Engineering Mechanics
IHPC aims to advance science and technology related to mechanics, the mechanical properties of materials and mechanical engineering by using and developing novel computational methods and techniques.
Our capabilities enable researchers to deal with the behavior of mechanical systems ranging from nano scale, through micro scale, and all the way to macro scale.
Utilising high performance computing (HPC) resources, our researchers are able to power four major research directions spread across different capability expertise.
A*STAR celebrates International Women's Day
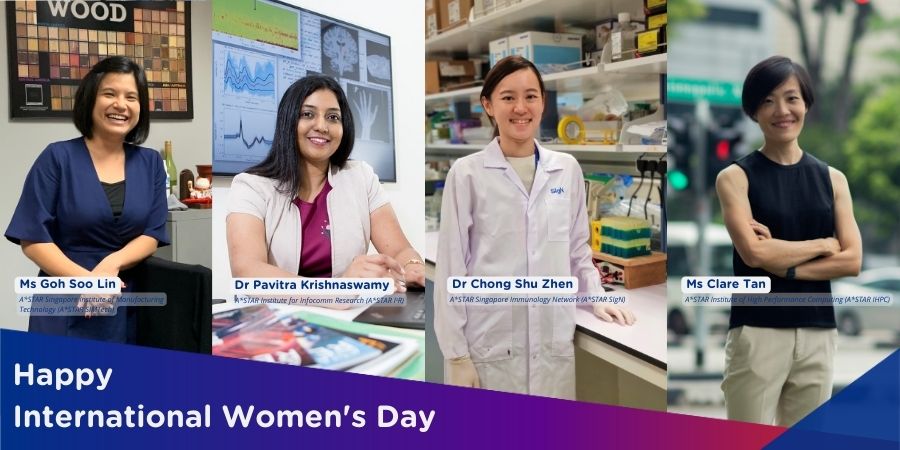
From groundbreaking discoveries to cutting-edge research, our researchers are empowering the next generation of female science, technology, engineering and mathematics (STEM) leaders.
Get inspired by our #WomeninSTEM