INTEGRATED END-TO-END AM SOLUTIONS
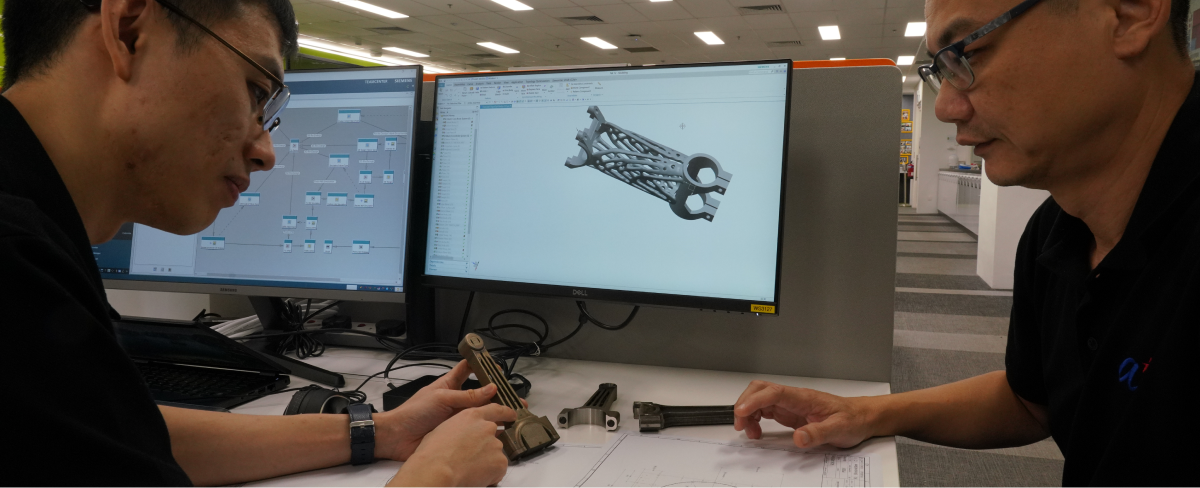
AIC has a strong history of industry partnerships and engagements through SME platform technologies to uplift and upscale the local manufacturing industry. Our significant joint lab partnerships with LLEs and MNCs have also seen the synergistic development and innovation of solutions to address industry problem statements and advance additive manufacturing capabilities.
AIC’s comprehensive suite of additive manufacturing technologies and facilities, from advanced material characterisation to high industry testing protocols, support our distinctive expertise in integrated end-to-end additive manufacturing solutions and pilot batch production.
Design and Simulation
- Design for Functionality
Design for functionality is an approach that aims to achieve the desired function of a product or system
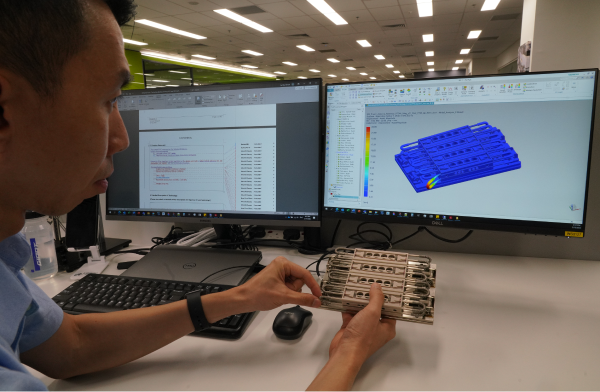
- Reverse Engineering
Reverse engineering is the process of creating a 3D digital model of an existing physical object. - Topology Optimisation
Topology optimisation is a design approach that involves optimising the shape and layout of a product or system to meet specific performance requirements while minimising weight and material usage. - Engineering Simulation
Engineering simulation involves the use of computer software to model and analyse the behaviour of a product or system under different condition. - Design for AM Production
Design for additive manufacturing (AM) production is an approach that considers the unique constraints and opportunities of AM technology during the design process.
