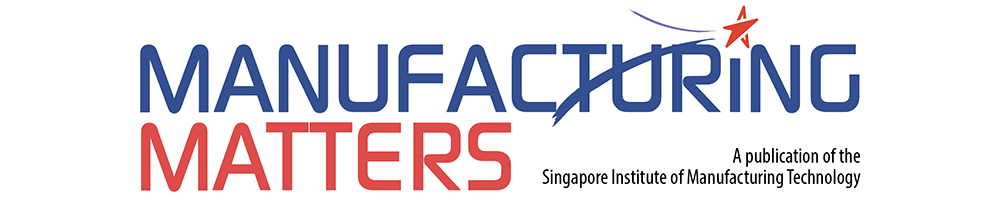
- Press Releases
- Industry Updates
- SIMTech Manufacturing Matters
- Manufacturing Matters
- SIMTech 30th Anniversary
- Events
- ASPEN2022
- BCA Green Mark (Platinum)for Healthier Workplaces and Laboratories
Building an Alcon-ic Smart Factory - Part 2
Part 2: Digital Workflow Automation System
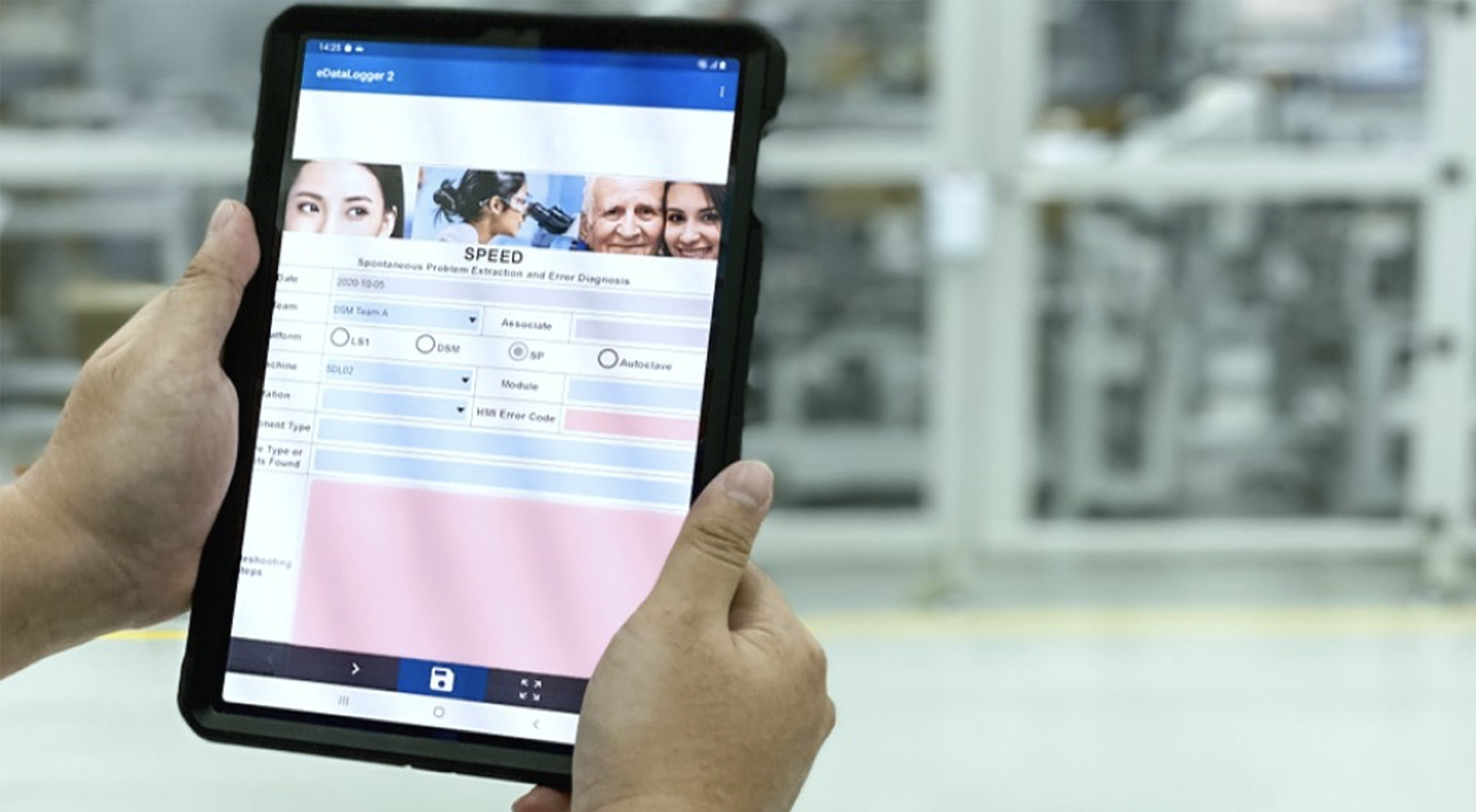
Figure 1: A screenshot of Digital Workflow Automation mobile app. Users can access past repair records and troubleshooting steps with their handphones easily in real-time.
