Creating A Factory “Smart” Enough to Operate in the Dark
Meet Singapore’s Tech Transformers, small and medium enterprises (SMEs) that have adopted innovation, embraced new technologies and digitalisation to meet the challenges of a disrupted business environment. Behind their transformation is a partnership with A*STAR, involving training and the adoption of technologies to achieve their digital goals. Here, learn more about the evolution of Fong’s Engineering and Manufacturing.
When Fong’s Engineering and Manufacturing CEO Mr Jeremy Fong first toured Shanghai’s factories several years ago, it sparked his decision to pursue a smart factory transformation. Seeing how large sections of the factories there had unmanned operations made him realise how much further ahead the Chinese were in the latest manufacturing technological trends.
“I realised that if we didn’t move fast, we would have a problem,” he says.
This gave Mr Fong a unique goal for his SME’s own factory: to operate in the dark. “If everything was automated and done by robots, we wouldn’t need lighting,” he explains, adding that such a factory would also be able to operate round the clock.
On the Right Track
Today, 50 percent of Fong’s factory has been digitalised, including one of its production lines which was successfully automated last year. Mr Fong shares that the transformation would be complete in 2021, and he expects a 20 percent year-on-year revenue growth and 30 percent increase in productivity by then.
Meanwhile, the COVID-19 pandemic has already made the benefits of a smart factory evident.
Despite facing a shortage of skilled workers on its production line due to movement restrictions, the company’s output remained relatively stable, according to Mr Joseph Wong, Project Manager, Technology and Transformation, Smart Manufacturing.
“The unmanned capabilities afforded by our smart production lines helped us cushion the impact of manpower shortage,” he explains. The fact that these automated capabilities withstood such stress-testing also signalled to management that they were headed in the right direction in transforming the factory, adds Mr Wong.
The Guiding Hand in Transformation
“We didn’t just want to transform the workplace — we wanted to transform the business,” says Mr Fong on the decision to march the company towards Industry 4.0. Yet, he is also clear-eyed on the company’s capabilities. “Our expertise lies in manufacturing, not automation,” he says.
Therefore, when Fong’s wanted to pursue the goal of achieving a “lights out” factory, the leadership team turned to A*STAR, which has been advising the business on medtech devices through SIMTech’s Precision Engineering Centre of Innovation for the past nine years.
“A*STAR helped to plug the gap,” says Mr Wong. “Besides tapping into its technologies, we were able to access its wide network of industry partners and contacts, and identify relevant vendors who could help with installation.”
Fong’s first learned to devise a roadmap for its digital transformation using the Smart System Framework. The framework helped Fong’s better understand its capabilities and existing machinery, shares Mr Wong. This informed the gaps within the company and the technologies they needed to adopt to transform.
New Eyes on the Shopfloor
To find out about the latest developments in manufacturing, the management team paid a visit to the Model Factory@SIMTech — a co-innovation platform where industry partners can collaborate with researchers to testbed technologies in advanced manufacturing. Here, one piece of technology caught their eye: the Real Time Dashboard.
Mr Fong and Mr Wong recognised that the dashboard could propel the company along its digital transformation, and pursued it as part of Fong’s bid to enhance its shopfloor connectivity. “Previously, we used a whiteboard for production monitoring, which was prone to human errors,” explains Mr Wong. “The dashboarding technology helps capture accurate data automatically.”
The dashboarding technology pulls out data from multiple sources across Fong’s production floors, and allows the company to track its production and operational performance in real-time, and respond swiftly to unexpected events such as machine breakdowns. The smart technology improved productivity by up to 40 percent.
Knowledge transfer from A*STAR is also crucial for effective technology adoption. Under the agency’s Technology for Enterprise Upgrading programme, a researcher from SIMTech was seconded to train the company’s engineers on data acquisition over the course of nine months.
Everyone Gets Trained
The road to transformation was not without its bumps. According to Mr Fong, staff initially had trouble getting used to the new technology. The management team thus sought the help of Singapore Polytechnic, which studied the skill gaps that needed to be addressed and helped Fong’s put together a training roadmap. The company also converted several rooms into a dedicated training facility equipped with smart boards and movable tables to create a conducive place for staff to be trained.
Fong’s conducted in-house staff training workshops on digital readiness to prepare its staff for Industry 4.0
Unsurprisingly, the leadership team strongly advocates lifelong learning, believing it to be key to the company’s success in its Industry 4.0 transformation. “It’s a company-wide mindset, from the cleaner to the CEO,” declares Mr Fong. He explains that cleaning a smart factory properly entailed more than mops and brooms — it required specialised cleaning equipment and knowledge of how to operate them.
Going Forward, Together
Mr Fong credits Singapore’s supportive enterprise ecosystem as one of reasons the company has been able to find success in its digital transformation. From learning trips coordinated by Enterprise Singapore to employment placements organised by the Employment and Employability Institute, “different organisations have helped boost our capabilities in different ways,” he says.
As the company continues to chart its course towards Industry 4.0, Fong’s has ambitious plans to leverage big data and cloud computing to achieve its goal of an unmanned smart factory. It also plans to tap into artificial intelligence for inspection during the manufacturing process. The company is also learning how to anticipate the impact of more nascent technologies such as 5G and blockchain, shares Mr Wong.
“We hope that Fong’s can be a model for other SMEs in Singapore,” says Mr Fong, recounting how traditional and manual their operations used to be. “It took pain to transform, but it was worth it.”
A*STAR celebrates International Women's Day
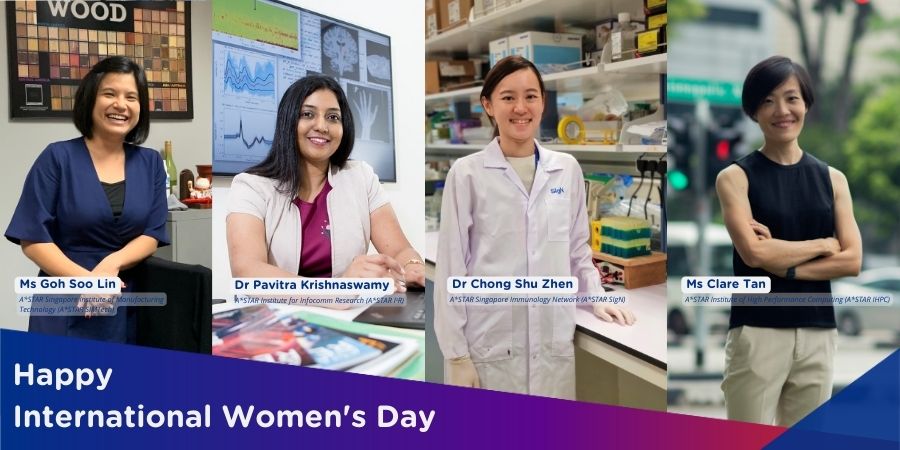
From groundbreaking discoveries to cutting-edge research, our researchers are empowering the next generation of female science, technology, engineering and mathematics (STEM) leaders.
Get inspired by our #WomeninSTEM