Multi-Fidelity Modelling for Design Enhancement: Inkjet Printers
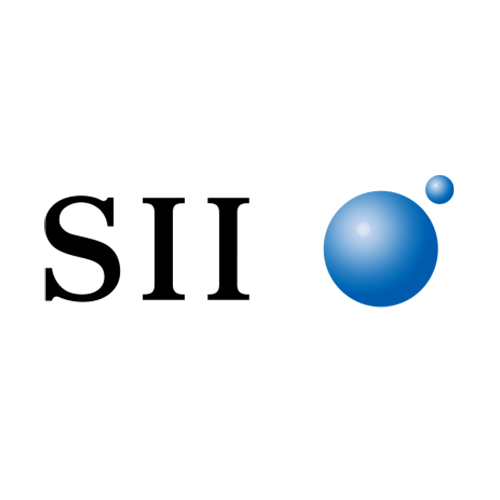
Collaborator
Founded in 1937, Seiko Instruments Inc.[1] (SII) manufactures and sells electronic components, precision parts, analysis and measurement instruments, machine tools, factory automation systems and printers. As a subsidiary of Seiko Holdings Corporation[2], the company now has over 12,000 employees worldwide, engaging in various business domains such as watches, electronic devices, systems solutions, clocks, high end apparel, fashion accessories and system clocks.
Founded in 1937, Seiko Instruments Inc.[1] (SII) manufactures and sells electronic components, precision parts, analysis and measurement instruments, machine tools, factory automation systems and printers. As a subsidiary of Seiko Holdings Corporation[2], the company now has over 12,000 employees worldwide, engaging in various business domains such as watches, electronic devices, systems solutions, clocks, high end apparel, fashion accessories and system clocks.
Challenges
At the heart of any inkjet printer, the ink droplet ejection process controls the speed and quality of printing. Back then, there was no robust solution to simulate the ink droplet ejection process. Simulating such a process would involve complex physics in fluid dynamics, solid mechanics, piezoelectricity. And coupling these individual solvers into one integrated suite of solvers was also a challenge due to the high demand of computational resources.
Subsequently, SII approached IHPC to study a large-scale simulation of a full inkjet head with multiple ink ejection sites involving aerodynamic effects between the print head and fast-moving print media. The air currents generated by the moving print media and a constant stream of droplets would significantly impact the ink droplet trajectory and affect print quality.
At the heart of any inkjet printer, the ink droplet ejection process controls the speed and quality of printing. Back then, there was no robust solution to simulate the ink droplet ejection process. Simulating such a process would involve complex physics in fluid dynamics, solid mechanics, piezoelectricity. And coupling these individual solvers into one integrated suite of solvers was also a challenge due to the high demand of computational resources.
Subsequently, SII approached IHPC to study a large-scale simulation of a full inkjet head with multiple ink ejection sites involving aerodynamic effects between the print head and fast-moving print media. The air currents generated by the moving print media and a constant stream of droplets would significantly impact the ink droplet trajectory and affect print quality.
Solution
The design of inkjet heads to cater to specified technical demands for a broad user base is crucial to SII for market development and maintenance for its inkjet printers. At the initial project phase, IHPC has developed a multi-fidelity approach for inkjet heads optimisation. It combined different fidelity models of inkjet head mechanisms and processed from a high fidelity three-dimensional, electromechanical fluid-structure interaction model to a simplified lumped element model (LEM).
In the next phase, the team was tasked into building an integrated platform to incorporate all models to mitigate the multi-fidelity optimisation process of the inkjet head. It involved in-depth validation for the optimal inkjet head design with experimental prototyping and extend possible simulations on other technical specifications, such as user-specific demand on droplet generation[3].
The design of inkjet heads to cater to specified technical demands for a broad user base is crucial to SII for market development and maintenance for its inkjet printers. At the initial project phase, IHPC has developed a multi-fidelity approach for inkjet heads optimisation. It combined different fidelity models of inkjet head mechanisms and processed from a high fidelity three-dimensional, electromechanical fluid-structure interaction model to a simplified lumped element model (LEM).