Alcon is a global leader in eye care, dedicated to helping people improve their vision. With its 75- year heritage, Alcon is the largest eye care device company in the world1, with complementary businesses in Surgical and Vision Care.
In Singapore, Alcon Manufacturing & Logistics (AML), the first highly automated manufacturing facility in Asia, opened in 2005 and is one of Alcon’s largest contact lens manufacturing sites in the world. Utilising a state-of-the-art manufacturing process, AML supplies lenses to Alcon’s Distribution Centres (DCs) worldwide, and operates in a Make-To-Stock (MTO) environment with finite manufacturing capacity to meet the demands of each DC.
Previously, in troubleshooting process documentation, Alcon’s senior technicians would need to manually record troubleshooting steps for machine repair on paper documents, consolidate the documents, and file them in cabinets. The hardcopy repair records were difficult to find and retrieve, hindering new technicians with less experience from performing repair work independently – they would often diagnose errors incorrectly, and not know the best practices for repairs. Senior technicians would need to spend months mentoring and training new technicians before they could work independently.
SIMTech partnered Alcon to implement a Digital Workflow Automation System, digitalising their hardcopy repair documentation and creating a digital Spontaneous Problem Extraction and Error Diagnosis (Digital SPEED) platform. Working closely with Alcon’s engineers, SIMTech optimised the Digital Workflow Automation System and customised Digital SPEED forms based on their user needs and feedback, programming the Digital SPEED forms to look exactly like Alcon’s previously hardcopy forms for a smooth and easy digital transition. Besides delivering the system, SIMTech also trained Alcon’s staff in learning and implementing the new system.
Senior technicians can now use Digital SPEED forms to document and record diagnosis results and troubleshooting steps. Beside documenting repair records, the system enables mobile accessibility to technical operational manuals, component manuals, engineering drawings, and repair videos. It also provides intelligent repair suggestions, scan-and-tell service scheduling, voice-enabled data queries, access control, version control and audit trails.
Over time, the senior technicians’ knowledge and expertise are captured and digitalised in a centralised knowledge base. New technicians will be able to easily retrieve past repair records and use the data to guide them in performing the right diagnoses and repairs.
Alcon’s Digital Workflow Automation System is now operational and has since reduced Alcon’s time required for troubleshooting process documentation by 50%. Manual data entry and human errors have also been largely reduced. New technicians now work independently more quickly after orientation and basic trainings, reducing the time and effort on training young technicians by 30%.
We can now read error diagnosis records on our handphones. We use it like a handbook to guide us in doing repairs.
Tjiptoputro Adrian Kaizen, Senior Engineer at Alcon
Digitalising a manufacturing knowledge base with a Digital Workflow Automation System is just one of the aspects on which SIMTech partnered Alcon to optimise their business productivity. Read Part 1: Automated Planning & Scheduling, and look out for the upcoming stories in this series for how Alcon leveraged Industry 4.0 technologies to grow their business resilience and sustainability!
Sources
1 https://www.alcon.com/about-us
For enquiries, please contact:
Teng Wei Yuen
Senior Research Engineer, Planning and Operations Management (POM), Manufacturing System Division
Email: wyteng@simtech.a-star.edu.sg
A*STAR celebrates International Women's Day
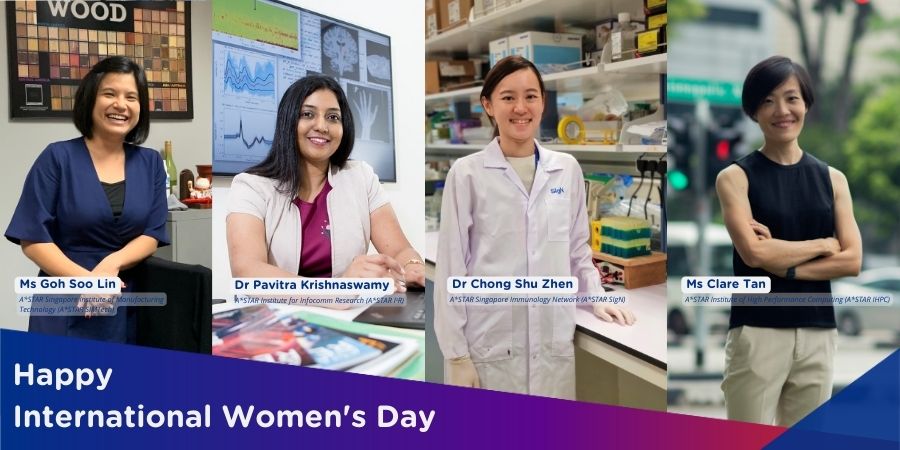
From groundbreaking discoveries to cutting-edge research, our researchers are empowering the next generation of female science, technology, engineering and mathematics (STEM) leaders.
Get inspired by our #WomeninSTEM