IHPC Tech Hub
IHPC Tech Hub showcases IHPC's suite of in-house developed applications, tools or technology to help you unlock the possibilities to overcome business challenges. Through providing valuable insights, you can now predict and shape the commercial outcomes, automate processes, and free up resources for repetitive and labour-intensive tasks.
Discover the power of computational modelling, simulation and AI that brings about positive impact to your business.
Discover the power of computational modelling, simulation and AI that brings about positive impact to your business.
- Health & Human Potential
- Manufacturing & Engineering
- Smart Nation & Digital Economy
- Transport & Connectivity
- Urban Solutions & Sustainability
Precision Insight: Leveraging Advanced Analytics for Enhanced Rubber Profile Measurement
12 Oct 2023
The current measurement system employed in the Hutchinson manufacturing line utilises a laser sensor system to capture the profile of the section's point cloud. It then compares this profile with a pre-defined template and key point pairs to ascertain the conformity of the rubber profile to the template. However, due to the non-rigid nature of the rubber shape before vulcanisation, deformations and rotations in the section are common. This leads to inaccuracies in the existing system's ability to precisely match the profile and measure distances. Consequently, this undermines the reliability of the quality monitoring process.
In response to this need for precision, A*STAR’s Institute of High Performance Computing (IHPC) has engineered Precision Insight - an analytics-driven measurement tool that harnessed laser sensor data as its input. This tool incorporates a suite of advanced algorithms, resulting in an Artificial Intelligence (AI) solution tailored for Hutchinson's rubber extrusion lines, specifically designed to predict rubber shape accuracy. The results have been highly encouraging, showcasing the tool's ability to meet the ever-growing technical demands of these specifications. Furthermore, the integration of AI technology has empowered the tool to be scalable, promising significant time and cost savings.
Features
- Identify the need for laser sensor maintenance
- Detect the profile off-center drift for rotational and translational compensation
- Recognise key points and measure the distance between them
- Assess the conformity of an extruded profile with a known pre-defined template
The Science Behind
