Applying Technologies to Empower “Traditional” Business: Doors
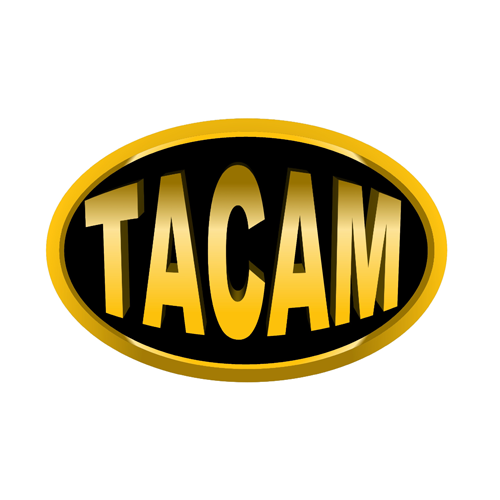
Collaborator
Established since the early 1960s, Tacam Steel Pte Ltd (TACAM) sets out to satisfy the needs of Singapore’s public housing and rapid industrialisation programs, with its steel and aluminium window louvres recognised globally with a U.K. patent and SISIR Quality Mark. TACAM’s strength lies in meeting complex requirements ranging from fire-compartmentalisation and radiation shielding to acoustic dampening and blast resistance. Today, TACAM is the leading steel door manufacturer in the region, with its doors installed in residential, commercial and industrial projects in Singapore, Malaysia, Asia and the UK.
Established since the early 1960s, Tacam Steel Pte Ltd (TACAM) sets out to satisfy the needs of Singapore’s public housing and rapid industrialisation programs, with its steel and aluminium window louvres recognised globally with a U.K. patent and SISIR Quality Mark. TACAM’s strength lies in meeting complex requirements ranging from fire-compartmentalisation and radiation shielding to acoustic dampening and blast resistance. Today, TACAM is the leading steel door manufacturer in the region, with its doors installed in residential, commercial and industrial projects in Singapore, Malaysia, Asia and the UK.
Challenges
Before the 1960s, fire safety standards in Singapore’s buildings were less stringent than the present day. Most doors found in residential and commercial buildings were typically non fire-resistant and therefore unable to withstand the extreme temperatures of a fire which could go as high as 1200 degrees Celsius. Few companies were willing to invest in the high costs and long hours needed to perform physical fire resistance tests. Furthermore, with the limited number of prototypes available, the test results were statistically under-evaluated. The prototypes were also unable to be extrapolated for other test scenarios such as higher temperatures or longer durations.
In 1974, the Singapore Civil Defence Force (SCDF) published the first version of the Fire Code [1] to provide an official rulebook for fire safety standards to keep pace with Singapore's evolving urban landscape and national development. The Fire Code mandates that fire-rated doors be able to compartmentalise a fire within a room and prevent it from spreading for a fixed period, allowing time for people to escape and for SCDF personnel to arrive on-site to extinguish the fire. Such doors can be rated from 30 minutes to as long as 4-hours.
TACAM's fire-rated doors are certified and compliant with SCDF’s Fire Code standards to last the full 4-hours in the event of a fire. However, when used in HDB flats with lower fire-rating requirements, some of these doors were considered over-specifications. It resulted in the company to absorb higher material and production costs, and thus a lower profit margin.
TACAM was keen to explore ways to reduce its material and production cost for the doors while meeting the regulator’s requirements. Through the Technology for Enterprise Capability Upgrading (T-UP) programme, IHPC worked with TACAM to enhance its capabilities in the design of fire-resistance doors using numerical tools that evaluate the performance of doors design and materials. The simulation insights would then serve as crucial inputs and design guidelines for future products.
Solution
Coupled with TACAM’s domain knowledge of physical fire tests and design regulations, IHPC was able to simulate and mimic the fire test in a digital environment and use the simulated results to validate and benchmark against TACAM’s designs database. These results consisted of the temperature profile and the corresponding structural deformation of the doors as they were “burned”.
The virtualised results enabled TACAM and IHPC to gain insights into the heat paths/loads and the structural performance at any instance of the digital fire-test. With the validated simulation model and virtually assessed "what-if" scenarios, TACAM would be able to make sound and cost-effective business decisions by applying the simulation approach to the new door designs.
Before the 1960s, fire safety standards in Singapore’s buildings were less stringent than the present day. Most doors found in residential and commercial buildings were typically non fire-resistant and therefore unable to withstand the extreme temperatures of a fire which could go as high as 1200 degrees Celsius. Few companies were willing to invest in the high costs and long hours needed to perform physical fire resistance tests. Furthermore, with the limited number of prototypes available, the test results were statistically under-evaluated. The prototypes were also unable to be extrapolated for other test scenarios such as higher temperatures or longer durations.
In 1974, the Singapore Civil Defence Force (SCDF) published the first version of the Fire Code [1] to provide an official rulebook for fire safety standards to keep pace with Singapore's evolving urban landscape and national development. The Fire Code mandates that fire-rated doors be able to compartmentalise a fire within a room and prevent it from spreading for a fixed period, allowing time for people to escape and for SCDF personnel to arrive on-site to extinguish the fire. Such doors can be rated from 30 minutes to as long as 4-hours.
