INNOVATE
How Golden Bridge Foods Digitalised to Feed its Appetite for Growth
Meet Singapore’s Tech Transformers, small and medium enterprises (SMEs) that are adopting innovation, embracing new technologies and digitalisation to meet the challenges of a disrupted business environment. Behind their transformation is a partnership with A*STAR. Its technologies and training propel these businesses to achieve their business goals. Here, learn more about the evolution of Golden Bridge Foods.
Luncheon meat. Stewed sliced pork. Chinese sausage. These mouth-watering meat staples in Chinese cuisine are the specialty of Golden Bridge Foods (GBF), a food manufacturer with humble beginnings as a factory with a handful of employees. Today, it is a regional powerhouse with 150 employees.
Since making a splash with its XO Special Lean Wax Sausages in 1993, the SME has expanded its offerings to Western-style and halal-processed meats to cater to the region’s diverse tastes. In fact, its products are enjoyed in countries as far afield as Mongolia today.
Madam Ong Chew Yong, GBF’s Director of Operations, shares her vision for the business. “We want to differentiate ourselves in taste, food safety and quality, product traceability and manufacturing speed,” she says.
Digital systems allowed GBF to manage data accurately, increasing productivity.
First Moves
In 2003, GBF kickstarted its transformation by adopting an enterprise resource planning system. The business management software allowed data from various business activities to be captured in an error-free manner. Since then, GBF has been able to collect high-quality data accurately while eliminating double entries, increasing the company’s productivity.
Mdm Ong admits that at the beginning, the transition was not easy. Aside from the financial outlay, the management also had to convince employees to embrace digital change. But by patiently guiding staff through the necessary reskilling and upskilling, the company eventually won them over, shares Mdm Ong. This experience would serve as an important lesson in the digital transformation journey ahead.
Eye-opening Technology
Seeking to boost its innovation capabilities further, GBF learned of A*STAR and its technologies in 2017. By the following year, the company adopted the Smart Manufacturing Operations Management (SMOM) system and eDatalogger. Both quickly became integral to operations.
“50 percent of our shopfloor was already automated but the rest used to be very manual,” explains George Tay, Senior Manager of Human Resources and Information Technology. In particular, work orders for the production line had to be filled in by hand, with only the beginning and end of the process captured. With various stations involved in each work order, the missing information made it challenging for management to analyse productivity, says Mr Tay.
The SMOM system digitalised the entire shopfloor process, providing complete visibility. Now, information is available for every part of the workflow, including the amount of time each station took and identity of the operator. The data has helped GBF improve its operations, such as identifying training gaps for staff, shares Mr Tay.
Similarly, the eDatalogger+ has helped to streamline the quality assurance process by digitalising a previously manual process. Forms used to be filled in by quality check inspectors by hand, Mr Tay explains. “Now, they just log everything in the eDatalogger and managers, quality assurance personnel and analysts can follow up.”
Ready, Set, Impact
Given their experience adopting the business management software system, GBF’s leadership team knew how crucial training was and ensured that staff had enough time to learn how to use the technologies before implementation. When the company adopted the SMOM system for instance, it received training support from SIMTech in developing operational scenarios and processes, as well as model fine-tuning, data analytics and optimisation. This allowed GBF to smoothly roll out the SMOM system and eDatalogger+.
Both technologies have had a dramatic impact on productivity, saving GBF staff a total of 1,450 hours spent on manually recording data each year. This has led to a 67 percent reduction in lead time from order to delivery and a 70 percent increase in manpower efficiency.
Digitalisation has helped the company remain resilient in spite of the pandemic, with production lines continuing to operate at full force, supported by the SMOM system and eDatalogger+. The company has even contributed to the national stockpile of canned and dried food, helping to meet the increased demand in food stock due to COVID-19.
A Ravenous Appetite for Growth
Golden Bridge Foods has milestones to adopt Industry 4.0 technologies over the next few years. To prepare for its next stage of transformation, the company leadership plans to undergo the Digital Transformation & InnovationTM programme, a joint initiative by A*STAR’s Singapore Institute of Manufacturing Technology (SIMTech) and the SkillsFuture. The programme aims to guide SME leaders in carrying out meaningful digital transformations for their businesses.
“We want to be one of the top food manufacturing companies in Singapore,” declares Mdm Ong. “We believe our collaboration with A*STAR will make this possible.”
The hope, says Mr Tay, is to one day extend GBF’s reach outside Asia, to the United States and Canada. “Even though we are a small SME now, we want to become a medium enterprise and then eventually, a global multinational company,” says Mdm Ong.
Was the article helpful?
A*STAR celebrates International Women's Day
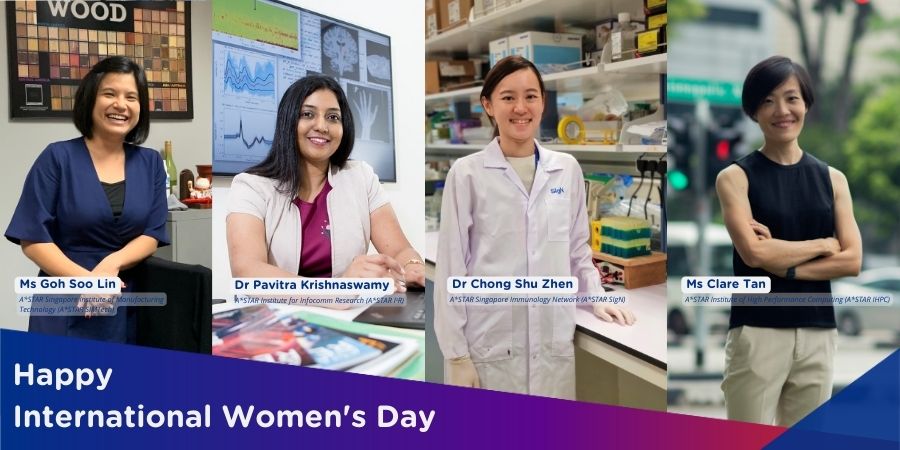
From groundbreaking discoveries to cutting-edge research, our researchers are empowering the next generation of female science, technology, engineering and mathematics (STEM) leaders.
Get inspired by our #WomeninSTEM