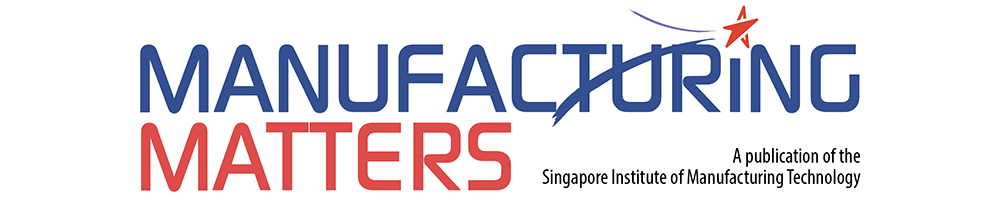
- Press Releases
- Industry Updates
- SIMTech Manufacturing Matters
- Manufacturing Matters
- SIMTech 30th Anniversary
- Events
- ASPEN2022
- BCA Green Mark (Platinum)for Healthier Workplaces and Laboratories
Building Foundations for Transformation and Growth
Leveraging SIMTech’s Operations Management and Innovation™ (OMNI™) Programme for Employee Upskilling
Team discussion of issues and opportunities using Value Stream Map
OMS Oilfield Services (OMS) is a leading oilfield services and manufacturing company in the upstream energy industry. It designs, qualifies and manufactures equipment for drilling and production with expertise in precision machining, welding, inspection and testing. Established in 1976 and headquartered in Singapore, OMS has international operations in six countries serving the Asian, Middle Eastern and North African regions. Each facility is well-equipped with modern infrastructure, professional staff and highly skilled personnel to fulfil its customers’ requirements.
With sites across multiple locations, OMS sought to enhance its operations at its Singapore HQ and further strengthen its foundation to seize growth opportunities. Recognising the crucial role of human capital, OMS turned to the Singapore Institute of Manufacturing Technology (SIMTech) to enroll a critical mass of its key management and executives in SIMTech’s Operations Management and Innovation (OMNI™) training programme to further enhance its competency in this field.
The OMNI™ training programme provided OMS with a structured approach and common language within the company to communicate effectively across all levels of the organisation. Participants gained knowledge and skills in understanding the business holistically, identifying opportunities for productivity improvement, and implementing targeted initiatives for improvement.
Working within and across departments, the participants embarked on several initiatives across the OMS value stream to improve operational efficiencies at the OMS HQ, and enhance organisational capabilities for the business. These initiatives included:
- Streamlining incoming quality inspection processes, improving cycle time by 33%
- Simplifying responses to customer requests for quotes (RFQs), reducing key process times by 80%
- Upskilling quality control inspectors
- Improving shopfloor planning, reducing administrative cycle times by an estimated 50%
- Improving vendor engagement, significantly reducing RFQ-to-Purchase turnaround time
- Further plans to develop and enhance capabilities in critical areas such as business development, project management and product design engineering for OMS products
Through the OMNI™ training programme, OMS employees enhanced their competencies in operations management. This enhanced both individual and organisational foundations, better positioning OMS to seize growth opportunities and improve the overall customer experience. One participant commented that the OMNI™ methodology is a “unique methodology that focuses on continuous improvement, integrates the best practices and flexibility, while ensuring a structured and systematic approach”.
With rapid technology shifts and structural industrial changes in the energy industry, it is imperative that OMS positions ourselves advantageously for these inevitable changes. In order not to be left behind, embarking on OMNI™ is key, with its learning outcomes used as ammunition for the changes to come. OMNI™ is also geared towards the manufacturing industry. For OMS, with manufacturing quality as one of our key pillars, the OMNI™ methodology creates an excellent pathway to excel as we strike a balance between external customer-driven metrics and internal ones.
Mr How Meng Hock, CEO of OMS
To find out more about courses by SIMTech’s Knowledge Transfer Office, visit us at www.a-star.edu.sg/SIMTech/KTO
For more information, please contact:
Mr Ma Bin, Principal Research Engineer II
Cyber-Physical Production System (CPPS)
Email: bma@simtech.a-star.edu.sg
A*STAR celebrates International Women's Day
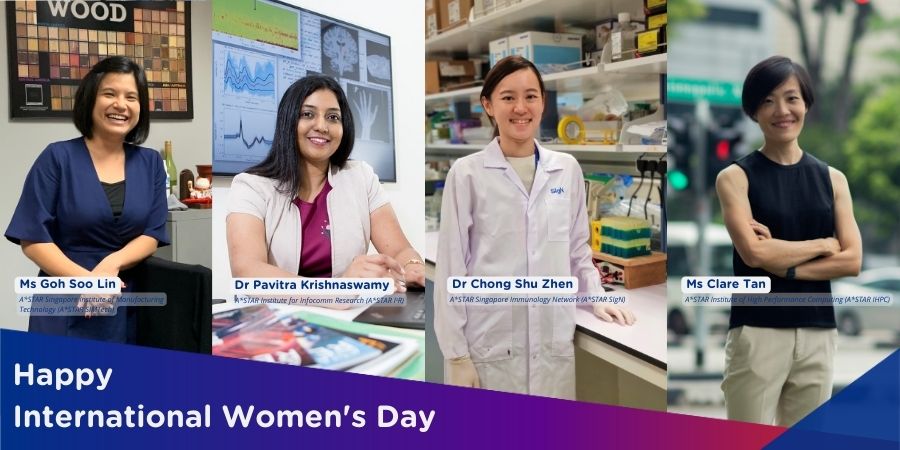
From groundbreaking discoveries to cutting-edge research, our researchers are empowering the next generation of female science, technology, engineering and mathematics (STEM) leaders.
Get inspired by our #WomeninSTEM