INDUSTRY COLLABORATIONS
To date, SIMTech has completed over 11,000 collaborations with more than 3,700 companies in the precision engineering, medtech, aerospace, automotive, marine, oil & gas, electronics, semiconductor, logistics and other sectors.
PRECISION ENGINEERING
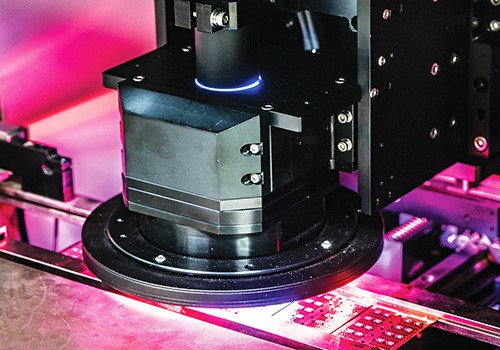
Component Technology Pte Ltd (CTech), a local SME which distributed wire/die bonder and X-ray inspection systems for the semiconductor industry, jointly conducted a feasibility study with SIMTech in 2006 on using optical methods to inspect 3D wire loop under the environment of specular, metallic surface reflection, which was an unsolved issue for the last 15 years. Based on the feasibility study result, CTech set up a new company and recruited 20 Research Engineers to work with SIMTech in 2007 to develop the world’s first 3D optical wire bond inspection system. The system has been integrated into its customers’ production lines. SIMTech has assisted CTech’s transformation from an equipment distributor to an original equipment manufacturer.
MEDTECH
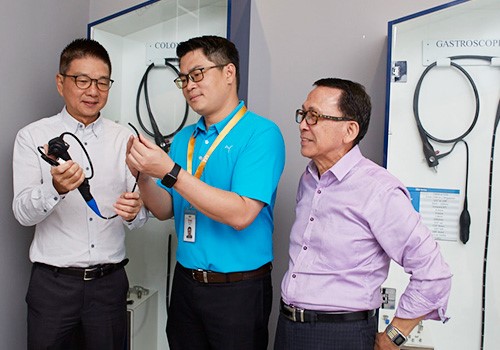
Fong’s Engineering & Manufacturing Pte Ltd, which provides Precision Machining & Assembly for the Biomedical, Optical, Aerospace & Electronics Industries, engaged SIMTech to assist in the design and development of a medical instrument to expand into manufacturing of medtech devices. The consultant helped Fong’s Engineering expedite the preparation process for product manufacturing. SIMTech also trained six of the company’s engineers in original design manufacturing facilitating Fong’s Engineering’s transformation from being a build-to-print manufacturer to an original design manufacturer.
AEROSPACE
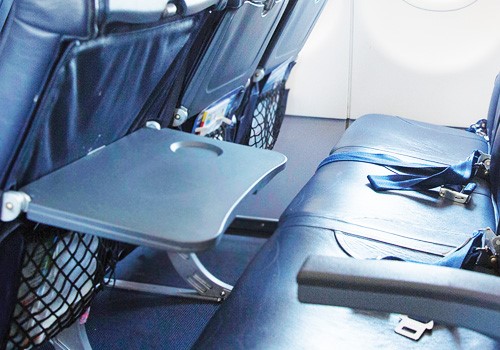
Proway Engineering Plastic Pte Ltd, a manufacturer of plastic parts and tools for the electronics industry, is one of the four Small and Medium Enterprises involved in the Collaborative Industry Project to develop polymeric cabin parts, previously sourced from overseas suppliers, for a well-known airline engineering company.
During the project, SIMTech provided the knowledge and expertise to upgrade the capabilities of Proway Engineering in the design, simulation, and manufacturing of polymeric materials according to aerospace standards to build the company’s capabilities in product design. Insert-moulding technologies were also transferred to fabricate aircraft interior parts. With these capabilities, the participating SMEs are qualified local suppliers, venturing into the aerospace industry with high value added products. After acquiring the capabilities, Proway Engineering has secured more projects and their 2014 revenue has increased by 30 per cent and is set to expand its business overseas.
JEP Precision Engineering (JEP) Pte Ltd, a home-grown company that does large format precision machining of Inconel and titanium parts ranging from combustion engine casing for commercial aircraft, to air management systems and landing gear components, has successfully transformed and digitalised its manufacturing operations.
At its new Smart Factory at Seletar Aerospace Park, JEP invested into digital manufacturing solutions in robotics, automation and smart factory software. Playing a role in JEP’s Smart Factory set-up is the implementation of the Overall Equipment Effectiveness Monitoring System (OEEMS) by SIMTech. Previously, JEP used a paper-based method to keep track of the machine operation details, such as machine set-up and downtime, which was time-consuming and prone to human error.
