INNOVATE
Why did this company work with A*STAR to codevelop 27 technologies
Since 2006, Component Technology and A*STAR have worked on several industrial projects together and co-developed 27 key technologies in wire bond inspection.
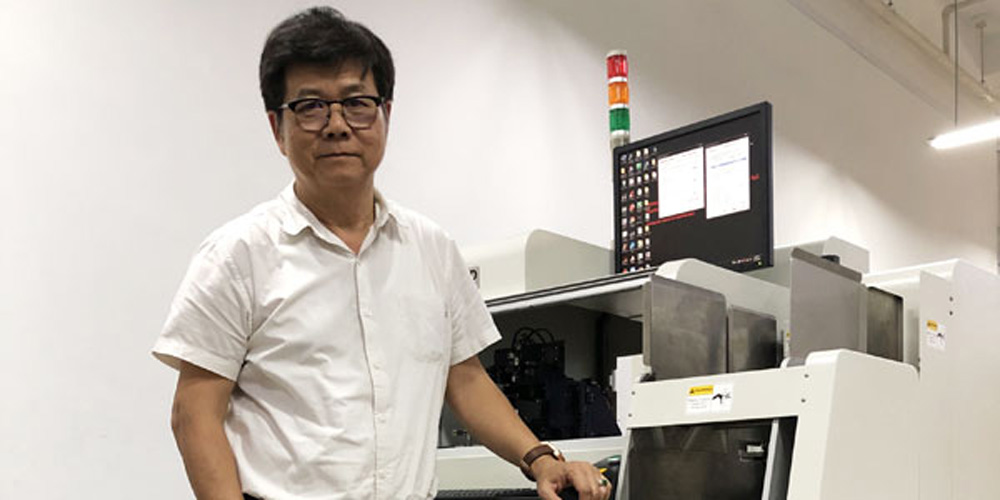
Component Technology CEO and managing director Berne Chung with the first-of-its-kind 3D automated wire bond inspection system his company developed in collaboration with A*STAR.
Transformation is the latest buzzword for Singapore businesses, but Component Technology has been ahead of the game for several years now.
Now an original equipment manufacturer, the company had been distributing machinery to the local semiconductor industry for more than 10 years since its founding in 1989, when CEO and managing director Berne Chung sensed a need to change tack in 2003.
In that year, we had a product (for) which we were the world’s top performer in 2000, for selling it. Then it went through three cycles of selling, and the product became outdated.
It makes you feel that no matter how well you do, something could happen to the supplier, then your future is gone. So we decided to take our future in our hands.
Berne Chung, CEO and Managing Director
Following up on an old email from A*STAR’s Singapore Institute of Manufacturing Technology (SIMTech), he approached A*STAR to explore product development as a higher-value process for his company. Since 2006, Component Technology and A*STAR have worked on several industrial projects together and co-developed 27 key technologies in wire bond inspection.
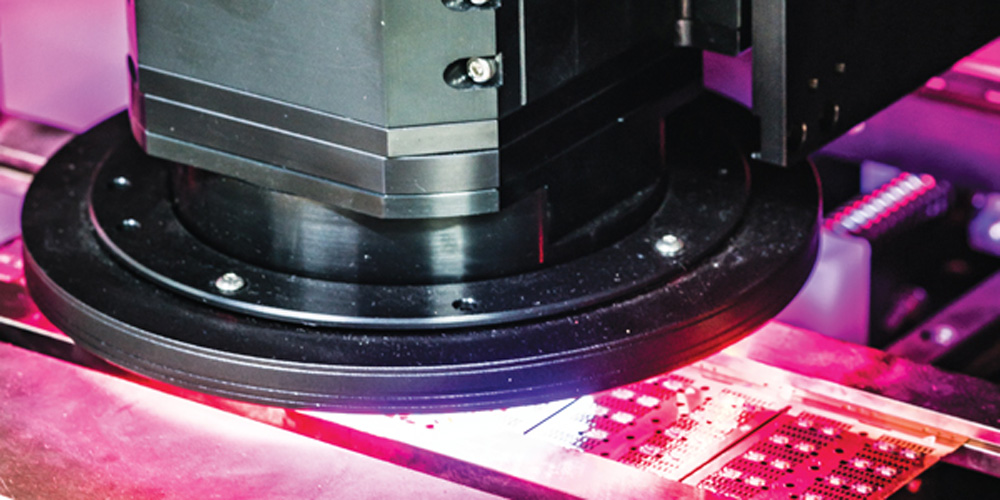
These collaborations resulted in a first-of-its-kind 3D automated wire bond inspection system, which Component Technology exhibited at the Hannover Messe trade show in April when The Business Times spoke with Mr Chung.
Using algorithms and triangulation technology jointly developed with A*STAR, the machine inspects the interconnections between wires to confirm that they are up to standard. This process is normally conducted by comparing the product to a “golden image”, but Component Tech’s machines can go further than just identifying the problem areas. It can measure the exact differences and from those values, provide clues as to which part of the manufacturing process resulted in the defect.
This machine proved to be a turning point for the company’s prospects, Mr Chung said, as a series of events in the following years proved his hunch that the distribution model was unsustainable. For instance, Component Tech lost the distribution rights to one of its best-selling products, while another product was lost when the supplier closed down the relevant department.
