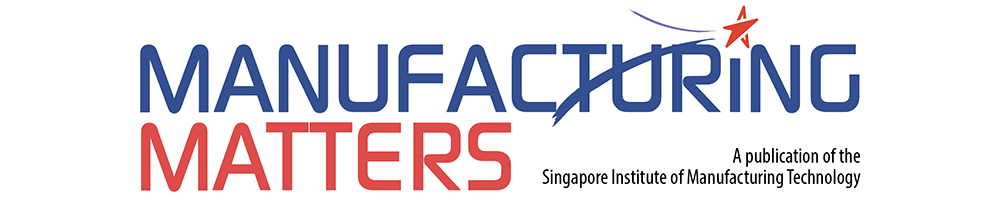
SUCCESS STORIES
Building an Alcon-ic Smart Factory - Part 1
Part 1: Automated Planning & Scheduling
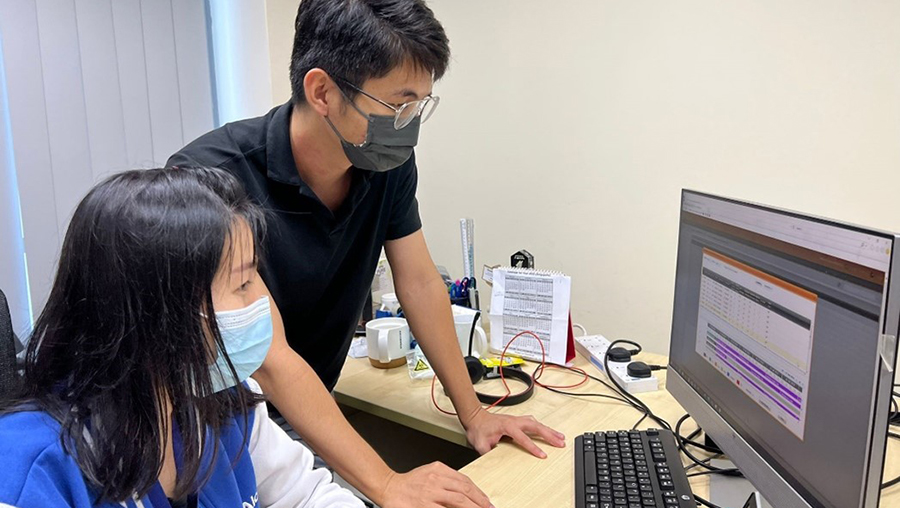
AML’s Planners performing planning & scheduling what-if analysis using the DRPSS developed on S-MOM platform
Alcon is a global leader in eye care, dedicated to helping people improve their vision. With its 75-year heritage, Alcon is the largest eye care device company in the world1, with complementary businesses in Surgical and Vision Care.
In Singapore, Alcon Manufacturing & Logistics (AML), the first highly automated manufacturing facility in Asia, opened in 2005 and is one of Alcon’s largest contact lens manufacturing sites in the world. Utilising a state-of-the-art manufacturing process, AML supplies lenses to Alcon’s Distribution Centres (DCs) worldwide, and operates in a Make-To-Stock (MTO) environment with finite manufacturing capacity to meet the demands of each DC.
Through SIMTech’s Digital Transformation & Innovation™ (DTI™) Programme in 2019, Alcon developed a transformation roadmap, involving 8 key digital initiatives:
- Digitalised Data Entry
- Real-Time Nerve Centre xDashboard
- Real-Time Intelligent Overall Equipment Effectiveness (OEE) Monitoring
- Augmented Reality (AR) Diagnostics for Machine Maintenance
- Capability Library (Skills/Awareness/Mindsets)
- Digitalised Manufacturing Knowledge Base
- Smart Manufacturing Operations Management (S-MOM)
- Predictive Maintenance
SIMTech and Alcon embarked on a 3-year research project to support the implementation of the S-MOM and Predictive Maintenance systems. For S-MOM, more research in the area of planning & scheduling was required to develop a set of customised, dynamic scheduling rules, which considered various inputs, such as setup and conversion, planned maintenance, and machine loading preferences. Predictive maintenance was also a required research area, as most maintenance approaches in manufacturing today still do not have predictive capabilities, and operations often suffer from delayed detection of breakdowns.
