INNOVATE
Racer Technology’s Smart Factories Make the Singapore SME Shine
From left: Mr Kelvin Tan, Vice President of Quality Assurance and Regulatory Affairs at Racer Technology, Mr Lee Chia Ta, General Manager and Chief Operation Officer, Mr Kenny Lee, Chief Marketing Officer, and Mr Willy Koh, founder and CEO.
- Racer Technology initiated a partnership with A*STAR’s SIMTech in 2006
- Integrated four of A*STAR’s modular solutions to help drive its smart factory transformation
- Improved production yield and cost-savings of up to 70 per cent, following its transition to smart manufacturing
- Upskilled employees so they can keep up with technological trends
- This transition enabled Racer to sustain its operations during the COVID-19 pandemic
Meet Singapore’s Tech Transformers, small and medium enterprises (SMEs) that are adopting innovation, embracing new technologies and digitalisation to meet the challenges of a disrupted business environment. A smart factory represents a significant move to a more agile, interconnected system. As the manufacturing sector edges towards Industry 4.0, this is how local firm Racer Technology transitioned into smart production in partnership with the Agency for Science, Technology and Research (A*STAR).
The journey began in 1988. With a team of enterprising engineers, Mr Willy Koh, founder and CEO, launched a company dedicated to the design of medical products. Later, he expanded into end-to-end MedTech solutions such as surgical, patient-care and diagnostic devices. “There weren’t many local firms specialising in medical products at that time,” he says. “We bought a company and got ourselves ISO 13485-certified (for quality compliance) so we could design and manufacture medical devices independently.”
This conventional manual vertical moulding machine was transformed with an auto robotic and auto-feeding operation process, so that no operator is required. Previously, at least two operators were required.
Keeping a Competitive Edge
Without expertise to develop its own product solutions, Racer needed a strategy to stay ahead. In 2006, it established a partnership with the Singapore Institute of Manufacturing Technology (SIMTech), a research institute at A*STAR to tap its engineers and technological solutions. One success story was the development of a technology device which optimises the storage of blood plasma, for blood collection and processing. This was beyond its own engineering capabilities at the time. After working with SIMTech, Racer was able to research and co-develop the product for its growing customer base.
With the wfMobile solution, productivity improved by 50 per cent, on top of a 50 per cent reduction in paper usage due to digital reports.
Enhancing Productivity With A*STAR
To push the envelope further, Racer next set its sights on digitalising operations and improving production efficiency. In order to provide customised products and components that were in demand by its customers, Racer looked to SIMTech again to build its smart factories. The company was further encouraged by the financial support received from government agencies such as Enterprise Singapore (formerly known as SPRING).
Leveraging A*STAR’s Model Factory initiative for SMEs, the company adopted four modular solutions that were tailored to Racer’s manufacturing equipment and processes across its industrial units. The impact was clear — Racer experienced cost-savings and efficiency enhancements of up to 70 per cent, as well as improved real-time visibility on production schedules after the solutions were implemented.
In 2017, Racer also deployed SIMTech’s Manufacturing Operations Management (MOM) computer system, enabling the team to overcome time-consuming manual production planning and scheduling. “The system enables us to respond more efficiently to unexpected events like machine breakdowns or last-minute orders,” says Mr Kelvin Tan, Vice President of Quality Assurance and Regulatory Affairs. Their planning time which previously took up to 28 hours, was reduced to 10 hours per week as well.
Workflow Mobile (wfMOBILE) is another SIMTech solution that Mr Tan mentions with enthusiasm. The cloud-based tracking system makes it possible for Racer’s supervisors and managers to receive workflow progress updates on smartphones or tablets, enabling them to make decisions in real-time, even when they are off-site. wfMOBILE also enables the team to perform and share quality measurements digitally while ensuring data entry is accurate. Productivity improved by 50 per cent, on top of a 50 per cent reduction in paper usage due to digital reports.
