Manufacturing & Engineering
- Health & Human Potential
- Manufacturing & Engineering
- Smart Nation & Digital Economy
- Transport & Connectivity
- Urban Solutions & Sustainability
Cyber-Physical Platform for Industry 4.0
Manual work and inspection in the manufacturing process are unproductive as it is labour-intensive, time-consuming, and costly. For example, in a shot peening operation, the development of the Almen strip approach for guiding actual operation often takes about 2-4 months to establish process parameters for a targeted intensity in a fundamental component. Overall, the Almen strip approach takes up 20 to 25% of production efforts, and the testing process is a common bottleneck for various surface treatments which often prevents automatic production.
The developed Model-based control platform, namely ‘Cyber-Physical Platform for Automated Shot Peening Machine’ can automatically and directly apply to actual peening operation for any targeted intensity without the need of Almen strip approach development. As a result, upgrading the automated control system can significantly reduce the cost, time, and labor and material wastes. This platform can also apply to other industrial applications, not limiting to the shot peening process.
Features
- Directly apply to industrial peening production without prior Almen strip approach development
- Automatically manipulate input (inlet air pressure) to accurately attain output (any targeted intensity)
- Stable, robust and accurate model-based controller
- Better quality of final product
- Greatly improved efficiency and productivity
- Significantly reduced cost, time, labor, and material wastage
The Science Behind
As a result, a single input / single output feedback MPC with future process pre-view capability is developed and integrated into the actual shot peening machine. The MPC has been demonstrated and validated using both in-silico and onsite controls for different scenarios. The obtained results showed that the developed MPC is stable, robust and accurate as it can automatically adjust inlet air pressure to attain any intensity setting accurately.
Industry Applications
- Shot peening industry for surface enhancement
- Sand blasting industry for surface preparation
- Painting industry
- Chemical engineering processes
- Pharmaceutical industry
- Data centre
- 3D printing
For more info or collaboration opportunities, please write to enquiry@ihpc.a-star.edu.sg.
A*STAR celebrates International Women's Day
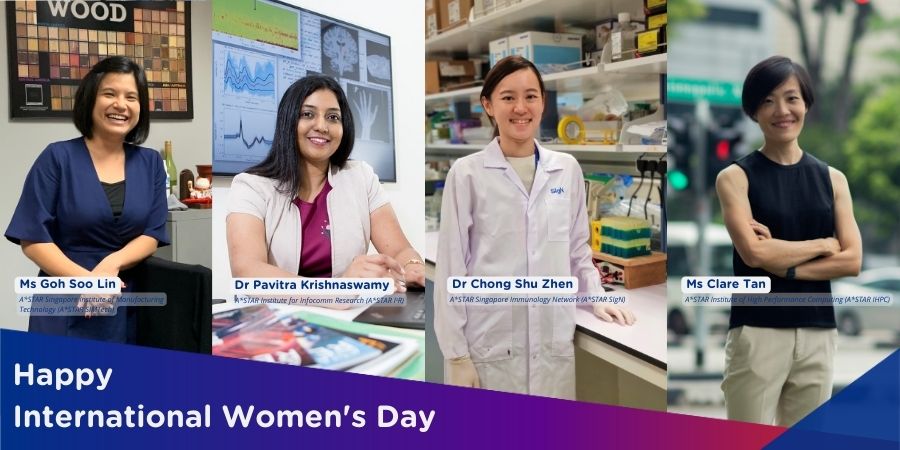
From groundbreaking discoveries to cutting-edge research, our researchers are empowering the next generation of female science, technology, engineering and mathematics (STEM) leaders.
Get inspired by our #WomeninSTEM