In the next phase, the team was tasked into building an integrated platform to incorporate all models to mitigate the multi-fidelity optimisation process of the inkjet head. It involved in-depth validation for the optimal inkjet head design with experimental prototyping and extend possible simulations on other technical specifications, such as user-specific demand on droplet generation[3].
Variation of droplet volume and velocity with pulse width in comparison with experiment
measurement.
Solution
The design of inkjet heads to cater to specified technical demands for a broad user base is crucial to SII for market development and maintenance for its inkjet printers. At the initial project phase, IHPC has developed a multi-fidelity approach for inkjet heads optimisation. It combined different fidelity models of inkjet head mechanisms and processed from a high fidelity three-dimensional, electromechanical fluid-structure interaction model to a simplified lumped element model (LEM).
In the next phase, the team was tasked into building an integrated platform to incorporate all models to mitigate the multi-fidelity optimisation process of the inkjet head. It involved in-depth validation for the optimal inkjet head design with experimental prototyping and extend possible simulations on other technical specifications, such as user-specific demand on droplet generation[3].
IHPC developed various physical models and incorporated them progressively into the fully integrated suite of solvers and libraries while balancing the needs of immediate deployment into the actual production line.
The design of inkjet heads to cater to specified technical demands for a broad user base is crucial to SII for market development and maintenance for its inkjet printers. At the initial project phase, IHPC has developed a multi-fidelity approach for inkjet heads optimisation. It combined different fidelity models of inkjet head mechanisms and processed from a high fidelity three-dimensional, electromechanical fluid-structure interaction model to a simplified lumped element model (LEM).
In the next phase, the team was tasked into building an integrated platform to incorporate all models to mitigate the multi-fidelity optimisation process of the inkjet head. It involved in-depth validation for the optimal inkjet head design with experimental prototyping and extend possible simulations on other technical specifications, such as user-specific demand on droplet generation[3].
IHPC developed various physical models and incorporated them progressively into the fully integrated suite of solvers and libraries while balancing the needs of immediate deployment into the actual production line.
- [Validation] Two inkjet head channels were shortlisted. IHPC then used data collected from the experiment on the variation of droplet speed and volume changes in pulse parameters to validate the multi-fidelity model developed at the initial stage. In addition, the study would confirm and characterise the behaviour of the channels in jetting conditions.
- [Optimisation] IHPC applied optimisation technology to improve inkjet head design and operational control of the droplet generation by integrating numerical models with an optimisation toolbox to generate a computational design framework. The team also developed several design frameworks such as ink channel geometry and input electrical pulse to demonstrate its methodology.
- [Simulation] IHPC developed a computational methodology to simulate droplet’s interactions with airflows after ejection and its deposition on moving printing media. The simulations shed light on air gap effects between inkjet heads with printing substrates, thus providing numerical predictions of printing quality in different design configurations. The results would offer designers and engineers a clearer view of ink droplets trajectories and a complete description of inkjet head operations.
The final framework was a fully coupled computational fluid and piezo-mechanical solver capable of fully resolving the ink droplet ejection process from a signal pulse introduced at the actuator portion of the ink channel.
Key Results
SII applied the developed computational framework and adopted it across various design stages of its latest inkjet heads. For example, the simulations of ink circulation in a channel would enable engineers and designers to better understand circulation mechanism, allowing different design ideas of channel shapes testing. As the models were built and customised with high performance computing (HPC) resources, SII would be able to leverage the power of advanced HPC to speed up the simulation time in future.
SII applied the developed computational framework and adopted it across various design stages of its latest inkjet heads. For example, the simulations of ink circulation in a channel would enable engineers and designers to better understand circulation mechanism, allowing different design ideas of channel shapes testing. As the models were built and customised with high performance computing (HPC) resources, SII would be able to leverage the power of advanced HPC to speed up the simulation time in future.
