A*STAR NEWS
FEATURES
Thriving Through Sustainability: How Local Manufacturers Can Manage Their Carbon Footprint To Secure A Competitive Edge
By Dr Yeo Zhiquan, Acting R&D Division Director at A*STAR's Singapore Institute of Manufacturing Technology (SIMTech) and Advanced Remanufacturing and Technology Centre (ARTC)
This image was generated with the assistance of AI.
For manufacturers in Singapore, one of the pressing challenges they face is how to become more sustainable to stay competitive and relevant in the global market.
With the European Union and Singapore launching regulations that scrutinise firms’ Scope 3 emissions – which includes indirect emissions from sources not owned or controlled by firms, such as from companies that are part of their supply chains – more businesses will only work with sustainable suppliers in time to come.
Since manufacturing contributes about 22 per cent of Singapore’s gross domestic product and about 12 per cent of its jobs, the industry’s sustainability is essential to help us achieve our goal of net zero emissions by 2050.
While Singapore’s focus on growing and enhancing the value-add of its manufacturing sector may seem, at first glance, to be in conflict with its net zero emissions ambition, as an increase in manufacturing points to a likely rise in emissions too, sustainable manufacturing is the key that unlocks both goals.
With these pressures, manufacturers must embrace sustainability or risk being left behind. At the same time, there are strong benefits to achieving sustainability. Manufacturers can grow faster, and globally, by creating sustainable products that appeal to an increasingly sustainability-conscious client base, and enhance their brand in the process.
The manufacturing industry’s shift to sustainability has already started. According to a recent survey by the Singapore Manufacturing Federation and other organisations, 37 per cent of firms in the sector have introduced sustainability initiatives, and another 38 per cent plan to do so within one to three years. Those that do not follow suit will be in a shrinking minority.
As manufacturers think about their first or next steps in enhancing their sustainability, some may not know what to focus on, given the array of possibilities. Roadmapping tools such as the Green CompassTM developed by the Agency for Science, Technology and Research (A*STAR), JTC and TÜV SÜD can help.
Using data and insights to drive sustainability
The Green CompassTM tool involves a four-step process: learn about the latest sustainability trends and methodologies, assess the firm’s sustainability, prioritise areas with the most financial and strategic impact, and develop a roadmap for change. By going through this process, manufacturers can develop customised, effective plans that make sense for them.
For example, after completing the process, I-PEX Singapore, which manufactures electronic connectors and parts, recognised that it had to improve its supply network, as some suppliers were not able to meet its sustainability requirements. It has reviewed its environmental policy and suppliers’ code of conduct, and engaged with key suppliers on its sustainability targets.
After manufacturers use suitable roadmapping tools to understand where they are, and what they need to do next, adopting a rigorous approach that uses data to evaluate options, such as life cycle assessment (LCA) and life cycle costing (LCC), will help determine the best way forward.
An LCA spells out the environmental consequences of a product from cradle to grave. This includes not just the resources needed to extract, transport, process and assemble the raw materials, use the product, and finally dispose of or recycle it, but also the greenhouse gas emissions, pollution and other impacts associated with all of these activities.
Data from LCAs will allow companies to implement solutions that make the largest difference, whether it is switching to more environmentally-friendly materials, revamping processes, or even redesigning products to use less resources and make them easier to disassemble for recycling.
When A*STAR worked with a local manufacturer specialising in metal and ceramic injection moulding to conduct an LCA of seven of its products, the results showed that the electricity used to fabricate the items was the major source of its carbon emissions.
Consequently, the analysis found that minimising the energy needed to manufacture the products, for instance by installing energy-efficient technologies, or switching to renewable energy sources, would go far in supporting the manufacturer’s goal to become a greener partner in the supply chain, and to demonstrate corporate credibility to stakeholders and customers.
An LCC, on the other hand, uncovers a product’s financial costs over its lifetime. With such an analysis, a manufacturer may discover that a factory machine that costs less upfront will be a larger financial liability in the long run because it is energy-inefficient and will expose the firm to penalties under environmental regulations.
