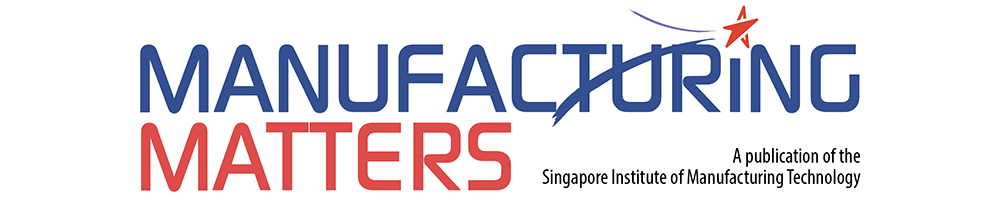
Research Spotlight
Hybrid Laser Aided Additive Manufacturing Technology Platform
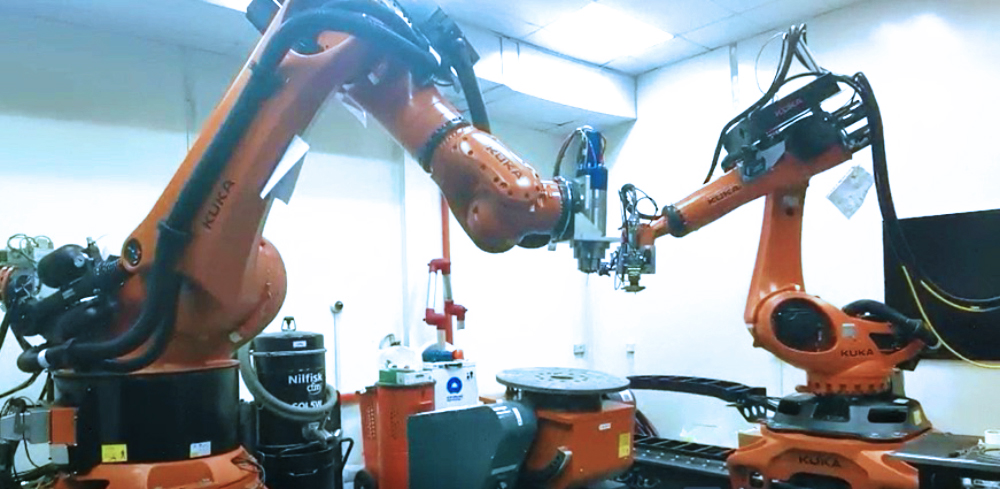
Figure 1: Dual robotic system for hybrid additive manufacturing and machining
SIMTech’s development of the Laser Aided Additive Manufacturing (LAAM) technology platform incorporates dual robotic systems for additive manufacturing and machining. The core capabilities of this platform include: i) CAM software with customisable advanced toolpaths for additive and hybrid processes for pre and post machining; ii) Process simulation integrated with machine learning for optimising deposition toolpath strategies; iii) Process development, testing and characterisation to enhance mechanical properties of both commercially available alloys and novel functional alloys; iv) Development of monitoring and control, machine learning for laser additive manufacturing (AM) and welding of complex geometries.
This flexible system can be applied for enhancing surface properties, high power laser & hybrid laser-arc welding, laser aided additive manufacturing (LAAM) with both powder and wire, as well as wire-arc additive manufacturing (WAAM). The technology platform aims to provide turnkey solutions for marine & offshore, aerospace, land transport and precision engineering in additive manufacturing, cladding and repair applications. The LAAM technology platform is also well positioned for digital transformation with pipeline efforts to integrate more process and system monitoring sensors.
Recent R&D Highlights
Development of LAAM process for bulk multi-materials and medium entropy alloy
The C300 Maraging steel C300 and 420 stainless steel are combined in a layerwise manner to achieve hierarchical heterogeneous characteristics, leading to good strength-ductility properties with ultimate tensile strength of 1.32 GPa together with an elongation of 7.5%. The increase in strength is attributed to hetero-deformation induced strengthening. In-situ deformation monitoring revealed numerous unique deformation bands, which are distinct from homogeneous materials and contributed to the increase in elongation. This research demonstrates a potential approach to extend the performance limits of existing commercial alloys.
Figure 2: Multi-material LAAM process to form high performance heterostructured high strength steels
Interstitial High Entropy Alloy (HEA) was successfully fabricated using LAAM technology. Superior ultimate tensile strength were obtained for iHEA tested at 25℃,-40℃ and -130℃. Dislocations, elemental segregation and oxide inclusions contributed to strengthening of iHEA. Room temperature strain hardening is attributed to dislocation motion; activation of both TRIP and TWIP. Minimal twinning were observed in fractured samples tested at -40℃, indicating TWIP to TRIP transition.