The tool was developed using a knowledge-embedded approach, which involved analysing data from the extruded profiles using data-driven techniques coupled with mathematical formulations and physics-based knowledge from domain experts,
as illustrated in Fig 1.
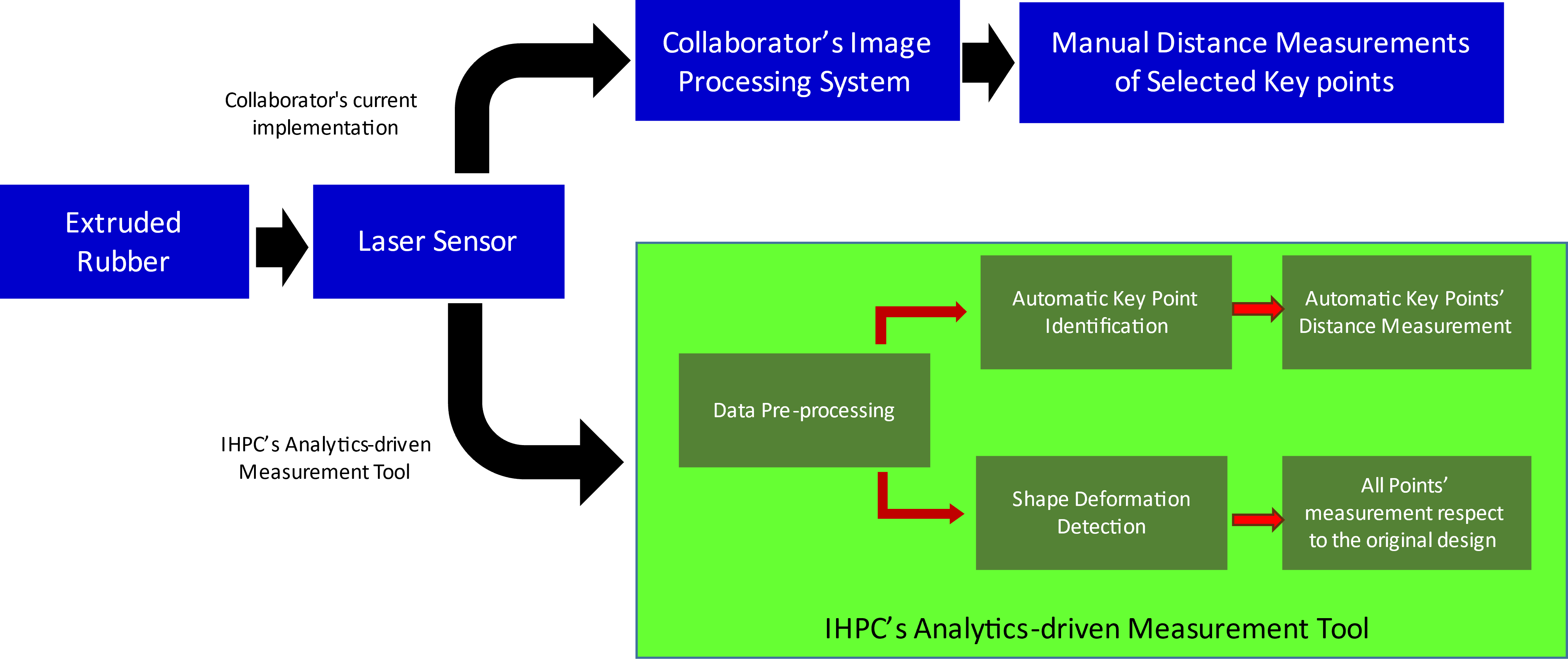
Fig 1. Measurement tool that works seamlessly with collaborator’s current image processing system
Sustainability Outcomes
This AI innovation could significantly contribute to sustainability in several ways:
- By employing AI to predict the accuracy of the rubber shapes, Hutchinson could significantly minimise waste in their production process. Currently, a substantial number of raw materials were discarded due to inaccurate measurements of the vulcanised
rubber material falling outside acceptable ranges. Introducing a laser scanner at the outset of the production line, coupled with AI predicting shape accuracy, allowed Hutchinson to reduce waste by halting the production line or adjusting parameters
before any waste was generated. This could potentially help to trim raw material usage, cut energy consumption, and mitigate the carbon footprint associated with the production of these materials.
- This project could enhance Hutchinson's quality control protocols, resulting in a reduction in customer-rejected products. Through the integration of a laser scanner and AI, Hutchinson could ensure that their rubber components align with the desired shape and design specifications. This not only fosters heightened customer satisfaction but also diminishes product returns and replacements, hence reducing waste and conserving valuable resources.
In addition, this project holds the potential to contribute significantly to the broader sustainability of the manufacturing industry. By showcasing the efficacy of incorporating advanced technologies and practices, Hutchinson sets a precedent for other companies. Their commitment to waste reduction and improved quality control becomes a blueprint for sustainable production, fostering eco-friendly practices and minimising environmental impact in the long term.
This article is published with the permission from Hutchinson.
A*STAR celebrates International Women's Day
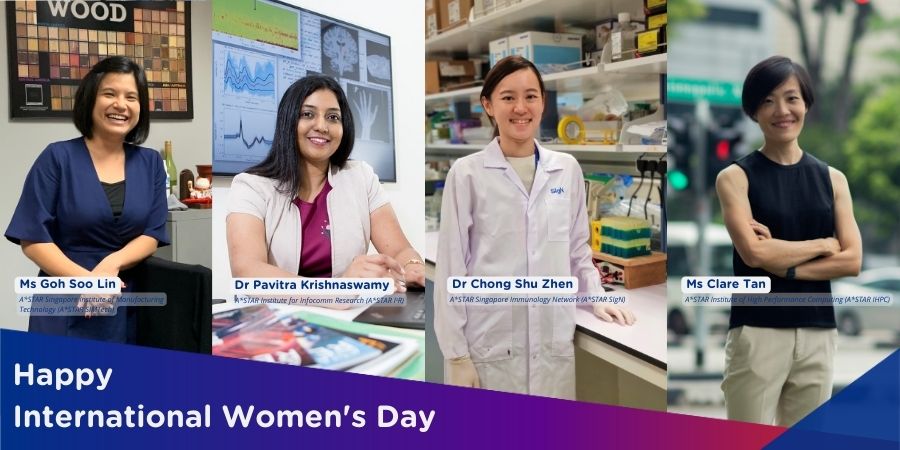
From groundbreaking discoveries to cutting-edge research, our researchers are empowering the next generation of female science, technology, engineering and mathematics (STEM) leaders.
Get inspired by our #WomeninSTEM