To address this, JEP implemented the OEEMS on all 90 machines to provide real-time machine visibility, giving live machine status updates through the dashboard, and automatically capture data on machine stoppages, such as the cause and duration of each stoppage.
By monitoring and analysing the performance of all of JEP’s 90 machines, the OEEMS improves the company's machine utilisation by close to 30 per cent and achieves 15 per cent increase in yield. The digital systems deployed have helped JEP secure higher value contracts with major aerospace Original Equipment Manufacturers (OEMs) and achieve a close to 12 per cent increase in revenue in 2017.
AUTOMOTIVE
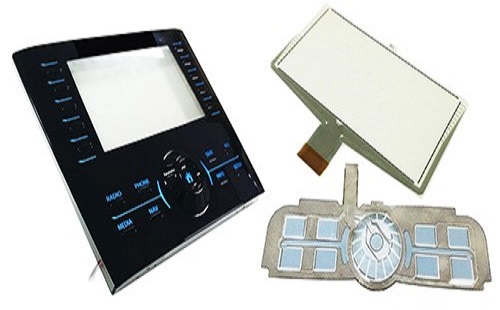
Automakers face challenges from global customers with various requirements and designs for infotainment faceplate, forcing them to produce a large variety to meet customer expectations. To help a European multinational automotive part supplier to overcome this challenge, SIMTech adopted printed electronics technology to facilitate the development of a new generation reconfigurable passenger vehicle infotainment faceplate that can be customised. A typical automotive infotainment faceplate consists of more than 20 parts of buttons and knobs. Each part, formed by a mould with tight tolerance, is costly. SIMTech developed for the collaborator printed touch sensing film and printed electroluminescent lighting for backlighting the buttons from design to fabrication.
Through this project, partnering with local precision plastic engineering solution provider, Sunningdale Tech Limited, using the 3D formed printed touch buttons and dial, the faceplate is manufactured in one tool. Huge cost saving in tool making are achieved. Customers who require varied faceplate designs benefits from faster turnaround times as the faceplate is reconfigurable. The touch buttons and dials illuminated by printed lighting give faceplates a sleek and thin appearance.
Lighting can also be applied to the control panel of medical equipment, home appliances for hygiene purposes and ease of maintenance. It functionalises conventional plastic surfaces into a new interactive platform to enhance the user experience.
MARINE
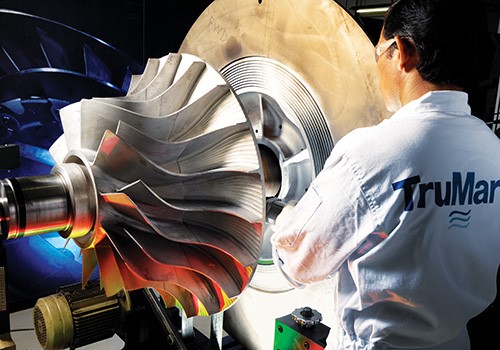
Tru-Marine Pte Ltd, a specialist in the repairs, overhaul, maintenance and spare supplies for turbochargers in marine, offshore, power plant and locomotive applications, applies Laser Aided Additive Manufacturing (LAAM) technology to repair turbocharger components. SIMTech provided Tru-marine a turn-key solution by developing a robotised LAAM system and the LAAM processes, applying for the Det Norske Veritas certificates and providing on-site training for Tru-marine’s staff.
Before the LAAM process was implemented at Tru-marine, most of the repair was carried out manually using TIG. With manual repair processes, the productivity and quality are inevitably dependent on the experience and skills of the individual operator. For example, a part needs four days to be repaired with the manual TIG-welding. With LAAM process, the repair can be accomplished in two hours. The surface quality and dimensional accuracy are much better, due to the easily controllable process.
Before, it took a few months for Tru-Marine to train the operator to be a good welder. The operators can be trained to operate the system in 1-2 weeks. Furthermore, the huge heat input from manual TIG welding causes distortion and cracking of small components. The automated LAAM process can significantly reduce the heat-input to avoid distortion and cracking. As a result, these components are repairable now. This technology has been commercialised for the repair of turbocharger components.
