IHPC Tech Hub
IHPC Tech Hub showcases IHPC's suite of in-house developed applications, tools or technology to help you unlock the possibilities to overcome business challenges. Through providing valuable insights, you can now predict and shape the commercial outcomes, automate processes, and free up resources for repetitive and labour-intensive tasks.
Discover the power of computational modelling, simulation and AI that brings about positive impact to your business.
Discover the power of computational modelling, simulation and AI that brings about positive impact to your business.
- Health & Human Potential
- Manufacturing & Engineering
- Smart Nation & Digital Economy
- Transport & Connectivity
- Urban Solutions & Sustainability
Informatics for Catalysis Design
12 Oct 2023
Difficulties of Traditional Methods
While computations could be very useful for gaining insights into catalytic mechanisms, they might be difficult to perform and scale up due to various factors:
- High Entry Barrier: Immense training is needed for new researchers to acquire knowledge of different codes and platforms developed by various groups such as bash, ASE, VASP, pymatgen, CatKit, Avogadro, Materials Studio - to perform these calculations.
- Tedious and Time-Consuming: Numerous computations are often required to understand a single reaction. This consumes significant time and requires manual preparation, which is prone to human errors.
- Increasing Complexity: The number of required computations increases exponentially for more complex catalysts, such as alloys.
To tackle these difficulties, two complementary technologies have been developed to accelerate the development of novel catalysts:
- Catalysis Platform (CatPlat): Automate various workflows in computational heterogeneous catalysis by increasing the throughput and reliability of calculations and decreasing the barriers to entry for researchers in the field of computational heterogeneous catalysis. Additionally, the results of the computations are stored in databases to prevent duplicate computations and allow the sharing of data with collaborators and colleagues.
- Machine Learning Powered Reaction Optimiser (MPRO): Train a vast amount of literature knowledge to optimise the catalyst composition and reaction conditions for a particular reaction. Crucially, MPRO assesses the system's characteristics, allowing for the identification of the most critical system attributes and enabling a guided approach to enhance reaction conversion.
Features
CatPlat is designed to address the pain points of traditional catalysis workflows via the following desirable features:
- Low Entry Barrier: An intuitive interface designed for researchers, eliminating the need to learn multiple codes.
- Efficient: Automated workflows greatly save time for the setting up and analysis of computations. Additionally, CatPlat stores data for reuse and reduces duplicate calculations. The computational jobs performed by CatPlat can be parallelised through an internal queuing system, making jobs highly scalable.
- Improved Algorithms: Robust slab building and adsorbate placement algorithms refined by testing over a wide variety of catalyst surfaces, from metals to oxides. It is also able to handle both monodentate and bidentate adsorbates.
MPRO
- Physics-based catalyst fingerprints: Focuses on experimental data and incorporates the rich physics and chemistry-based features of catalysts obtainable by computations, such as adsorbate binding energies and surface properties.
- Web-interface: MPRO includes a user-friendly and intuitive web interface for visualisation and understanding of the obtained results.
The Science Behind
CatPlat seamlessly links the various codes required for catalysis computations, and automatically constructs and executes workflows for calculating key catalytic descriptors such as binding energies, Bader charges, and d-band centers
(Fig 1). These valuable descriptors could be analysed to understand the electronic and energetic properties of the chosen catalytic materials in more detail.