Feedstock Development
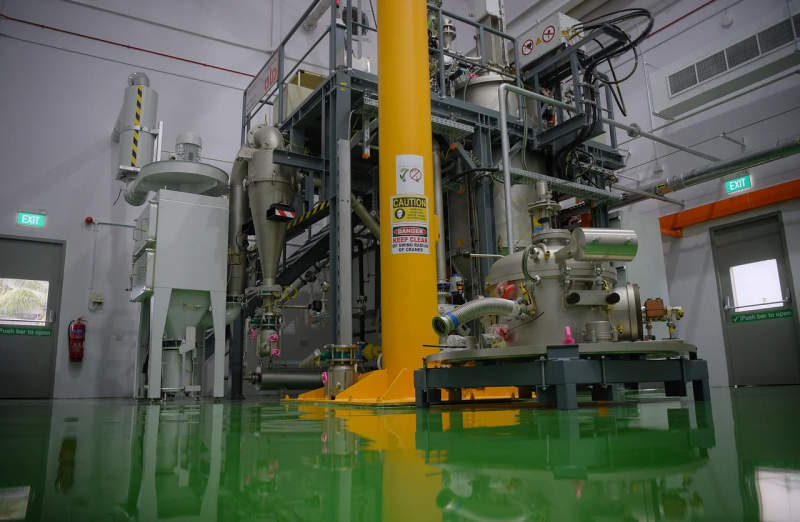
-
Development of Next Generation Materials:
- Creating and modifying materials for improved properties and characteristics
- Using new materials or modifications of existing materials through processing techniques
-
Tailoring of material properties for high-performance applications:
- Controlling the composition and structure of materials
- Modification of materials to meet specific performance requirements
-
Sustainable quality feedstock:
- Ensuring the sustainability and consistency of feedstock used in manufacturing processes
- Development of environmentally friendly feedstock options
- Implementation of sustainable practices in the manufacturing process
-
Quality-assured feedstock characterisation facilities:
- Facilities for characterising and analysing feedstock materials
- Ensuring the quality and consistency of feedstock through testing and analysis
- Implementation of quality control measures to ensure consistent performance of feedstock materials
Process Development
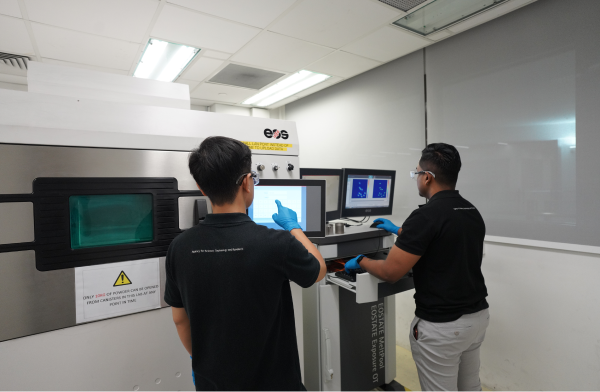
-
Wide suite of metal, polymer and ceramic 3D printers capable of running small batch production for AM components:
- Our company offers a range of metal, polymer and ceramic 3D printers capable of producing high-quality components in small batches.
- These printers are equipped with advanced features, including precision controls and automated systems, to ensure consistent and accurate production.
-
Dedicated research in ceramic printing:
- Our company is dedicated to the development of ceramic printing technology, which is a challenging and complex field.
- We have a team of experts focused on researching and developing new ceramic printing processes and materials, with the goal of producing high-quality ceramic components using AMs.
Post Processing
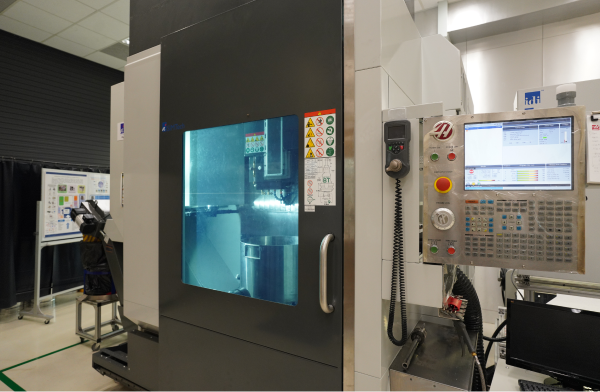
-
High precision advanced machining technologies capable of producing complex AM features
- Our company has state-of-the-art machining equipment capable of producing highly precise and complex features on AM components.
