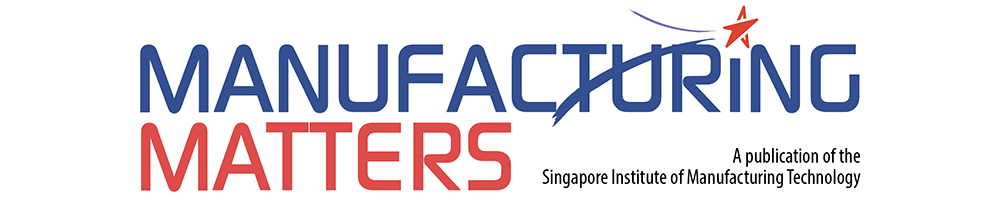
- Press Releases
- Industry Updates
- SIMTech Manufacturing Matters
- Manufacturing Matters
- SIMTech 30th Anniversary
- Events
- ASPEN2022
- BCA Green Mark (Platinum)for Healthier Workplaces and Laboratories
Paving the Way for Better 3D Printing
3D Printing Solution for Lightweight Design
Electron Beam Melting (EBM) can print 3D objects of complex shapes and designs. Its unique function of preheating the powder bed layer by layer, at elevated temperatures, lowers residual stress and reduces the need for support structures. This makes EBM very suitable for the fabrication of lightweight designs. However, it is unknown whether and how the process of EBM can affect the final products’ performance.
To address this, SIMTech researchers experimentally analysed a lightweight-designed component as a guideline for designing complex EBM built parts. The research team applied the EBM technique to manufacture two car suspension wishbones, one using conventional design and the other with thinner, computer-optimised walls.
Experimental studies reveal that the geometrically complex lightweight component can be successfully fabricated with high density and good reproducibility. The EBM-fabricated wishbones have a weight reduction of 38.6 per cent, which is close to the designed value of 41 per cent. However, mechanical testing reveals that the computer-optimised design is less stiff than the conventional design—and while the conventional design is strong enough to withstand a maximum load of over ten tons of weight, the computer-optimised design is only able to bear 73 per cent of the maximum load.
Further clarification suggests that the designer needs to consider the properties under as-built conditions, rather than using the standard computer models that assume constant material properties regardless of thickness. A trade-off between finer microstructure in the thinner EBM built samples and the contribution of rough surfaces that weakened the metal structure is also observed.
Our findings indicate that any new EBM designs involving thin walls and struts need careful attention and testing before mass production. By using updated simulation software with consideration of these limitations, SIMTech can provide a new solution for lightweight design with desirable mechanical properties.
With the expansion of the EBM application, both the automotive and aerospace industry can benefit greatly.
A*STAR celebrates International Women's Day
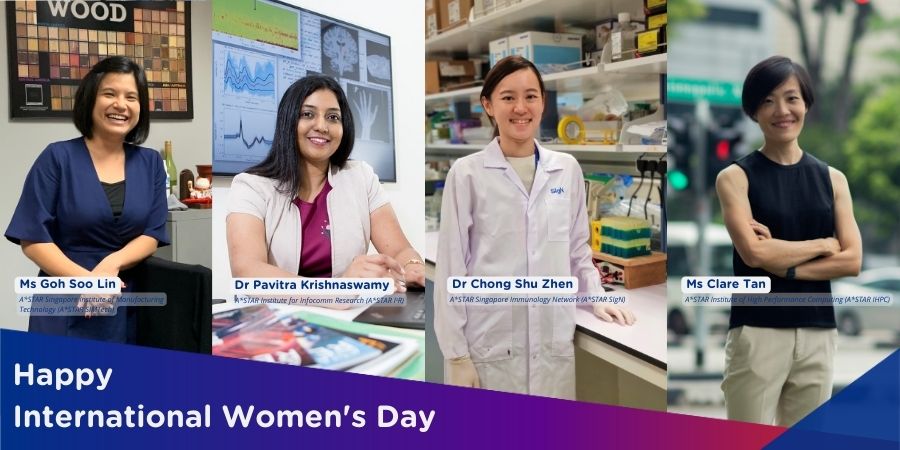
From groundbreaking discoveries to cutting-edge research, our researchers are empowering the next generation of female science, technology, engineering and mathematics (STEM) leaders.
Get inspired by our #WomeninSTEM