TACAM's fire-rated doors are certified and compliant with SCDF’s Fire Code standards to last the full 4-hours in the event of a fire. However, when used in HDB flats with lower fire-rating requirements, some of these doors were considered over-specifications. It resulted in the company to absorb higher material and production costs, and thus a lower profit margin.
TACAM was keen to explore ways to reduce its material and production cost for the doors while meeting the regulator’s requirements. Through the Technology for Enterprise Capability Upgrading (T-UP) programme, IHPC worked with TACAM to enhance its capabilities in the design of fire-resistance doors using numerical tools that evaluate the performance of doors design and materials. The simulation insights would then serve as crucial inputs and design guidelines for future products.
Solution
Coupled with TACAM’s domain knowledge of physical fire tests and design regulations, IHPC was able to simulate and mimic the fire test in a digital environment and use the simulated results to validate and benchmark against TACAM’s designs database. These results consisted of the temperature profile and the corresponding structural deformation of the doors as they were “burned”.
The virtualised results enabled TACAM and IHPC to gain insights into the heat paths/loads and the structural performance at any instance of the digital fire-test. With the validated simulation model and virtually assessed "what-if" scenarios, TACAM would be able to make sound and cost-effective business decisions by applying the simulation approach to the new door designs.
Key Results
The new advanced approach in designing doors enables TACAM to achieve a 30% reduction in design lead time and a 15% decrease in manufacturing cost. Being able to carry out digital testing on product design has also reduced the number of physical prototypes required with a potential cost saving of $15,000 per design. TACAM is now able to design and build fire-resistant doors in a myriad of sizes and configurations that meet customer’s specifications in a faster and cost-effective manner, in this competitive market.
The new advanced approach in designing doors enables TACAM to achieve a 30% reduction in design lead time and a 15% decrease in manufacturing cost. Being able to carry out digital testing on product design has also reduced the number of physical prototypes required with a potential cost saving of $15,000 per design. TACAM is now able to design and build fire-resistant doors in a myriad of sizes and configurations that meet customer’s specifications in a faster and cost-effective manner, in this competitive market.
"Having witnessed the evolution of the construction and manufacturing industries in Singapore and the region since the 1960s, TACAM is a firm believer and testament of the need to constantly innovate in order to stay ahead of the competition. Disruption has now become the norm, making it even more critical to invest in R&D. Through our collaboration with IHPC, we have managed to accelerate this process through robust simulations of our fire resistance tests, which traditionally take many months and considerable funding to complete. These simulations allow us to iterate many design variations and observe the outcomes before even fabricating a single door.", said Mr Brian Wong, Director, TACAM.
Significant Progress
Numerical simulations can provide insights to the performance of various designs in a virtual environment, thereby lowering costly investment on product development through potential reductions in the design cycle, material wastage and the number of experimentations required. Moreover, numerical simulations can aid in evaluating the performance of fire doors under “what-if” scenarios and conditions, such as higher temperatures.
IHPC’s capabilities in modelling and simulations enable us to tackle real-world challenges in physical and human systems in the areas of manufacturing, energy, transportation and urban systems, environmental sustainability, healthcare and more.
A*STAR celebrates International Women's Day
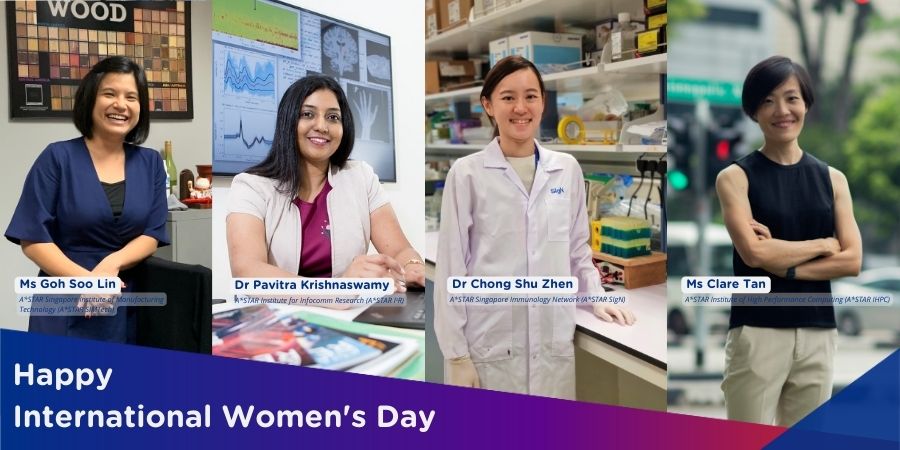
From groundbreaking discoveries to cutting-edge research, our researchers are empowering the next generation of female science, technology, engineering and mathematics (STEM) leaders.
Get inspired by our #WomeninSTEM