- This allows us to achieve tight tolerances, smooth surfaces, and intricate geometries that are difficult or impossible to achieve using AM alone.
-
Advanced surface enhancement technologies for functional and reliable textured surfaces
- We offer a range of advanced surface enhancement technologies, including chemical and electrochemical treatments, laser texturing, and plasma treatments.
- These techniques can be used to create functional and reliable textured surfaces on AM components, such as anti-corrosion coatings, hydrophobic surfaces, and improved adhesion properties.
-
Deep knowledge in material properties and facilities for enhanced post-heat treatment
- Our team of experts has in-depth knowledge of material properties and their behaviour after printing.
- We have facilities for enhanced post-heat treatment, including vacuum furnaces and controlled atmosphere furnaces, that allow us to improve the mechanical properties, fatigue life, and corrosion resistance of AM components.
Quality Inspection
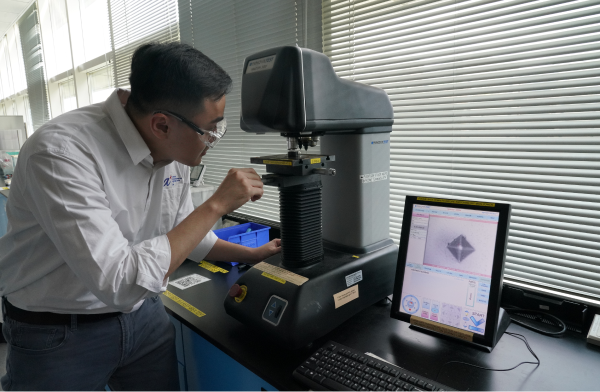
- State-of-the-art non-destructive inspection technologies to detect submicron defects:
- We offer a range of non-destructive inspection technologies, including X-ray and computed tomography (CT) scanning.
- These technologies can detect submicron defects in AM components, such as cracks, voids, and porosity, that are difficult to detect using traditional inspection methods.
- Highly accurate geometric dimensioning and tolerancing measurement systems for reliable part qualification:
- We use highly accurate geometric dimensioning and tolerancing (GD&T) measurement systems to measure the accuracy and quality of AM components.
- These systems use advanced metrology techniques to ensure that the components meet the specified requirements and standards.
What We offer
A*STAR celebrates International Women's Day
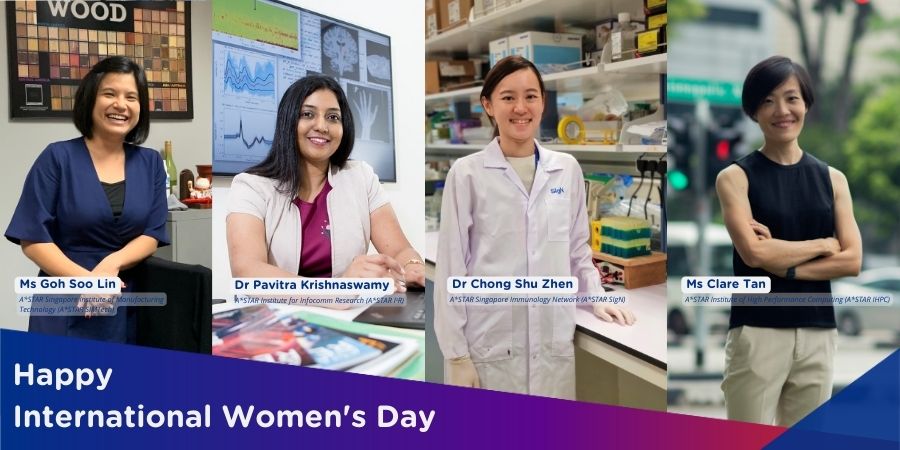
From groundbreaking discoveries to cutting-edge research, our researchers are empowering the next generation of female science, technology, engineering and mathematics (STEM) leaders.
Get inspired by our #WomeninSTEM