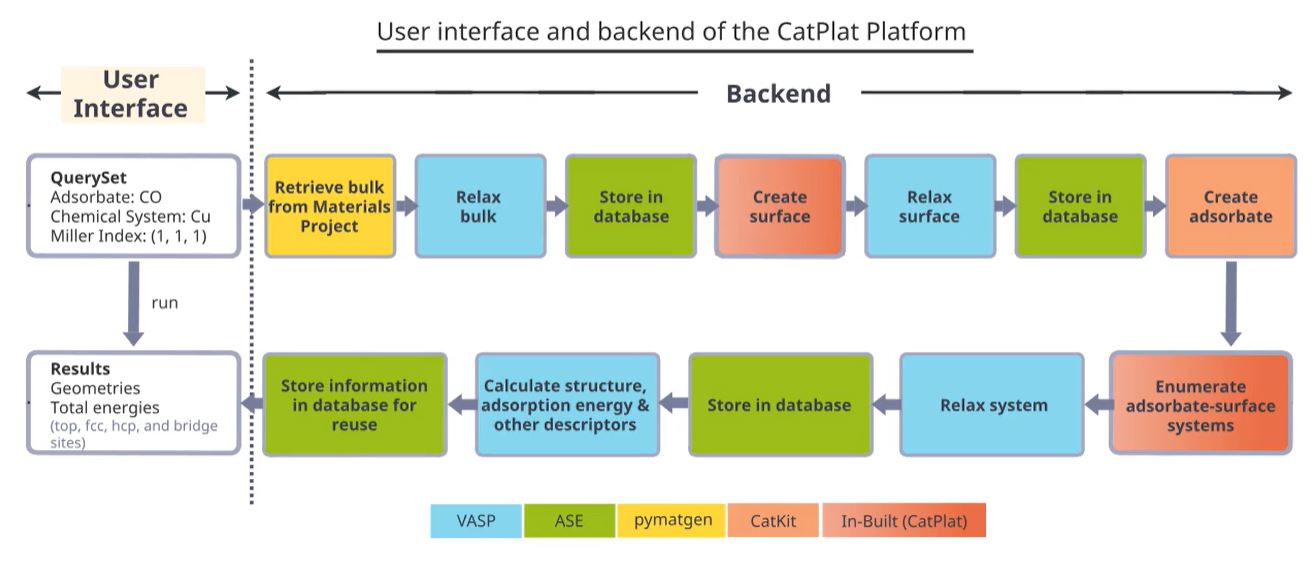
Fig 1. User interface and backend of the CatPlat platform. An example of CO binding on Cu(111) is shown. The query specified by the user, is automatically converted into a series of backend tasks, color-coded by the various programs and python packages used. The tasks are then executed to return the results to the user. The backend process is transparent to the user, making the user interface simple and intuitive.
The user will therefore only need to specify their query in simple terms, for example, which adsorbates and catalyst surfaces they want probed. Invisible to the user, the backend then performs multiple steps that take care of input preparation and output
processing. In the end, the results are returned to the user without the user needing to have any knowledge of the codes used.
MPRO uses state-of-the-art XGBoost and neural network architectures to train accurate models for predicting reaction conversions based on a given catalyst and reaction conditions (Fig 2). A theory-guided loss function is imposed to ensure
that the predictions are physically bound and obey thermodynamic principles.
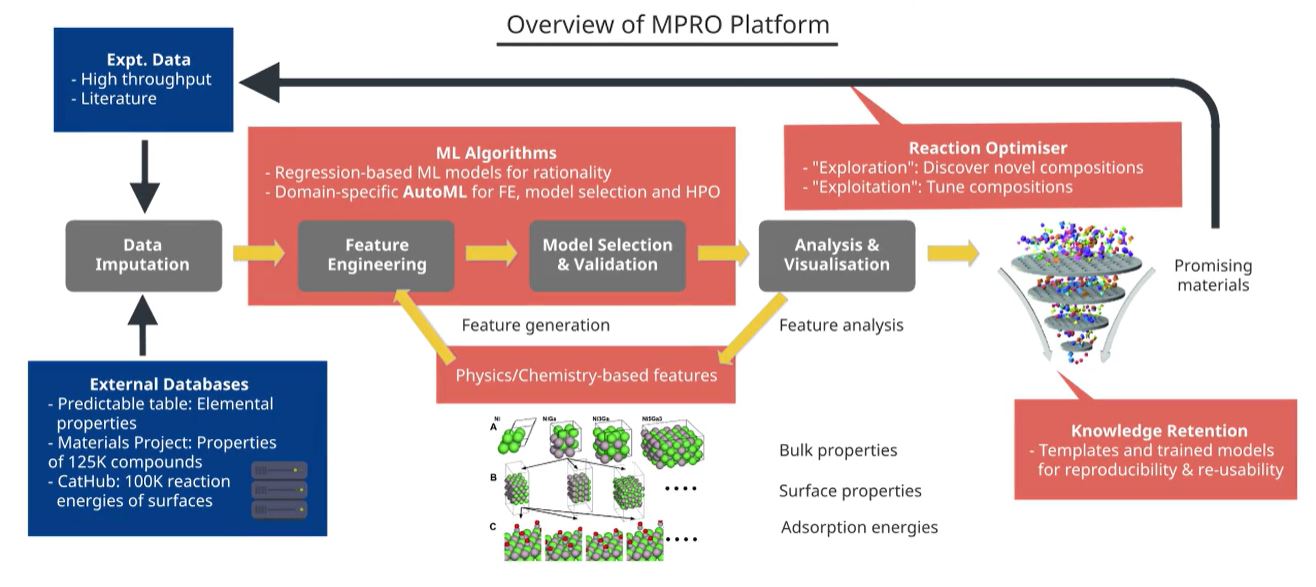
Fig 2. Overview of the MPRO platform. External databases and in-house experimental data can be used as inputs for MPRO, in addition to physics and chemistry-based catalyst features. The data are then machine learned to predict reaction conversion, which also enables solution of the inverse problem of reaction condition and catalyst optimisation.