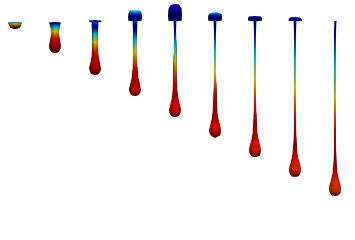
Droplet ejection from Seiko’s inkjet head by numerical simulations. Droplets are coloured by ink velocity.
Overall, the numerical platform enabled SII to see a potential 20% reduction in the inkjet head development and design time. The use of simulations also played an integral part in investigating ink behaviour and the design considerations, such as nozzle alignment, control of the ejection timing, and related operations. In addition, the platform would seamlessly integrate the existing and newly developed models, minimising disruption to SII’s operation and potential costs reduction in the configuration of the process setup. This platform could also be shared and used in other Seiko’s facilities to boost production efficiency.
Significant Progress
With the developed simulation technologies, SII’s engineering team is considering beyond the inkjet head design and extending the collaboration further on enhancing the printing quality of future advanced printer systems. It includes bringing numerical tools into the pre-design stages to test new head designs and kinematic of printing systems. Further work is also in discussion between SII and IHPC in integrating physics-based simulations with machine learning approaches for further improvement on prediction and design cycle.
Since the first project commencement in 2012, IHPC is glad to have worked alongside SII in achieving product enhancements via computational methodologies. This not only boosts SII’s confidence in continuous improvements with lower testing costs and shortens the design cycle, it is also a significant testament to IHPC’s modelling and simulation capabilities as a trusted enabler for industry collaborations.
With the developed simulation technologies, SII’s engineering team is considering beyond the inkjet head design and extending the collaboration further on enhancing the printing quality of future advanced printer systems. It includes bringing numerical tools into the pre-design stages to test new head designs and kinematic of printing systems. Further work is also in discussion between SII and IHPC in integrating physics-based simulations with machine learning approaches for further improvement on prediction and design cycle.
Since the first project commencement in 2012, IHPC is glad to have worked alongside SII in achieving product enhancements via computational methodologies. This not only boosts SII’s confidence in continuous improvements with lower testing costs and shortens the design cycle, it is also a significant testament to IHPC’s modelling and simulation capabilities as a trusted enabler for industry collaborations.
A*STAR celebrates International Women's Day
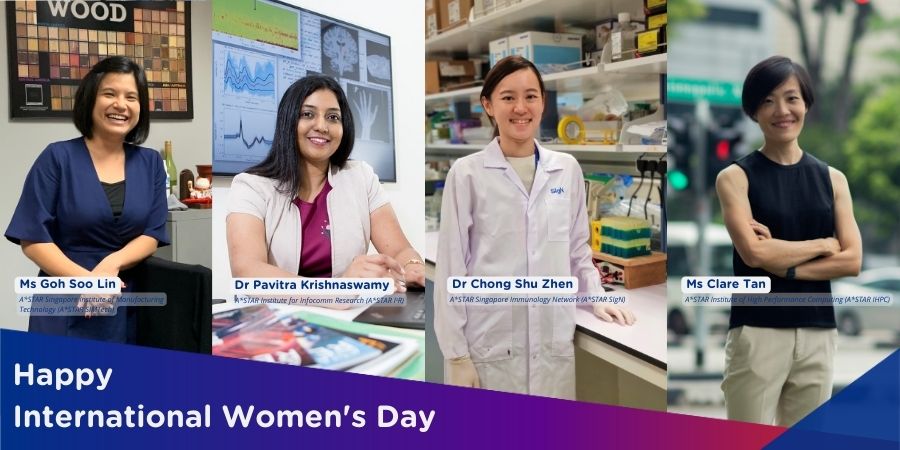
From groundbreaking discoveries to cutting-edge research, our researchers are empowering the next generation of female science, technology, engineering and mathematics (STEM) leaders.
Get inspired by our #WomeninSTEM