(1) Planning & Scheduling
AML’s then planning and scheduling process was Excel-based and manual. Planners had to consider the average demand for each Stock Keeping Unit (SKU), the maximum number of lines per product type, power-to-track configuration, lot and formation change constraints, transportation lead-time to the DC, pack size distribution, configurable flexible lines, current on-hand quantity, and inventory coverage of the SKU at the specific DC, among other factors. These involved heavy planning efforts with high susceptibility to human errors.
An integrated Distribution Requirements Planning & Scheduling (DRPS) solution was proposed to address these challenges by mapping the manual activities to various integrated modules. In response to AML’s operational constraints and global demand fulfilment scenarios, the SIMTech project team designed and developed this new system, extending the scope and coverage of our current S-MOM system. The Planning & Scheduling (P&S) team designed four new modules – the Demand Management module, Requirement Planning module, Production Scheduling Engine, and Reporting & Integration module. All modules were integrated into the S-MOM platform.
This integrated DRPS solution is now operational and has since reduced planning efforts by over 80% from 3 days to 2-3 hours per week. Duplicated data entry efforts and human errors have also been starkly reduced. In addition, planners can now perform what-if scenario analysis and evaluation of demand fulfilment plans for different distribution centres and fine-tune the replenishment plans, considering real operational factors such as manufacturing constraints, demand fluctuations, and inventory levels.
This integrated DRPS solution is now operational and has since reduced planning efforts by over 80% from 3 days to 2-3 hours per week.
Planning and scheduling and smart manufacturing operations management is just one of the aspects on which SIMTech partnered with Alcon to optimise their business productivity. Look out for the upcoming stories in this series for how Alcon leveraged Industry 4.0 technologies to grow their business resilience and sustainability!
Sources
1 https://www.alcon.com/about-us
For enquiries, please contact:
Dr Xu Chi
Group Manager, Planning and Operations Management (POM), Manufacturing System Division
Email: cxu@simtech.a-star.edu.sg
Dr Ng Huey Yuen
Acting Deputy Director, Knowledge Transfer Office (KTO)
Email: nghy@simtech.a-star.edu.sg
A*STAR celebrates International Women's Day
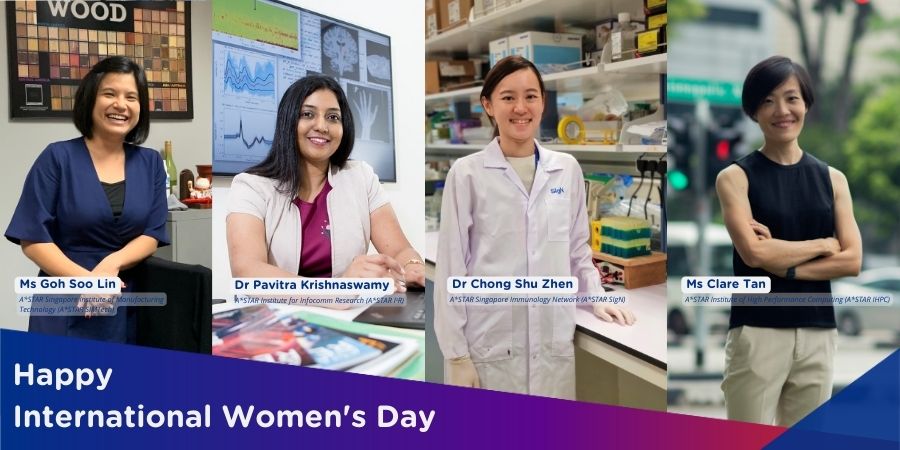
From groundbreaking discoveries to cutting-edge research, our researchers are empowering the next generation of female science, technology, engineering and mathematics (STEM) leaders.
Get inspired by our #WomeninSTEM