Workstreams
The workstreams within PIPS 2 include Active Ingredients to Product Interface, Agile Factory of the Future, Manufacturing Technology Platforms, Plant Operations, and Tools for Accelerated Process Development and Process Technology. There are 2 sub-workstreams namely, Nitrosamines and Sustainable Waste Management in the Active Ingredient to Product Interface and Agile Factory of the Future, respectively. The horizontal themes namely Sustainability, Digitalisation and Automation and Experimental Design and Modelling are integrated throughout the entire PIPS programme.
Sub-Workstreams
A*STAR celebrates International Women's Day
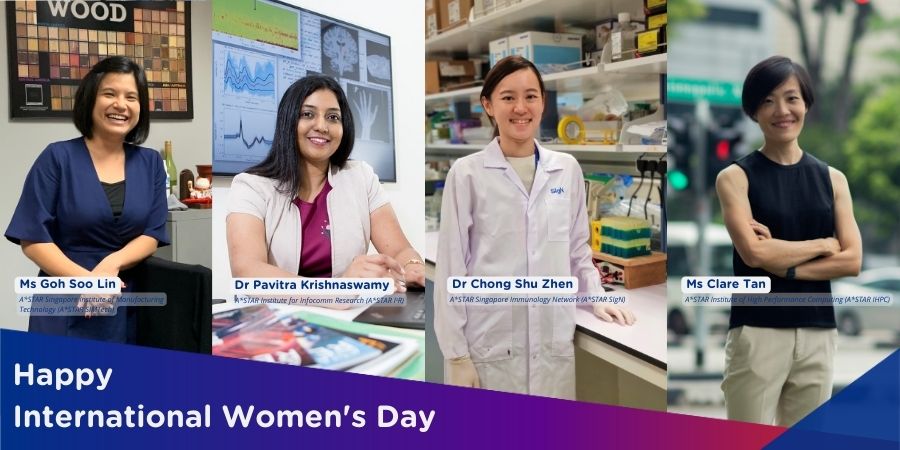
From groundbreaking discoveries to cutting-edge research, our researchers are empowering the next generation of female science, technology, engineering and mathematics (STEM) leaders.
Get inspired by our #WomeninSTEM