The Future of Advanced Manufacturing is here
By Mr. Lim Chuan Poh, A*STAR Chairman
From making cocktail trays for planes to 3D metal printing and using data analytics, manufacturers are getting a transformative boost with programmes from the Agency for Science, Technology and Research.
Manufacturing has been the topic of discussion at the World Economic Forum (WEF) for the past two years. And for good reason.
Its white paper, "Manufacturing Our Future: Cases on the Future of Manufacturing", published in May last year, points out that an industrialised nation's economy largely depends on its manufacturing sector.
In its introduction, the white paper declares: "The link between a thriving manufacturing sector and economic growth is a direct and significant one, particularly regarding employment and industries that themselves are linked. In fact, manufacturing has the largest multiplier effect of any economic sector."
This is also pertinent for Singapore, where manufacturing makes up about a fifth of the country's gross domestic product. The report of the Committee on the Future Economy (CFE) released in February reiterates that the manufacturing sector "generates strong spillovers to the rest of the economy" through its close engagement with other sectors, such as wholesale trade and business services.
Several countries are now talking about Industrie 4.0. The term refers to the fourth industrial revolution journey and was coined by the Germans to promote the digitalisation of manufacturing for an era of high-mix, low-volume production.
Its relevance for Singapore is that to survive in this age of technological disruption, local small and medium-sized enterprises (SMEs) - thousands of which are in the manufacturing sector - must adapt and transform to remain relevant and competitive.
Countries with significant manufacturing in the economy, such as China, Japan and Germany, are embarking on Industrie 4.0 to position themselves for the future. Singapore has to do likewise to be a preferred hub for multinational corporations (MNCs) and large local enterprises (LLEs) to site their Industrie 4.0 factories.
At the Agency for Science, Technology and Research (A*Star), we have worked on more than 1,700 industry projects in financial year 2016, with around a third done in collaboration with SMEs. About half of these SME projects were manufacturing-related. These are spread across industries, with the key sectors being precision engineering, electronics and pharmbio.
A look at some of A*Star's research collaborations in the advanced manufacturing sector highlights the potential to transform this sector.
CLOSING THE GAP
A*Star has a slew of different programmes to help SMEs and LLEs in advanced manufacturing to close technological gaps so they can access higher-value work and fit into the global supply chain of MNCs in the oil and gas, medtech and aerospace industries that have set up shop in Singapore.
Home-grown precision engineering company Meiban in 2011 took part in a Gun Drill Collaborative Industry Project (CIP) initiated by A*Star's Singapore Institute of Manufacturing Technology (SIMTech) and led by multinational energy product and service provider Halliburton. Over 20 companies, big and small, got together to jointly develop capabilities to level up the local precision engineering industry for the global oil and gas sector.
Through meetings with major oil and gas original equipment manufacturers (OEMs) in Houston, SIMTech worked with Meiban Group for the launch of a deep-hole drilling services company. The $10 million drilling production facility started out with a team of 35 engineers, machinists and operators. The company then installed a 30m deep-hole drilling machine - reputed to be the longest in South-east Asia at the time - to produce high-performance oilfield equipment for the OEMs.
Likewise, in the aerospace sector, collaborative industry projects have also been launched. SIMTech worked with TNC Optics & Technologies, Fong Shen Mould & Precision Engineering, LNE Holdings and Maxservo Technology to upgrade their capabilities in design, simulation and manufacturing processes of aircraft interior parts to meet stringent aerospace standards. These companies now supply interior parts such as cocktail trays and armrests to an aerospace MNC.
TAKING ON INDUSTRIE 4.0
Big manufacturers have already embarked on their Industrie 4.0 journey. Local SMEs must therefore keep pace if they want to be part of the high-value advanced manufacturing ecosystem.
Among the big boys in Singapore, Rolls-Royce is going digital with its operations, to have an overview of its products' life cycle as the company transforms its aerospace engineering and other engine-related businesses through the adoption of Internet of Things and advanced data analytics. It can then offer value-added services such as predictive maintenance to its customers, and capture market share in the future economy.
In January, Rolls-Royce chairman Ian Davis was in Singapore for the signing of a memorandum of understanding with A*Star to set up joint technology centres on Future of Manufacturing (FoM) capabilities in areas such as advanced technologies for manufacturing, assembly, maintenance, repair and overhaul. The idea is to get local enterprises to participate in a synergistic value chain on an Industrie 4.0 platform. This way, big manufacturers' experience can help smaller companies.