OIL & GAS
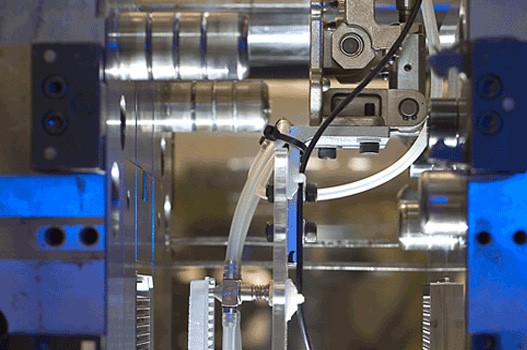
Meiban Group Pte Ltd, with strong capabilities in industrial design, tooling design and fabrication, precision moulding and contract manufacturing, set up a deep-hole drilling services company to meet the needs of the Oil & Gas industry with the assistance of SIMTech. Meiban Energy Services, a S$10 million deep hole drilling production facility and an outcome of a previous Collaborative Industry Project, is equipped with a team of highly skilled engineers, machinists and operators. The company installed a 30 metre long deep hole drilling machine (currently reputed to be longest in SE Asia) to produce higher value, higher performance and greater corrosion resistant oilfield equipment.
In partnership with another local SME, the team secured higher value orders that previously could not be manufactured in Singapore by one company alone. In addition, to cope with the rapid growth and the HPHT (High Pressure and High Temperature) harsh environment, Meiban Energy Services secured another factory with a floor space of 40,000 sq feet and new investment to provide more holistic services including large format deep hole drilling and 5-axis turn mill operations.
ELECTRONICS
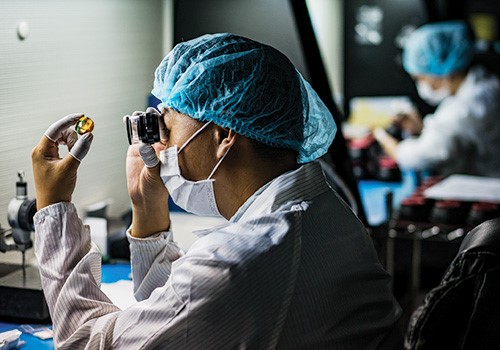
Wavelength Opto-Electronic Singapore Pte Ltd (WOE), a local SME manufacturing components for the optics industry, worked with SIMTech on several collaborations ranging from the Operational Technology Roadmap (OTR), the development of the Vacuum Laser Calorimetry System (MatCalorie™) to the secondment of SIMTech researchers through T-Up.
In 2007, WOE carried out OTR to develop long-term step-by-step strategy for business growth. Through OTR, WOE identified several key Laser and Optics technologies for future business growth and developed a five-year roadmap. The OTR exercise proved to be very successful, with many trends projected in the roadmap coming to fruition.
As the market continued to change rapidly, WOE worked with A*STAR under its enhanced OTR initiative. The enhanced OTR enabled the company to identify new key initiatives, such as Industry 4.0 connectivity solutions, intelligent optics development, security and safety systems development, and the setting up of a rapid prototyping unit. The enhanced OTR exercise also outlined key R&D plans, such as recruiting additional R&D staff and applying for patents, as well as overseas expansion plans.
Laser optics manufacturers, such as WOE, need to conduct quality control and verify the absorption rate of the coating and bulk properties of their laser optics components. However, there are no commercial systems available for absorption coefficient measurement of CO2 laser optics at 1μm and 10.6μm, and companies typically have to send their components to overseas state institutes for such coating quality measurement. To resolve this problem, WOE worked with SIMTech, from 2011 to 2013, to develop the Vacuum Laser Calorimetry System (MatCalorie™) which can conduct the required measurements. WOE subsequently licensed this technology from A*STAR to use it in-house.
In 2016, the company tapped into A*STAR’s T-Up initiative to enhance the MatCalorie™. The seconded SIMTech researcher helped to expand the range of applications of the calorimeter, automate the entire measurement process, as well as add on the industry 4.0 traceability system to monitor the system's health. Through this secondment, WOE has filed a patent application.
The calorimeter has enabled the company to promptly conduct quality control for their products, reducing cost and lead time, as well as enabling them to rectify any detected flaws quickly. Since the calorimeter was implemented in its production lines for grading lens quality, the company’s annual sales have increased by more than 20 percent. The system is also useful to other companies facing similar challenges, and potential clients from countries like Japan, France and China have already expressed interest in it.
LOGISTICS
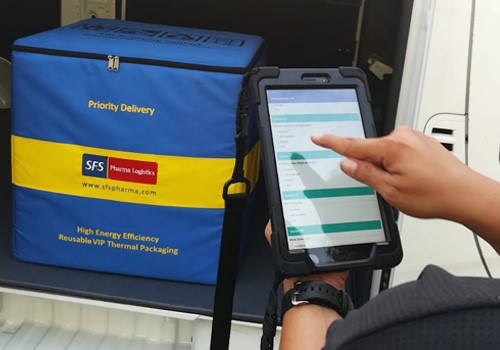
SIMTech helped the Small and Medium Enterprise SFS Global Logistics Pte Ltd, a specialty courier in the transportation of temperature-sensitive pharmaceutical and life science products and samples for clinical trials, drugs and biological substances as well as general freight forwarding services, and to implement the Workflow MOBILE™ (wfMOBILE™) system. Its aim is to go paperless in the tracking of Standard Operating Procedures compliance during the transportation of temperature-control logistics for pharmaceutical and life science products and samples by its logistics and warehouse staff in Singapore and the region. wfMOBILE™ is a platform for those in the mobile workforce to perform user-configurable business and operational transactions using Android devices.
