DIMENSIONAL MEASUREMENT OF INTERNAL FEATURES OF ADDITIVE MANUFACTURING PARTS
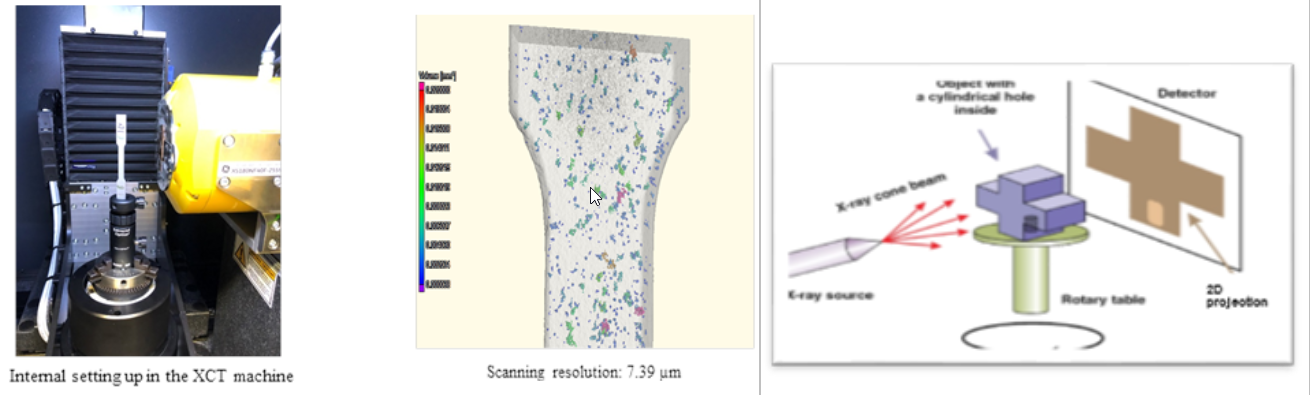
Additive manufacturing technology has innate advantages on manufacturing products of high complexity and customization. Those complex interior structures and intricate lattice features of an Additive Manufacturing (AM) part are inaccessible and impossible to be disclosed without destruction by the available contact and optical measurement technologies and systems. Non-destructive measurement methods are demanded for quality check and assurance of AM parts.
X-ray Computed Tomography (XCT) utilizes X-ray cone beam to scan an AM part for a good number of times at different angles, and 3D reconstruction of the part can be realized to disclose the 3D intricate volume non-destructively. It brings incredible advantages that were previously impossible with traditional inspection methods. Internal and external features can be detected simultaneously. The complex lattice structures can be intensively sampled and reconstructed quantitatively, and detecting defects and porosity and identifying the distribution also become possible. XCT is considered as the most promising non-destructive metrology tool to quantitatively uncover the internal 3D features, and is being more and more adopted for characterization of internal features of AM parts and materials.
Compared to traditional linear and 2D metrology tools, 3D measurements with XCT technology face some technical challenges in traceability and uncertainty for 3D measurements of different geometry with different materials. These issues come from the polychromatic beam nature of X-Ray and the mixed physical effects including photoelectric and scattering effect while X-ray penetrating sample material, and thus render open rooms for further development. How to make full use of XCT to traceably and accurately measure internal structures and features of AM parts, such as internal dimensions and surfaces, porosity and etc., is one of our main research areas.
A*STAR celebrates International Women's Day
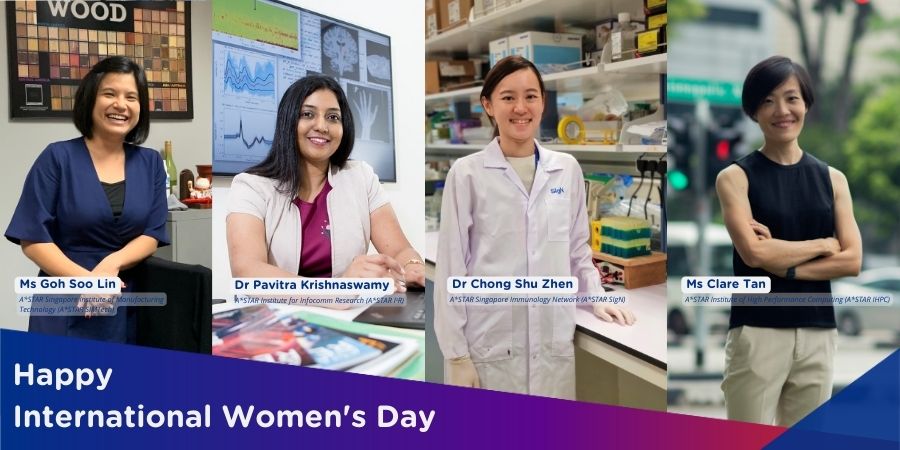
From groundbreaking discoveries to cutting-edge research, our researchers are empowering the next generation of female science, technology, engineering and mathematics (STEM) leaders.
Get inspired by our #WomeninSTEM