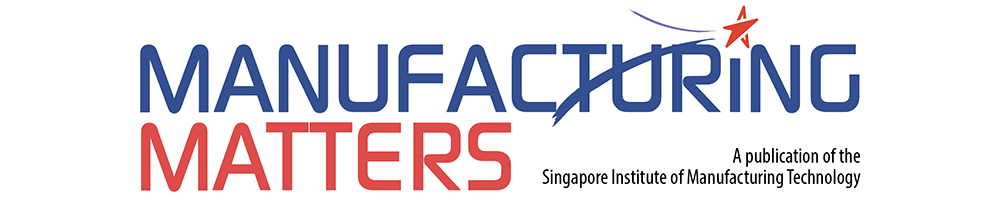
FEATURES
The Importance Of Post-Processing Technologies In Industrialising 3D Printing
Accelerated collaboration in response to COVID-19
In recent years, additive manufacturing or 3D printing technologies have advanced significantly, involving materials and equipment development to enable faster printing of larger, high-quality parts and components. With design flexibility to enable light weighting, print-on-demand capabilities to overcome long lead times and the benefit of minimising material wastage for environmentally friendlier processes, many major manufacturers are keen to adopt 3D printing for high-value manufacturing applications in various sectors, including the aerospace, medical and automotive industries. However, in almost all situations, the production of a 3D printed part is incomplete when coming off the print bed. Some parts emerge from the printer with very rough surface textures and temporary support structures still attached. These parts are still unfinished and must undergo post-processing.
Post-processing in 3D printing refers to any process or task that needs to be performed on a printed part, or any technique used to further refine the component. The finishing process can enhance the component’s surface characteristics, geometric accuracy, aesthetics or mechanical properties, among others. Traditional surface finishing technologies have been applied in the post-processing of 3D printed parts, including sanding, mechanical polishing, electropolishing, chemical smoothening, anodising, plating, painting and colouring. However, these conventional surface finishing technologies are unable to give the desired post-processing outcomes due to the inherent differences of 3D printed parts. Compared to conventionally-formed metal parts, 3D printed components are different in material composition, bulk structures, manufacturing routes and surface conditions. These differences can have detrimental effects on post-processing outcomes, like corrosion and wear resistances.
For example, anodising is not fully compatible with 3D printed aluminum alloys as the high silicon content (e.g. AlSi10Mg) and rough surfaces affect protective oxide coating formation, resulting in reduced corrosion and wear resistances.
The inherent porous bulk structure and highly rough surfaces of Fused Deposition Modelling (FDM) printed parts, coupled with difficulty in surface activation of polyethylenimine (PEI) polymer inadvertently impede metallisation via traditional plating processes.
Also, the rough surfaces of 3D printed polymer parts may require up to seven multi-layer coatings to achieve a colour topcoat with required hardness, leading to high material cost and longer processing time. Systemic research and development of new post-processing technologies is therefore required to support the industrialisation of 3D printing.
To realise this, researchers from SIMTech’s Surface Technology Group are collaborating with ST Engineering on a research programme to develop new post-processing technologies for 3D printed metal and polymer parts. For polymer parts, the research will focus on surface smoothening, pore sealing, surface pretreatment and activation, surface metallisation, as well as plating and painting as shown in the chart below.
A preliminary study on vapour smoothing of 3D printed PEI surfaces showed that the process can reduce surface roughness from 25 µm (left) to < 0.5 µm (right) as shown in the images below. Further studies will focus on the development of green chemical formulations and vapour smoothing systems.
The more challenging work will be to develop surface technologies to prepare the surfaces of 3D printed metal and polymer substrates to facilitate metal coating by electroless plating processes, followed by electroplating, also known as E-Coating or colour painting, to enhance surface properties such as aesthetics, electrical conductivity, corrosion resistance and wear resistance.
The outcomes of the research programme are expected to benefit various industries including aerospace, automotive and the 3Cs (Computers, Communications and Consumer Electronics). At the end of the research programme, SIMTech will seek to transfer these new post-processing technologies to suitable local surface finishing companies to build the local ecosystem to support these industries. On top of this research programme, SIMTech is also planning to develop other post-processing technologies for other forms of 3D printed parts and will be reaching out to the respective industries in due course.
For enquiries, please contact
Mr Tan Chee Tat, Director, PE COI
Email: cttan@SIMTech.a-star.edu.sg
Web: www.a-star.edu.sg/SIMTech-PECOI
A*STAR celebrates International Women's Day
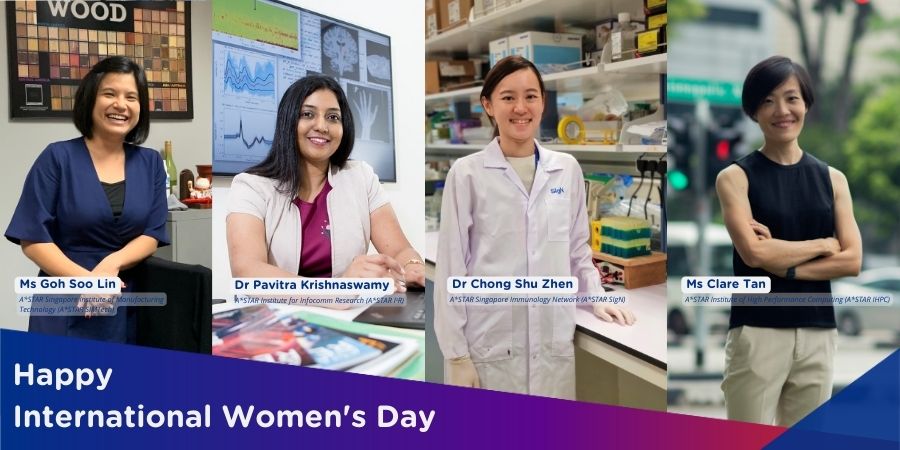
From groundbreaking discoveries to cutting-edge research, our researchers are empowering the next generation of female science, technology, engineering and mathematics (STEM) leaders.
Get inspired by our #WomeninSTEM