INNOVATE
Soaring High With Innovative Aviation Technologies

Ready to take flight as borders reopen? From producing sustainable aviation fuel from CO2 to improving aircraft monitoring with built-in smart sensors – discover our latest innovations to enhance sustainability and efficiency in the aviation industry!
Producing Sustainable Aviation Fuel From Co2 With Novel Energy-efficient Technology
A*STAR has been developing a streamlined process to produce sustainable aviation fuel directly from carbon dioxide (CO2 ), with the aim of contributing to the decarbonisation of the aviation industry.
CO2 can be recycled to produce carbon neutral jet fuel, replacing the use of fossil fuels that traditionally power aircraft, which is carbon positive and contain more pollution-causing impurities. This is in line with Singapore’s Long-Term Low-Emissions Development Strategy (LEDS), which aims to halve the country’s CO2 emissions from its peak of up to 65 million tonnes in 2030 to 33 million tonnes by 2050.
The new direct conversion process, which combines both CO2 and hydrogen (H2 ), marks an improvement from existing indirect conversion technologies, which require CO2 to first be converted to carbon monoxide (CO) or extracted from waste biomass, before aviation fuel can be produced. Using a unique catalyst developed by A*STAR’s Institute of Chemical and Engineering Sciences (ICES), the direct conversion process streamlines multiple reactor steps into one single step, with benefits including energy, space and monetary savings, as well as a more efficient yield of aviation fuel. A*STAR’s Institute of High Performance Computing (IHPC) provided the machine learning capabilities to speed up the catalyst development, while the techno-economic analysis, life cycle assessment and life-cycle cost analysis was done by ICES and A*STAR’s Singapore Institute of Manufacturing Technology (SIMTech).
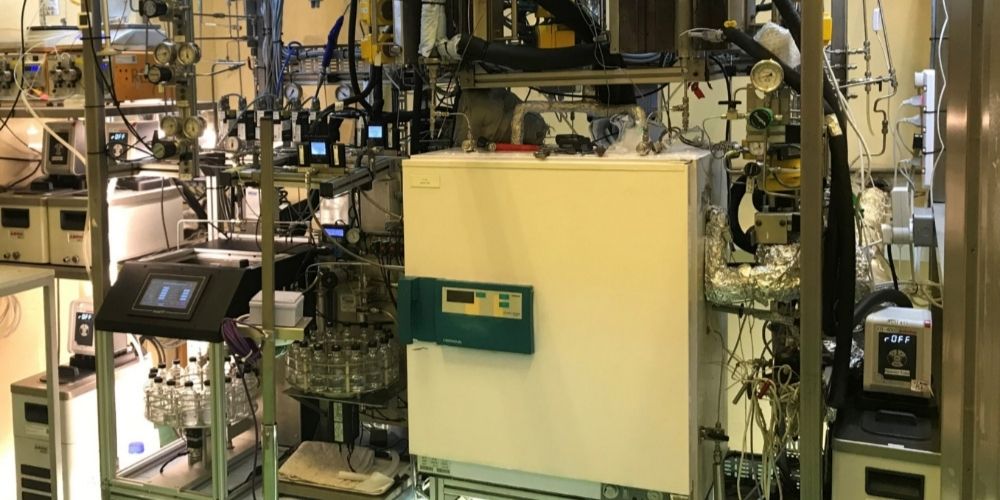
The team is currently in the catalyst development phase to further optimise the current first-generation catalyst. Future R&D plans include collaborating with various parties to scale up and integrate the technology for industrial use.
