This Singapore SME is Riding Waves of Innovation to Industry 4.0
- In 2013, Banshing Industrial collaborated with A*STAR to strategise and position the company for Industry 4.0
- Boosted production throughput and manpower efficiency with the adoption of A*STAR’s solutions
- Automation of laborious processes enabled employees to focus on high value work
- Reaped the benefits of upskilling its workforce, notably in weathering the COVID-19 pandemic
Meet Singapore’s Tech Transformers, small and medium enterprises that embody the spirit of innovation. They embrace new technologies and digitalisation to thrive in a challenging business environment brought on by the global pandemic. To drive their transformation, they team up with the Agency for Science, Technology and Research (A*STAR), which offers technologies and training. Banshing Industrial shares its success story.
In 1975, Banshing Industrial was established as a plastic injection moulding house, servicing just one client. Four decades later, it is an international group that specialises in custom moulding for precision engineering components. Clearly, Banshing Industrial has long understood the importance of transforming its business model and adopting technology and innovation to stay relevant.
This strategy led Banshing to collaborate with A*STAR about seven years ago to co-develop technologies through programmes such as the Operation Technology Roadmap (OTR) and Technology for Enterprise Capability (T-Up). The company also invested in automation with support from SPRING Singapore (now known as Enterprise Singapore).
Mr Alvin Cheng, 32, Director and second-generation leader at Banshing, hopes to continue harnessing technological innovations, including automation, to best position the company for the digital age and “Industry 4.0”.
“My viewpoint has always been that nobody knows exactly what Industry 4.0 is going to bring. We only know that it is going to be a wave of change,” he says. “And when you look back at all the previous industrial revolutions, there are only two outcomes: you either ride the wave of change, or you stand still and fall.”
Industry 4.0 represents the digital transformation of manufacturing and production systems, through the use of the digital industrial technologies such as robotics and automation, and the Industrial Internet-of-Things (IIoT), that can enhance productivity and competitiveness.
Preparing for Change
When Banshing first started working with A*STAR’s Singapore Institute of Manufacturing (SIMTech), the latter facilitated a workshop for the company’s executive Singapore team to assess its market and business drivers. They also built a first cut of its OTR, which helped the company strategise and chart its technology priorities. This kick-started its digital transformation journey.
Like many others in its industry, Banshing relied heavily on the manual filing and tracking of its sales and production orders. To improve productivity and efficiency in the company, Banshing adopted A*STAR’s Smart Manufacturing Operations Management (S-MOM) and Overall Equipment Effectiveness Monitoring System (OEEMS), blending these solutions into its existing Enterprise Resource Planning (ERP) system.
With that, the company was able to automate the process of creating and tracking sales and production orders, and have real-time visibility into its operations.
S-MOM allows real-time production monitoring, providing data to help generate customised reports to improve production. One example is the customisable scrap report, which serves as a document to track disposal of scraps or materials leftover from production. This also helped Banshing avoid human errors that could arise from manual monitoring. Meanwhile, the OEEMS, which was implemented on eight machines, helped the company reduce idle time loss from 112 hours per month to four hours per month. This 96 per cent reduction in idle time loss saves the company $23,800 each month.
The automation of such tedious, laborious work, also means that employees now have the time to focus more on higher value work, shares Mr Cheng. “Whatever solution we invest in has to be pragmatic, and it has to improve our productivity,” he adds. The S-MOM and OEEMS helped Banshing increase its throughput by more than 70 per cent, while manpower efficiency for production supervisors was also up 70 per cent.
Upskilling for the Future
The implementation of the solutions, however, required the upskilling of workers and a change in their attitudes towards technology adoption. “People don't like change. Why fix something if it's not broken? That's always been their mindset,” Mr Cheng says.
Banshing’s employees were sent for training in new moulding techniques, and that built a foundation for the company’s next steps in automation and Industry 4.0. They were also encouraged to participate in masterclasses in advanced manufacturing organised by SIMTech.
While upskilling workers and inspiring them was no easy feat, he says that employee morale has increased as workers now see the benefits of these solutions. “Not only is it improving productivity, but it’s also getting the general population of employees more comfortable with using different kinds of software and technology,” he explains.
Investments in these technologies and upskilling of workers paid off, as the solutions were especially useful during the COVID-19 pandemic. The closed borders between Singapore and Malaysia due to the pandemic had cut off a large portion of Banshing’s workers, leading to a manpower crunch. “The monitoring and execution tasks that were automated, or made much easier, definitely helped our workforce cope with the labour shortage and maintain a level of reporting quality,” he says.
The pandemic has also proven that technology will continue to play a big role in Banshing’s operations. To help workers thrive in this digital age, Mr Cheng hopes to build and encourage a culture of learning by providing more training opportunities for Banshing’s workers.
“If I can ensure the survival of the company, and at the same time, not forget the individuals that make up the organisation, I’ll be very happy,” he says.
A*STAR celebrates International Women's Day
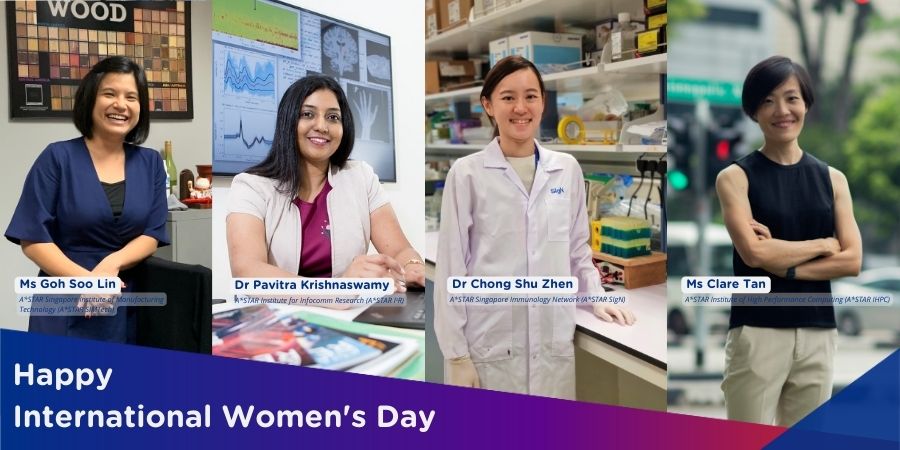
From groundbreaking discoveries to cutting-edge research, our researchers are empowering the next generation of female science, technology, engineering and mathematics (STEM) leaders.
Get inspired by our #WomeninSTEM