SMEs that prefer to take incremental steps in adopting technologies to improve efficiency could turn to Tech Depot, a whole-of-government initiative launched on April 20. This is a new addition to Spring's SME Portal, and it showcases ready-to-go solutions such as those that improve machining and business processes.
So far, more than 300 companies have benefited from plug-and-play technology solutions offered by SIMTech since 2013. These enterprises reported productivity improvements of up to 200 per cent.
Later this year, companies can make use of A*Star's advanced manufacturing facilities and tools, and tap advice under the new Tech Access initiative. The companies can then go on to acquire relevant equipment to capture new business opportunities.
Home-grown SME 3D Matters, which offers polymer 3D-printing services, participated in the SIMTech collaborative industry project on additive manufacturing last year. The company picked up capabilities in 3D metal-printing technologies and recently established a new company, 3D Metalforge, to produce customised metal parts for the heavy machinery industries. This week, 3D Metalforge launched its $2.5 million facility that offers a complete range of in-house metal- printing services.
By the end of this year, A*Star will also be establishing model factories at two locations: at the Advanced Remanufacturing and Technology Centre (ARTC), and at SIMTech. These allow companies to learn about the latest manufacturing technologies and collaborate with stakeholders to test-bed and jointly develop innovative solutions.
The end goal is for SMEs to adopt, in part or whole, the Model Factory platform on their own factory floors. This may be a challenge for many smaller local enterprises. But some have taken the plunge as early adopters and the benefits to them are clear.
MODEL FACTORY: EARLY ADOPTERS
Since late 2015, SIMTech has been working with local precision engineering SME CKE Manufacturing on linking five of its machines to the Manufacturing Control Tower platform, a key feature of the Model Factory @ SIMTech.
Currently, CKE's staff can track simultaneously the performance of all the machines digitally, and tap the data to plan future operations.
Another early adopter is Feinmetall Singapore, a local SME that manufactures probe cards for semiconductor tests. It is embarking on its Industrie 4.0 journey and, later this year, will be digitalising its machines for improved performance.
SME Sankei Eagle worked with consulting firm McKinsey & Company and ARTC to co-develop an Industrie 4.0 model assembly line. The pilot demonstrates the viability of using digital technologies in manufacturing lines for a globally connected business and operations network. Through this project, Sankei Eagle gained insights on analytics and data tracking, which will be valuable in its future business.
By embarking on the Industrie 4.0 journey, these SMEs place themselves ahead of their competitors in seizing new business opportunities.
As Minister for Trade and Industry (Industry) S. Iswaran pointed out in his address at SME Day last month, "While the Government can create a conducive environment for innovation and technology adoption, the onus is on SMEs to appreciate the potential, seek out solutions, and execute them effectively in order to realise the full benefits."
The time for SMEs to move towards Industrie 4.0 is now.
This article is also available in The Straits Times on 20 May, 2017, with the headline The future of advanced manufacturing is here.
A*STAR celebrates International Women's Day
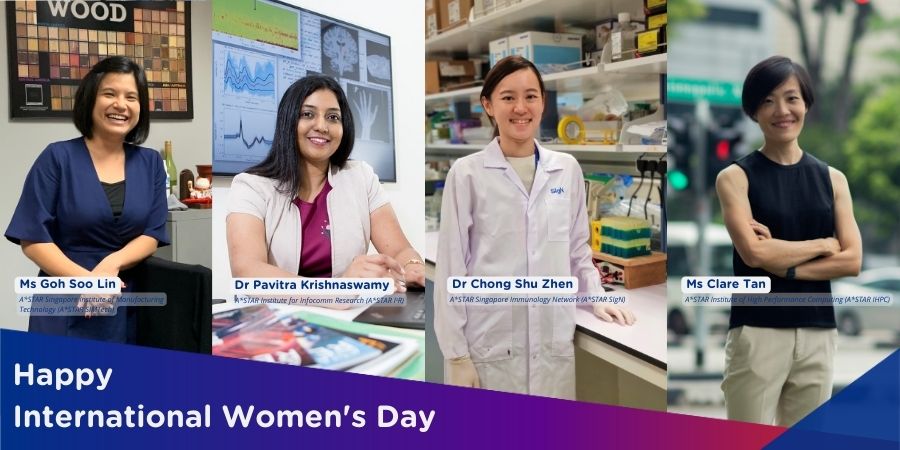
From groundbreaking discoveries to cutting-edge research, our researchers are empowering the next generation of female science, technology, engineering and mathematics (STEM) leaders.
Get inspired by our #WomeninSTEM