Figure 3: Laser aided additive manufacturing of FeMnCoCr high entropy alloy
Integrated numerical modelling and machine learning for LAAM process optimisation
The heat accumulation issue faced in continuous multi-layer LAAM can lead to inhomogeneous mechanical properties and non-uniformity in the deposited localised height and can result in accumulated dimensional deviations. A new integrated finite element (FE) simulation and machine learning approach was developed to select a multi-layer laser infill toolpath planning strategy to minimise localised heat accumulation during the deposition process. This approach can significantly improve the computational efficiency of simulating and planning of laser infill toolpath strategies.
Figure 4: Structure of the developed RNN-DNN that maps the temperature fields of previous layers and scanning pattern to the temperature field of the next layer
Computer-aided manufacturing (CAM) software
CAM software was developed in-house with complete digital workflow of the hybrid manufacturing. Major software capabilities include (1) toolpath planning for LAAM, machining, cladding, and welding, (2) machine motion calculation and simulation, and (3) customised machine code generation. In addition to the CAM functions, the software can potentially serve as a unified platform and interfaces to other digital design and analytics capabilities, such as process simulation, virtual microfactory design, and computer-assisted materials design.
Figure 5: The overview of the CAM software capabilities
A genetic evolution algorithm to automatically generate the partition and selection of appropriate infill toolpath was integrated into the software. The developed partition algorithm has been experimentally validated by benchmarking against the toolpath generated by commercial software. The scanning results demonstrated the optimized infill toolpath generated by the partition algorithm can significantly improve the building accuracy and surface flatness.
Figure 6: Layer partitioning and infill generation for LAAM
Robotic machining & hybrid manufacturing
Stiffness modelling and robot pose optimisation for robotic machining were analysed to achieve the best machining quality. Robotic machining process was development for various laser aided additively manufactured metals (e.g., Maraging steel, AISI4340, Inconel 625, HEA). Ultrasonic-assisted robotic machining was developed for composites (e.g., CFRP, natural fibre composites).
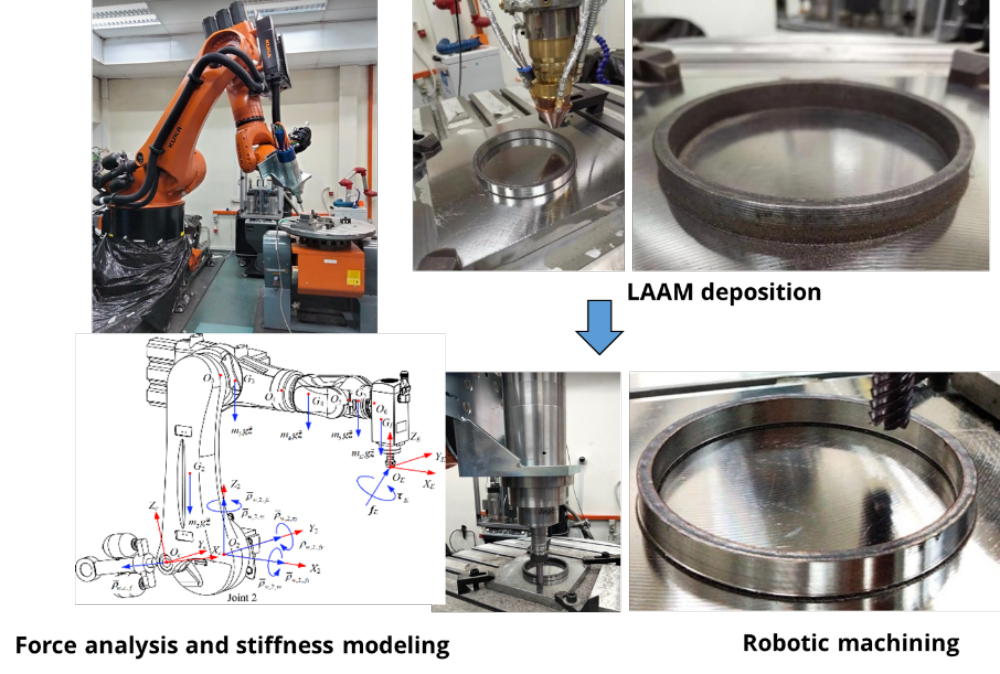
Figure 7: Robotic machining and hybrid LAAM
Process monitoring and control in hybrid LAAM
Various process monitoring and control technologies have been developed for hybrid LAAM system. Melt-pool monitoring is achieved by a coaxial CCD camera, and a feedback controller is developed to adjust the laser power in-situ to adjust the heat input and improve the dimensional accuracy. A laser profilometer is integrated into the robotic LAAM system to monitoring the surface height and topography. Conditions of LAAM system, such as the robot traveling speed and optical head’s temperature, etc., can also be monitored,. All these data can be used for process control and decision making for correction actions. For post-AM robotic machining, in-situ monitoring is performed for cutting forces, workpiece strain and vibration, tool vibration, and torques at individual robot joints. Such data can be used for machining process development and anomaly detection in automated operations.
