FACES OF A*STAR
Bringing Biologic Drugs to Market Faster and More Efficiently
- At A*STAR’s Bioprocessing Technology Institute, Senior Lead Research Officers Jessna Yeo and Mariati develop cost-competitive cell lines for biomanufacturing.
- Their team has developed a targeted integration platform for cell line development which reduces the average timeline for cell line development by three times, allowing biologics drugs to be developed and commercialised faster.
- The platform technologies have been licensed by companies to improve their capabilities in antibody development process.
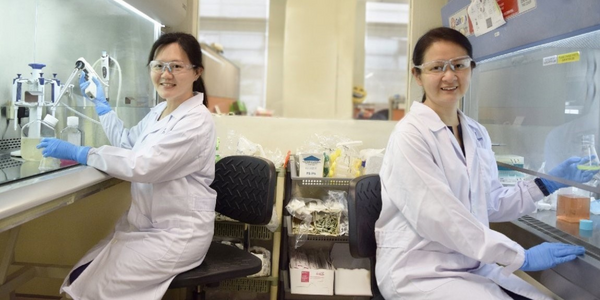
Biologic drugs made from living organisms have been used to treat diseases ranging from diabetes to cancer. Despite their diverse applications and effectiveness, biologics can be time- and labour-intensive to manufacture, raising costs and making treatment less affordable for patients.
Chinese hamster ovary (CHO) cells are commonly used cells to produce biologics. Therefore, developing high producing CHO cell lines can reduce the cost and duration of biologics production.
At A*STAR’s Bioprocessing Technology Institute (BTI) Cell Line Development (CLD) group, Senior Lead Research Officers Jessna Yeo and Mariati are working to develop cost-competitive cell lines for biomanufacturing. In this exclusive feature, they share about their research, and how they contribute to state-of-the-art technology in the biopharmaceutical field.
What are your areas of interest in research? And what motivated you to get into your field of expertise?
Jessna: During biology class in junior college, I found genetic engineering and biotechnology interesting. Following my studies at the National University of Singapore, I had the opportunity to complete my six-month industrial attachment with BTI and was assigned to the Animal Cell Technology group, which is now called the Cell Line Development (CLD) group. During the attachment, I gained insights to bioprocessing cell culture research and experienced wet lab experiments where I did cell line engineering and mammalian cell culture work, which I enjoyed. Upon graduation, joining BTI was a natural move and I have since been working in the CLD group.
Mariati: My research interests are expression vector and mammalian cell line engineering for the development of cell lines to produce biologics. Curiosity and the desire to achieve beneficial results in every experiment drives my work. It is my hope that the work I do will benefit society and the people around me.
What are some of the interesting projects that you are working on?
Jessna and Mariati: Antibodies are the best-selling drugs in the biopharmaceutical industry. They are produced in Chinese Hamster Ovary (CHO) cells, which is an epithelial cell line derived from the ovary of the Chinese hamster and commonly used in biomedical research. An important aspect of biologics manufacturing is the development of high producing CHO cell lines, which can affect the cost and duration of antibody production. Cell line development is also the bridge from the antibody development to clinical trials. After promising antibody candidates are developed, production cell lines need to be generated to produce enough amount of high quality materials for preclinical and clinical studies.
Our team has developed a CHO targeted integration platform for cell line development which reduces the average timeline for cell line development by three times - from over six months to under nine weeks - allowing drugs to be developed and commercialised faster.
The CHO targeted integration platform technology can also be used for accelerating the process of antibody development. Developing therapeutic antibodies remains a technically challenging, extremely time-consuming, high risk and costly process. CHO cells are the dominant host for antibody production. The transition from antibody development to production, which involves re-cloning of antibody genes and changes in antibody format and production host cells, increases duration and cost, and the failure of many antibody candidates. The platform enables a streamlined process to reduce the risk, time and cost of antibody development, and provides a powerful tool for various antibody engineering applications.
How does your research work bring impact to the industry?
Jessna and Mariati: Our platform technologies have significantly reduced the duration and cost of antibody development and production compared to existing technologies. They have been licensed by many companies to improve their capabilities in antibody development process. Our group has also used these technologies to support the companies’ needs through research collaborations and contract services, generating industrial revenue for businesses.BTI staff from the Cell Line Development group
What do you like most about what you do, and why?
Mariati: Daily experiments can be seen as mundane tasks but I like how I can work together with my team whenever we face challenges and roadblocks in the process. We have a culture of encouraging and mentoring each other to learn new things and achieve our goals together.
Jessna: The versatility of our work - Unlike a deskbound job that can be routine, doing research offers the flexibility to explore different research ideas and design different experiments to test one’s hypothesis. I like that there is a balance of hands-on wet lab and desk work. There are always opportunities to learn and contribute to state-of-the-art technologies in the biopharmaceutical field.
Was this article helpful?
A*STAR celebrates International Women's Day
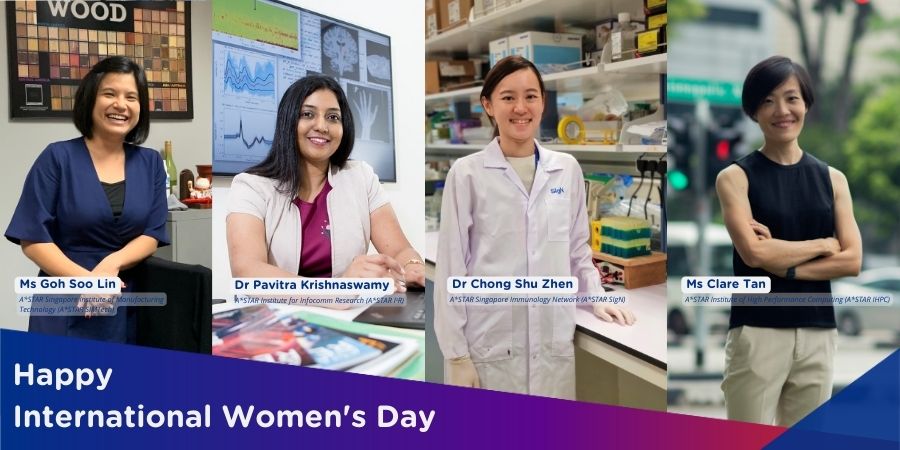
From groundbreaking discoveries to cutting-edge research, our researchers are empowering the next generation of female science, technology, engineering and mathematics (STEM) leaders.
Get inspired by our #WomeninSTEM