Inspired by microkinetic theory and physiochemical properties of metals and promoters, MPRO also incorporates fingerprint features based on the physical, chemical, and surface chemistry properties of the catalyst. This provides an extra boost to the accuracy
of our models compared to those of competitors.
The combination of MPRO and CatPlat streamlines the catalyst design whereby MPRO identifies essential catalyst features, while CatPlat conducts rapid screening of diverse catalyst surfaces. The resulting data is integrated into MPRO for quick predictions
of catalytic performance. This iterative process significantly expedites the discovery of new catalysts for various reactions.
Industry Applications
A deeper understanding of how catalysts work holds the key to improving the efficiency of many industrial processes. CatPlat and MPRO shine for complicated reactions involving numerous catalytic intermediates and complex catalyst surfaces, such as:
- Fischer-Tropsch Synthesis (FTS)
- Water Gas Shift (WGS) reaction
- Reactions pertaining to sustainability, such as CO¬2 hydrogenation to higher alcohols
Many of these reactions are intractable to study with traditional computational methods. However, with CatPlat, a fundamental understanding of the atomistic interactions between the reaction intermediates and the catalyst surface could be obtained in a timely manner. MPRO would also potentially help to optimise reaction conditions in a rapid manner and identify new catalysts by elucidating the key physics and chemistry-based descriptors that influence the conversion of the reaction.
A*STAR celebrates International Women's Day
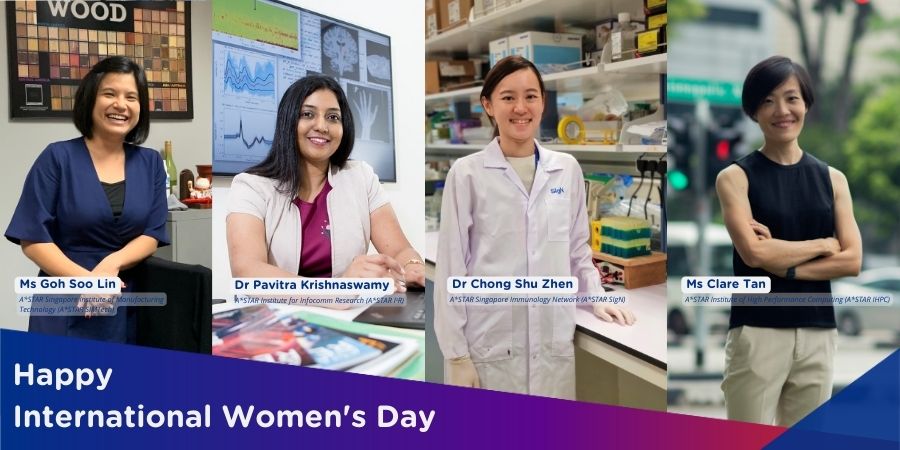
From groundbreaking discoveries to cutting-edge research, our researchers are empowering the next generation of female science, technology, engineering and mathematics (STEM) leaders.
Get inspired by our #WomeninSTEM