The implementation of a cloud-based wfMOBILE™ solution enables customers to conduct paperless quality audits by customers to improve productivity by 70 per cent. Reliability in SOP compliance is improved by 30 per cent, which is of paramount importance in the Pharma Industry. Workflow in different offices in the region is standardised to ensure consistency in conducting quality audit, another critical requirement of the Pharma Industry.
The easy-to-use wfMOBILE™ also enables SFS Global Logistics non-IT Staff to build their own new flows. So far, about 10 flows have been self-created by SFS. The company hired a full-time engineer to handle SOP standardisation, auditing and compliance to further strengthen its leadership in pharma-logistics in this region. Its 1,000 sq ft fulfilment centre for pre-conditioning of thermal packaging solution in early 2015 has recently expanded to an additional 6,000 sq ft facility.
OTHERS
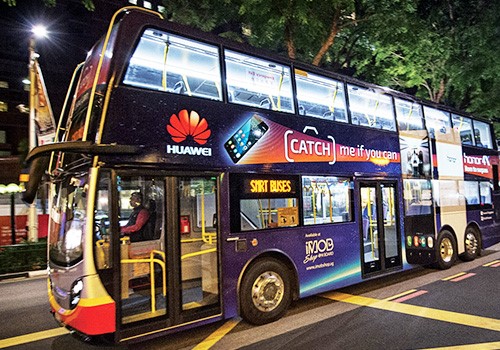
SIMTech collaborated with a local Small and Medium Enterprise, Film Screen Pte Ltd, to implement large size printed lighting on vehicles, opening up new lighted advertisement options in Singapore. The Large Area Processing technology enables Film Screen, a print technology specialist in Out-Of-Home print advertisements and Point-Of-Sale props and displays, to achieve the world’s first 12m² continuous printed lighting film implemented on a double-decker bus as a medium of advertisement for brand enhancement.
In helping Film Screen adopt the technology for the novel illuminated advertisement, Accelerate (formerly Exploit Technologies Pte Ltd and a technology transfer arm of A*STAR) facilitated the development of a large area inverter that could power the large area of printed lighting required for the bus. SIMTech resolved technical issues and power supply requirements for the printed lighting installation on the exterior of vehicles, improving the ease of application and reliability of printed lighting on vehicles. With these developed capabilities, Film Screen ventures into the untapped market for illuminated large size advertising, offering the company first-to-market advantages. This technology brings advertisers new options to elevate and add dimensions to their out-of-home advertising campaigns.
A*STAR celebrates International Women's Day
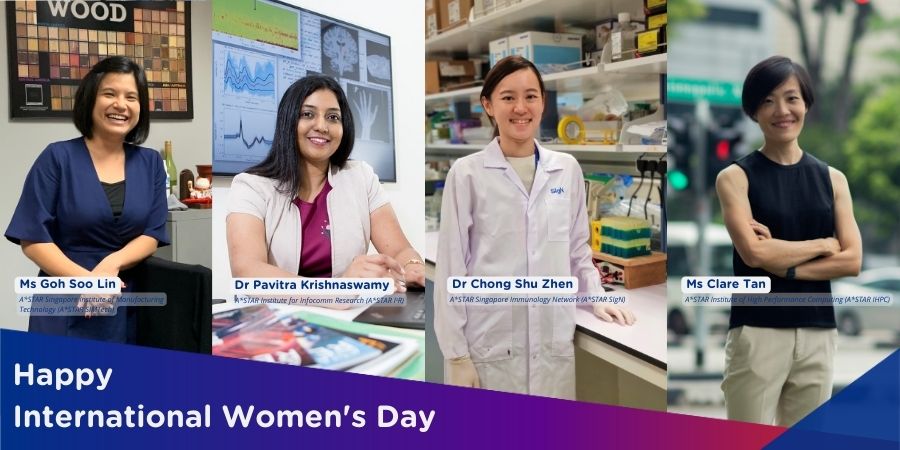
From groundbreaking discoveries to cutting-edge research, our researchers are empowering the next generation of female science, technology, engineering and mathematics (STEM) leaders.
Get inspired by our #WomeninSTEM