Smarter, More Accurate Machines: How A*STAR Helped Abrasive Engineering 'get-up' To Speed
Automated machines with greater precision, real-time data collection, and a dashboard that presents insights at a glance. Demands like these had been getting louder and more frequent from customers of machine design and fabrication company Abrasive Engineering (AE) in the last decade.
With the dawn of Industry 4.0, the Singapore small and medium-sized enterprise (SME) knew it was innovate or die. But how?
The SME challenge
As an SME, you do not even know who you need to employ, what work needs to be done,
Mr Tan Ser Hean, Executive Chairman, Abrasive Engineering
The Abrasive Engineering Team with A*STAR ARTC scientists and their shot peening machine
AE designs, develops, and manufactures abrasive blasting and shot peening machines, which are vital for surface treatment and used in a variety of industries - from aerospace to electronics and even cosmetics. Abrasive blasting cleans or smoothens the surface in preparation for a coat of paint, powder or welding work, while shot peening increases the surface's resistance to cracks, fatigue and corrosion.
An early attempt before 2019 to improve the accuracy of its surface treatment equipment in-house took four years and over S$500,000. "After our first development, we thought, ‘How can we launch a product to the market faster?'" Mr Tan recalled.
AE faced challenges in streamlining product development, establishing credibility, and accessing funding for research and development (R&D).
So it turned to the Agency for Science, Technology and Research's (A*STAR) Growing Enterprises through Technology Upgrade (GET-Up) programme to plug these gaps.
Through the programme, it got access to A*STAR's research pool, cutting-edge R&D tools, state-of-the-art facilities, and crucial government funding.
A blueprint for growth: Leveraging A*STAR's Operational and Technology Roadmap (OTR) programme
First, it needed a strategy. AE knew it wanted to develop new technologies that would differentiate it from its competitors, and market its products globally.
Through the OTR scheme, A*STAR reviewed AE's current business operations and technology and assessed its capability to meet future challenges and capture new markets.
Over a five-day workshop, AE understood that customers wanted a seamless machine-to-dashboard transition and more precision, and that it had to automate and improve the connectivity of its machines.
The OTR also identified potential areas for collaboration between AE and A*STAR. These included partnerships with A*STAR's Advanced Remanufacturing and Technology Centre (ARTC), National Metrology Centre (NMC) and Institute of High Performance Computing (IHPC), and setting up a joint lab in 2020.
Recruiting Top Talents: Tapping the Technology for Enterprise Capability Upskilling (T-Up) scheme
The T-Up scheme allowed AE to access A*STAR's extensive pool of scientists to help accelerate its innovation process. With the help of seconded researchers, it implemented and integrated an Internet of Things (IoT) box into the machines along the manufacturing line to allow real-time monitoring and control of assets through cloud services.
This allowed AE to respond to market demands for interconnectivity and a machine-to-dashboard system. The IoT box also enabled predictive maintenance of the machines and improved productivity and performance.
Abrasive Engineering with their microwave valve, developed in collaboration with A*STAR
In 2019, it collaborated with A*STAR's National Metrology Centre (NMC) to create the Non-Ferrous microwave valve with microwave particle sensing technology, allowing the surface treatment process to be controlled down to a T.
A key part of the process was the development of a calibration machine that cut the deviation range of the valve's accuracy from 5 per cent to about 2 or 3 per cent, which ensured stringent resource use and surface homogeneity.
"With an even roughness and surface finishing, you will get an even coating," said Mr Tan, explaining the merits of the valve's improved accuracy. "Customers would not buy a smartphone if it's uneven or patchy."
With support from the GET-Up programme, AE grew its revenue by $3 million in four years, said Mr Tan, and expanded into other regions in Asia.
The collaborative environment, combined with access to state-of-the-art facilities and expert guidance, has been instrumental in driving our innovation forward,
Mr Tan Ser Hean
Eyes on the future
AE is now primed to compete with industry leaders as it works with A*STAR to pursue further growth and innovation.
Its next goal? An even smarter valve. AE is leveraging A*STAR's expertise to program an artificial intelligence (AI)-driven printed circuit board for the valve. This AI-driven smart valve will grow more accurate with usage, ensuring an increasingly intuitive machine with further precision.
That is not all. AE will also examine ways to reduce its carbon footprint in line with the global drive for sustainability.
"We need to talk about sustainability," he stressed. "We must think about how we can lower our consumption - for example, reducing power, reducing hardware."
A*STAR celebrates International Women's Day
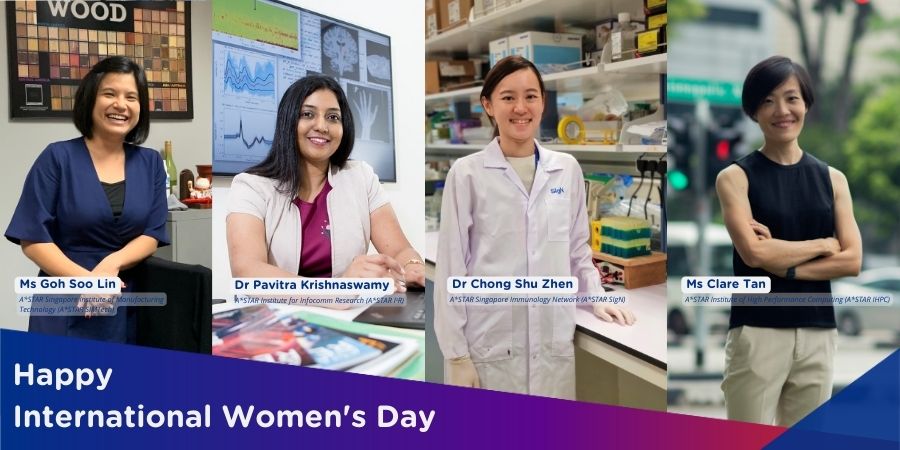
From groundbreaking discoveries to cutting-edge research, our researchers are empowering the next generation of female science, technology, engineering and mathematics (STEM) leaders.
Get inspired by our #WomeninSTEM