By combining LCAs and LCCs, manufacturers can identify the sustainability moves that will give them the biggest bang for their buck. Furthermore, such analyses underline how investments in sustainability are strategic commitments that deliver better operational efficiencies, long-term financial performance, and distinctive advantages over market competitors.
Becoming self-sufficient in sustainability planning
To equip manufacturers with the capability to conduct these analyses, A*STAR’s Singapore Institute of Manufacturing Technology (SIMTech) offers an LCA-LCC platform. This includes a 42-hour course that covers how to carry out an LCA to manage and optimise their products’ carbon footprint.
By learning how to conduct LCAs and LCCs, manufacturers gain the skills to evaluate their products and operations periodically. This allows them to respond to new business priorities, technological advancements, new shifts in industry, and other changes, to ensure that sustainability remains a core of their business strategy.
The LCA-LCC platform, which is an online tool, contains Singapore-based emissions data for electricity and other resource usage and activities, to empower local firms to develop accurate assessments of their environmental impact, for sustainability planning and to benchmark themselves against others. Singapore-based companies can also use data from a new Singapore Emission Factors Registry which was recently launched by Minister for Sustainability and the Environment Grace Fu in April, to track and report their carbon emissions.
Why is localised data important? Take electricity usage. Singapore generates almost all of its electricity from natural gas, which produces lower emissions than getting power from coal but more emissions than using renewable energy. Having local electricity emissions data is thus vital, as relying on overseas data where power comes from coal or solar energy would lead to flawed carbon footprint calculations.
With a comprehensive, granular and accurate picture of their impact on the environment, manufacturers will be in a better position to pinpoint areas for improvement, set goals and come up with actionable strategies to accomplish the targets, meeting the rapidly growing demand for climate-related transparency and sustainability worldwide.
Doing better for the environment is not just a moral imperative. It also delivers strategic business advantages that can strengthen manufacturers’ competitiveness and resilience, enabling them to stand out and extend their longevity.
By adopting a data-driven and deliberative approach to optimising products and processes, manufacturers can achieve both economic viability and environmental responsibility, support Singapore’s goal of achieving net-zero emissions, and position themselves at the forefront of industry innovation and longevity.
Was the article helpful?
A*STAR celebrates International Women's Day
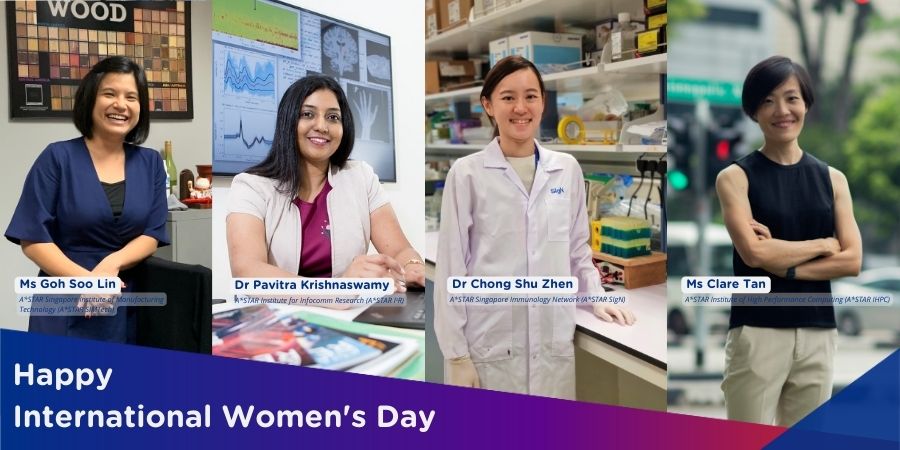
From groundbreaking discoveries to cutting-edge research, our researchers are empowering the next generation of female science, technology, engineering and mathematics (STEM) leaders.
Get inspired by our #WomeninSTEM