(These events) dragged on until 2013, when we no longer represented anybody else, and the business completely changed, so now we make our own products to sell
Our customers are famous IDMs (integrated device manufacturers) in the semiconductor industry, and now we are going after the Chinese manufacturers.
Mr Chung said.
The cost savings are the key value proposition for the machine. “Incorporating our product, customers can get a return of investment within a year,” Mr Chung said. “On top of that, no human judgment error, no sick leave, and no worries that other people will poach your skilled labour force.”
Since the company started selling the 3D inspection machines around end-2009, it has sold more than 570 units and netted an estimated S$47 million in revenue. The product also spurred Component Tech to expand its staff strength from about 20 in 2006 to 130 today with operations in Singapore, China, Taiwan, the Philippines, Thailand and Malaysia.
Working with A*STAR and SIMTech was crucial for a small business like Component Tech because it did not have the capabilities to develop new technology on its own, said Mr Chung. However, he emphasised that companies need to be clear about their needs and goals in such projects.
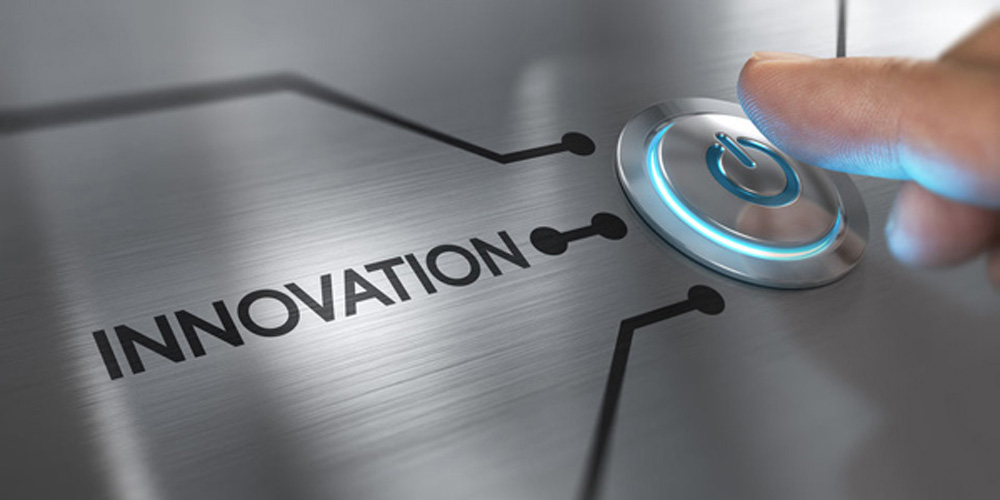
“We tried to make some products before, but being amateurs, we made very amateurish products,” he said. “And even with A*STAR’s assistance to our local industry, the (firms) really need to know exactly what they want. The first project we did with A*STAR actually failed, because we didn’t know exactly what we wanted.”
Component Tech and A*STAR will continue working closely together - the company will take part in the Technology Extension Partnership Programme, which develops strategic local partners to commercialise SIMTech technologies, and then builds up their capabilities and supports them in their internationalisation efforts.
Currently, Component Tech licenses the jointly developed wire inspection technology from A*STAR and derives recurring income from spare parts. In future, it plans to provide upgrades such as artificial intelligence capabilities so the machines can handle more complicated applications. It also plans to develop similar technology for wafer inspection, as it ventures into serving other parts of the manufacturing supply chain.
Collaborate with A*STAR
Companies interested to collaborate with A*STAR, can visit us at: www.a-star.edu.sg/simtechWas the article helpful?
A*STAR celebrates International Women's Day
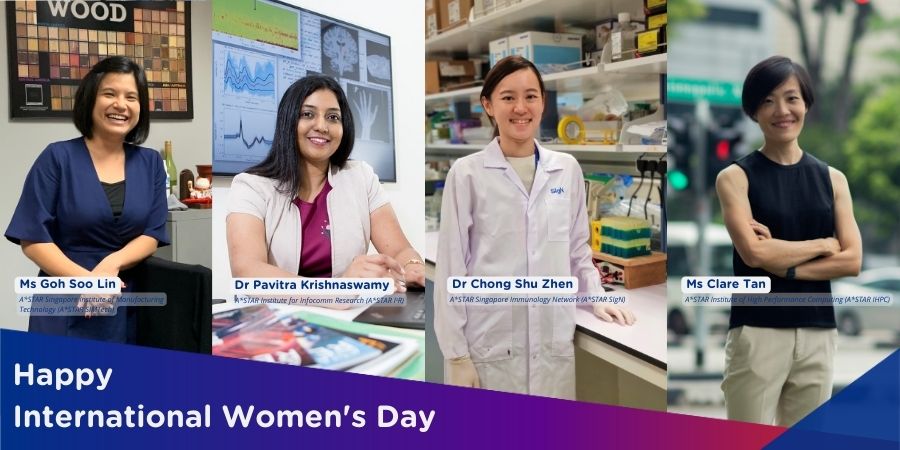
From groundbreaking discoveries to cutting-edge research, our researchers are empowering the next generation of female science, technology, engineering and mathematics (STEM) leaders.
Get inspired by our #WomeninSTEM