Figure 8: Process monitoring and control in hybrid LAAM
References
- Tan, C., Y. Chew, R. Duan, F. Weng, S. Sui, F.L. Ng, Z. Du, and G. Bi, (2021) Additive manufacturing of multi-scale heterostructured highstrength steels, Materials Research Letters, Vol.9(7), 291-299, DOI: 10.1080/21663831.2021.1904299.
- Y. Chew, Z.G. Zhu, F. Weng, S. B. Gao, F. L. Ng, B. Y. Lee, G. Bi, (2021) Microstructure and Mechanical Behavior of Laser Aided Additive Manufactured low carbon interstitial Fe49.5Mn30Co10Cr10C0.5 Multicomponent Alloy, Journal of Materials Science and Technology, Vol.77, 38-46, DOI: 10.1016/j.jmst.2020.11.026.
- K. Ren, Y. Chew, N. Liu, Y. F. Zhang, J. Y. H. Fuh & G. Bi, (2021) Integrated numerical modelling and deep learning for multi-layer cube deposition planning in laser aided additive manufacturing, Virtual and Physical Prototyping, DOI: 10.1080/17452759.2021.1922714.
- P. Xu, X. Yao, S. Liu, H. Wang, K. Liu, A. S. Kumar, W. Lu, G. Bi, (2021) Stiffness modeling of an industrial robot with a gravity compensator considering link weights, Mechanism and Machine Theory, Vol.161, 104331, DOI: 10.1016/j.mechmachtheory.2021.104331.
- L. Chen, X. Yao, P. Xu, S.K. Moon, G. Bi, (2020): Rapid surface defect identification for additive manufacturing with in-situ point cloud processing and machine learning, Virtual and Physical Prototyping, 2021, Vol.16, 50-67, DOI: 10.1080/17452759.2020.1832695.
For more information, please contact Dr Bi Guijun,
Joining & Machining Group at gjbi@SIMTech.a-star.edu.sg
A*STAR celebrates International Women's Day
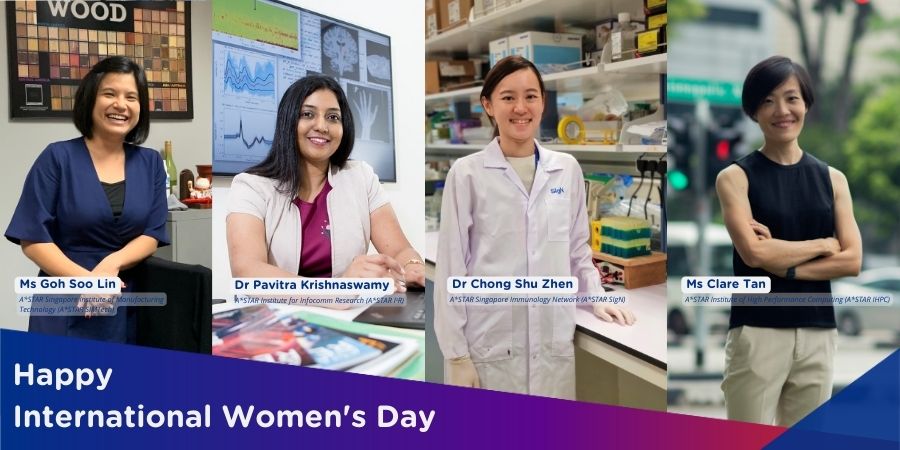
From groundbreaking discoveries to cutting-edge research, our researchers are empowering the next generation of female science, technology, engineering and mathematics (STEM) leaders.
Get inspired by our #WomeninSTEM