Forging ahead, the company also integrated SIMTech’s Overall Equipment Effectiveness Monitoring System (OEEMS) and Inventory Tracking System (ITS) to optimise operations. Previously, a time-consuming paper-based method was used to track Racer’s machine operations, which was prone to human error. After integrating OEEMs with its injection moulding machines, Racer could receive real-time updates on machine stoppages, and rectify machine downtime issues in less than 30 minutes instead of over 45 minutes. This led to machine utilisation by 17 per cent, and an increase in production yield by 21 per cent. ITS, which uses an RFID system, enables Racer to better manage inventory by having greater visibility on stock levels or even track down missing items.
Racer makes it a point to upskill employees to keep them attuned to evolving technological trends. To date, two workers have undergone the Workforce Skills Qualifications course (Understand the Microfluidics Manufacturing Processes), while 15 employees have been trained by SIMTech under the Model Factory programme. The company also plans to create more value-added career opportunities, especially for local technical institute graduates.
Dealing With Disruption
The COVID-19 pandemic caused massive disruptions across the supply chain, and Racer wasn’t spared. With many staff working from home, it was challenging to sustain operations. “In hindsight, we are glad we digitalised our factories before the outbreak. We experienced minimal disruption in our factory operations, even with a smaller workforce on the ground,” Mr Tan explains.
Racer’s adoption of A*STAR’s technologies also aided production output during this difficult period, when the company was tasked with manufacturing face masks and personal protective equipment (PPE) for frontline workers. “These new initiatives actually enhanced our operations. We can get things done at a much faster pace. For example, we can turn around these face shields in less than a month, when we used to have the luxury of producing them in two to three months before the pandemic,” adds Mr Tan.
A Process Engineer recording and updating the control environment assembly process through the wfMobile tablet. Data is transmitted to the server and displayed at the shopfloor in real time.
By transitioning to smart manufacturing, Racer Technology has grown into a leading medical device and lab equipment manufacturer on the global stage, with eight factories across Asia. Specialising in product design, contract manufacturing and assembly, the firm’s portfolio now spans smart wearables and hearing aids, to test kits and handheld diagnostic devices. Having achieved a successful digital transformation, what’s in the pipeline?
“We are discussing with SIMTech the possibilities of developing an automated 3D-screening inspection station to be introduced at various stages of the engineering tooling and quality control process. With our digitalised approach, we hope to further reduce defective waste in real-time manufacturing,” Mr Koh concludes.
Was the article helpful?
A*STAR celebrates International Women's Day
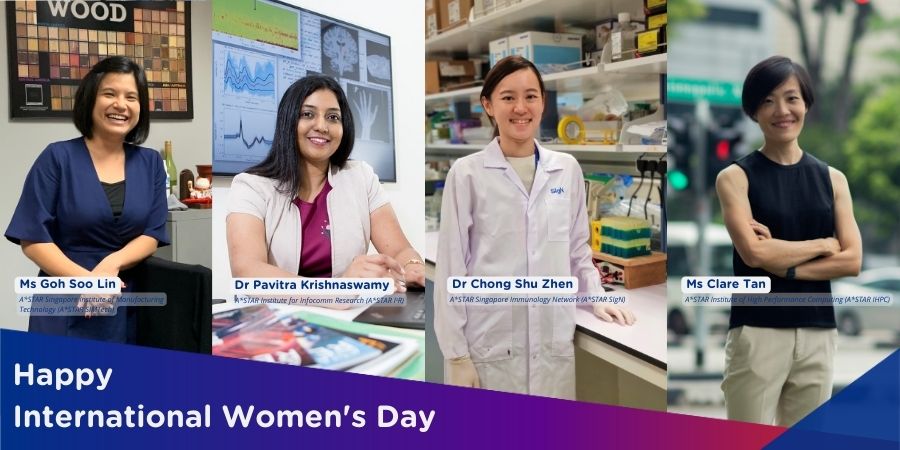
From groundbreaking discoveries to cutting-edge research, our researchers are empowering the next generation of female science, technology, engineering and mathematics (STEM) leaders.
Get inspired by our #WomeninSTEM