Developing Innovative Smart Sensors For Automatic Aircraft Monitoring
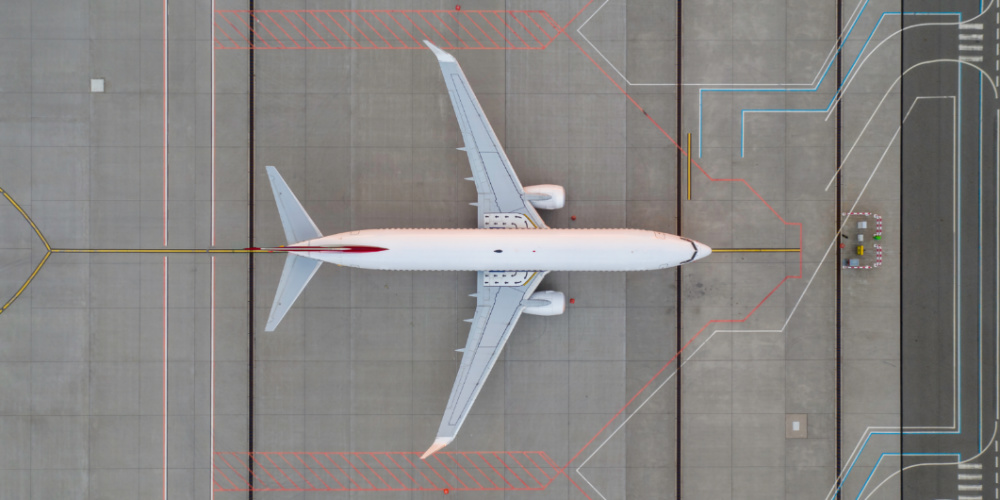
A*STAR is developing next generation direct-write (DW) ultrasonic sensors for aircrafts which offer enhanced capabilities like automatic structural health monitoring and efficient preventive maintenance.
Currently, ultrasonic inspection conducted in the aviation industry involves the use of handheld ultrasonic probes or manual installation of bulky ultrasonic sensors on aircrafts, which are labour-intensive, costly and may result in inconsistent outcomes.
The project involves researchers from A*STAR’s Institute of Materials Research and Engineering (IMRE), Institute of High Performance Computing (IHPC), Institute of Microelectronics (IME), and National Metrology Centre (NMC).
The team from IMRE is developing new light and compact DW ultrasonic sensors which are able to offer real-time monitoring capabilities, highly-consistent performance, as well as space and cost savings. Working together with IMRE to realise structural health monitoring functionalities with the DW sensors, IHPC conducted ultrasonic modelling and simulation, IME developed the electronic systems, and NMC provided metrology expertise for sensor performance evaluation and test protocols to be industry-recognised.
A network of these DW ultrasonic sensors can be built directly on the aircraft’s structural parts as a coating using in-situ deposition and patterning method. They can generate and detect acoustic waves in an aircraft’s structure and transfer the signals into useful data that shows the aircraft’s structural integrity. By automatically monitoring the aircraft’s operational and structural conditions, preventive maintenance can be done in a more efficient and accurate manner compared to scheduled inspections, where monitoring is done at set intervals without accounting for the actual condition of the aircraft.
The use of DW sensor technology marks a promising step towards implementing a scalable sensor network with improved reliability for automated structural health monitoring. Created using technology patented by A*STAR, the sensors have undergone environmental testing, with plans for further collaboration with industry partners to explore applications in the aviation industry.
Was the article helpful?
A*STAR celebrates International Women's Day
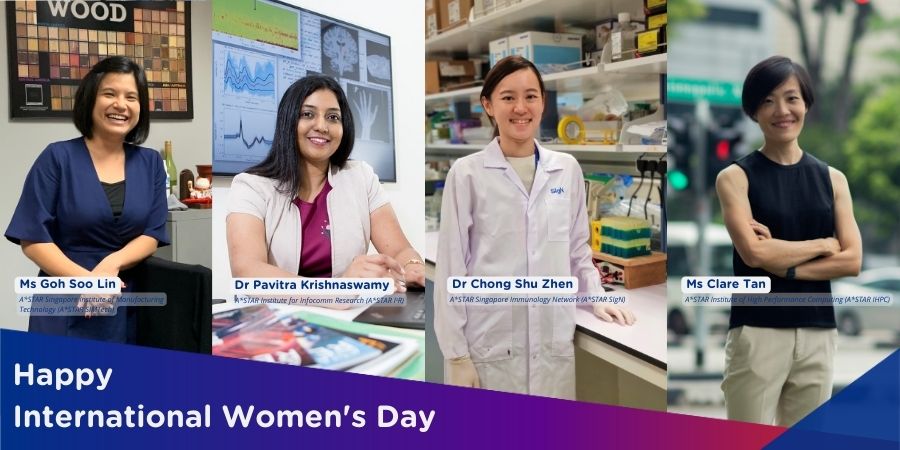
From groundbreaking discoveries to cutting-edge research, our researchers are empowering the next generation of female science, technology, engineering and mathematics (STEM) leaders.
Get inspired by our #WomeninSTEM