INNOVATE
How A*STAR's T-Up Programme Opened New Doors for Innovation with Univac
Mr Du Zhenglin (left), Senior Scientist at A*STAR’s SIMTech and T-Up Secondee, with Mr Sinclair Bateman (right), Head of Univac Group
In the ever-evolving world of manufacturing, companies must constantly innovate to stay ahead. Univac Precision Engineering (Univac) is a leading company in the precision engineering industry, involved in the design and manufacturing of precision assemblies and consumables across the pharmaceutical, medical, life science, consumer and automotive industries.
To maintain its competitive advantage, Univac sought to boost productivity and efficiency in its injection moulding processes. By leveraging A*STAR’s Technology for Enterprise Capability Upgrading (T-Up) programme, Univac not only improved its operational efficiency but also unlocked new opportunities for growth and sustainability.
Boosting Efficiency: Heat Management in Injection Moulding
One of the critical issues in injection moulding is managing the heat generated during the process. The cycle time—how long it takes for a mould to open and close before a part is produced—is heavily influenced by how quickly the material can cool after being heated. Traditionally, cooling channels are drilled into moulds to allow water to flow through, cooling the parts. However, this method is limited as it only allows for straight, vertical, or horizontal channels, which do not effectively cool parts with complex shapes and sizes. This inefficiency leads to longer cycle times, higher costs, and increased environmental impact due to wasted materials and energy.
Enhancing Innovation with T-Up
Through A*STAR's T-Up programme, Mr Du Zhenglin, Senior Scientist at A*STAR's SIMTech was seconded to Univac to address moulding efficiency challenges with Univac's engineers. Bringing his expertise in additive manufacturing, he supported the enhancement of Univac's approach to cooling in their injection moulding process. By leveraging 3D printing technology, the team designed conformal cooling channels (custom-shaped cooling paths that match the shape of the mould) that followed the contours of the moulded parts, ensuring uniform cooling and significantly reducing cycle times. This innovation allowed Univac to produce more parts in less time, reducing both costs and carbon footprint.
Uniform straight and conformal cooling channels
This collaboration significantly refined Univac's manufacturing process. Zhenglin worked with Univac's engineers to navigate the complexities of additive manufacturing, addressing challenges such as material selection and thermal management. This resulted in a fully optimised process that leveraged 3D printing to its fullest potential, significantly elevating Univac's operational standards.
Traditional drilling methods waste metal, but with 3D printing, Univac could use just the right amount of metal to create the mould, resulting in energy and material savings. The outcome of this collaboration was not just a more efficient manufacturing process, but also greener and more sustainable operations.
The Impact: Enhanced Revenue and Market Expansion
Zhenglin's contributions to Univac made a tangible impact on the business. Mr Sinclair Bateman, Head of Univac Group, shared that by introducing advanced manufacturing techniques, Univac was able to penetrate deeper into the medical sector. This proof of concept opened the door for recurring revenue as well, as customers gained confidence in Univac's capabilities and were willing to invest more in their services.
The collaboration also led to the creation of a new additive manufacturing hub within Univac, dedicated to developing innovative solutions through additive manufacturing techniques. This hub has become a platform for continuous improvement, exploring new areas such as 3D printing hybrid tools that combine machined and printed materials for cost-effective prototyping. These innovations have not only strengthened Univac's position in the market, but also enabled the company to offer faster and more efficient solutions to their customers.
Tooling insert before (left) and after (right) hybrid printing
Looking Ahead: A Partnership for Continuous Innovation
Univac's experience with A*STAR's T-Up programme has been a catalyst for ongoing transformation. Mr Bateman shared that Univac is keen to partner A*STAR for future projects, to explore new areas of innovation, including the potential for further advancements in 3D printing and other cutting-edge technologies.
A*STAR is a beacon of hope. The talent and state-of-the-art equipment we leveraged through the T-Up programme gave us the courage to innovate and it opened new doors that we never dared to explore before,
said Mr Sinclair Bateman, Head of Univac Group.
As Univac continues to broaden its innovative reach, Mr Bateman highlighted that this partnership with A*STAR will remain a cornerstone of its strategy, further reinforcing the company's position at the forefront of industry trends.
For Zhenglin, the T-Up secondment was an equally enriching experience for him. He shared, “I encourage fellow A*STAR scientists and researchers to join the T-Up programme to broaden your horizons, experience the whole value chain as you immerse yourself in the industry, and gain new insights that you may not usually have the opportunity to in research & development work. It was a wonderful experience, and I enjoyed speaking to a diverse range of people on the benefits of 3D printing.”
The T-Up collaboration has not only enhanced Univac's capabilities but also inspired a culture of continuous innovation that will drive the company forward for years to come. For local enterprises in Singapore, Univac's experience is a timely reminder that with the right support, boosting innovation is only a door away.
Was the article helpful?
A*STAR celebrates International Women's Day
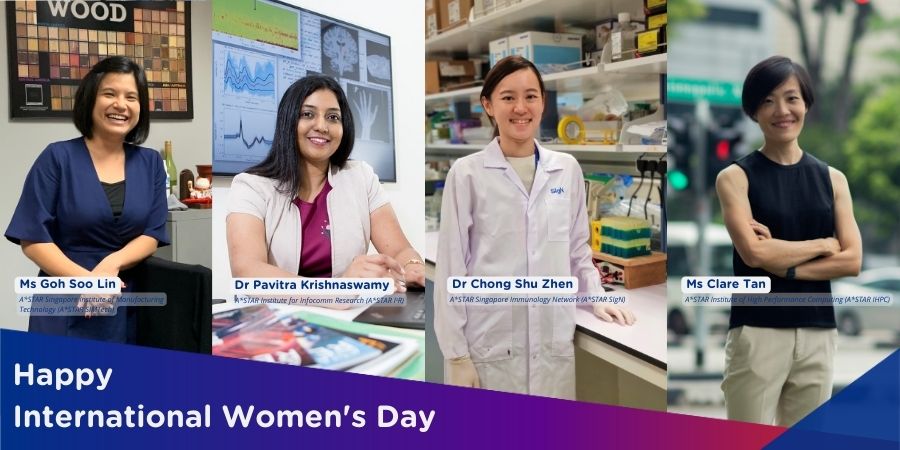
From groundbreaking discoveries to cutting-edge research, our researchers are empowering the next generation of female science, technology, engineering and mathematics (STEM) leaders.
Get inspired by our #WomeninSTEM