Digital Manufacturing Processes & Design
Background / Motivation
Digital Manufacturing refers to the extensive application of inter-connected computer-controlled systems throughout the manufacturing process. It is the ultimate result of the “Digitalisation” of the manufacturing process, where design and manufacturing are integrated by digital tools. Highly automated, computer-controlled machines are used, such as CNC Machining centres or Additive Manufacturing “3D Printers”, which connect to the digital design and manufacturing scheduling systems.
Capabilities
Digital Manufacturing refers to the extensive application of inter-connected computer-controlled systems throughout the manufacturing process. It is the ultimate result of the “Digitalisation” of the manufacturing process, where design and manufacturing are integrated by digital tools. Highly automated, computer-controlled machines are used, such as CNC Machining centres or Additive Manufacturing “3D Printers”, which connect to the digital design and manufacturing scheduling systems.
IHPC’s digital manufacturing process and design efforts include:
- Manufacturing Process Simulation, is a branch of Computer-Aided Engineering applied to the numerical simulation of a wide variety of manufacturing processes. IHPC has modelled processes ranging from bulk material forming, moulding, fluid flow and mixing, to product assembly and filling of liquid products. When used at the design stage, such simulations function as virtual testing, allowing manufacturers to optimise the product design as well as look for improvements in the manufacturing process.
- Identify the cause of manufacturing issues as and when they occur. Coupled with Digital Twins, which are unique digital replicas of highly sensorised physical systems, these simulations can be used in a predictive manner, to identify issues early.
- Develop Artificial Intelligence systems that use data from sensors to provide predictive capabilities. For infrequent events, where there is a lack of data, these can be enhanced with more detailed physics-based models, including manufacturing process simulations, that can determine the outcome from an event, e.g., damage caused by an overload.
Working with other A*STAR’s Research Institutes (RIs) such as the Singapore Institute of Manufacturing Technology (SIMTech) and Advanced Remanufacturing and Technology Centre (ARTC), IHPC seeks to develop complete Digital Manufacturing solutions that provides competitive advantage and enable new production technology to end users.
Collaboration Opportunities
There is rapid development in the field of Digital Manufacturing with many organisations striving to implement Industry 4.0. IHPC offers broad technical expertise in computational applications and supports companies looking to improve their manufacturing and operational processes. IHPC collaborates with industrial partners to develop advanced simulation, modelling and AI applications as a key enabler in their digitalisation strategy. Opportunities include the development of Manufacturing Process Simulations and integration with Digital Twins that allow manufacturing systems to develop predictive capabilities.
IHPC is also interested to collaborate in developments of AI, where there are emerging techniques to perform automatic defect detection, or predictive maintenance using sensors coupled to AI and machine learning techniques. We are also working with partners on use of AI to make machines smarter, so that they can learn from and with human operators and work better together.
For more info or collaboration opportunities, please write to enquiry@ihpc.a-star.edu.sg.
There is rapid development in the field of Digital Manufacturing with many organisations striving to implement Industry 4.0. IHPC offers broad technical expertise in computational applications and supports companies looking to improve their manufacturing and operational processes. IHPC collaborates with industrial partners to develop advanced simulation, modelling and AI applications as a key enabler in their digitalisation strategy. Opportunities include the development of Manufacturing Process Simulations and integration with Digital Twins that allow manufacturing systems to develop predictive capabilities.
IHPC is also interested to collaborate in developments of AI, where there are emerging techniques to perform automatic defect detection, or predictive maintenance using sensors coupled to AI and machine learning techniques. We are also working with partners on use of AI to make machines smarter, so that they can learn from and with human operators and work better together.
For more info or collaboration opportunities, please write to enquiry@ihpc.a-star.edu.sg.
A*STAR celebrates International Women's Day
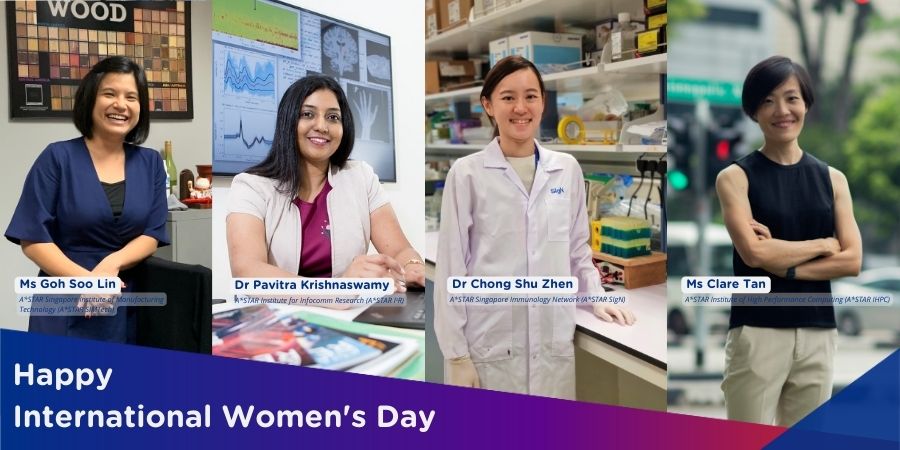
From groundbreaking discoveries to cutting-edge research, our researchers are empowering the next generation of female science, technology, engineering and mathematics (STEM) leaders.
Get inspired by our #WomeninSTEM