Press Releases
Local SMEs innovate to transform, thrive amidst Covid-19 pandemic through public-private Joint Labs and Innovation Factory collaboration
A*STAR launched two R&D joint laboratories with local manufacturing SMEs and opened its pilot Innovation Factory @ SIMTech (Singapore Institute of Manufacturing Technology) today (15 December 2020). The latter is in partnership with Enterprise Singapore (ESG), and saw 14 local SMEs and two trade associations come onboard. Second Minister for Trade and Industry Dr Tan See Leng graced the event.
Public-private partnerships such as these continue to play a key role in the innovation and adoption of advanced manufacturing technologies by businesses in this fourth industrial revolution, amidst the disruption caused by the COVID-19 pandemic.
1. About the joint laboratories
Local SMEs Tru-Marine and Abrasive Engineering (AE) joined A*STAR’s Advanced Remanufacturing and Technology Centre (ARTC) consortium as members in 2013, and continue to co-innovate with A*STAR to become more competitive.
a) A*STAR-Tru-Marine Joint Lab
Tru-Marine is a local SME that specialises in the maintenance, repair and overhaul (MRO) of turbochargers1 for marine and offshore, power plant and locomotive applications.
Under a new joint lab with a combined investment of S$6 million over three years, ARTC will help Tru-Marine develop a new predictive maintenance-as-a-service business model. The joint lab will create new jobs and upskill workers in the areas of digital fluency, data engineering and data science.
This comes after a successful digital transformation project with ARTC, with another underway (details in Annex A).
The new business model is set to disrupt the maritime industry by helping ship owners, managers and operators save costs through proactive, reliability-based maintenance. To transform the value chain for proactive MRO service, Tru-Marine will build an ecosystem to include its global network of partner repairers and suppliers as part of an integrated supply chain.
To build the new business model, the research team will develop a real-time monitoring system for marine turbochargers that:
- Monitors the health of turbochargers by monitoring engine turbocharger parameters holistically and correlating them with corresponding vibration levels
- Predicts potential problems before they arise by using smart sensors and advanced edge analytics
- Makes timely recommendations using the Industrial Internet of Things (IIoT) technologies
- Shows real-time information on digital dashboards to facilitate decision-making
When a potential turbocharger failure shows up on a dashboard, Tru-Marine will activate one of its partners in its global network, depending on who is closest to the ship in question. The customer can then get its turbocharger fixed at the nearest possible port.
Through early intervention, Tru-Marine’s customers can pre-empt failures, cut unplanned downtime, and reduce inventory of spare parts (by stocking only specific spare parts needed and in the right quantities).
A*STAR, Tru-Marine and Singapore-based container ship operator Pacific International Lines (PIL) signed a memorandum of understanding today to pilot this predictive maintenance-as-a-service application on PIL’s ships.
b) A*STAR-Abrasive Engineering Joint Lab
AE is a local SME that makes sandblasting2 and shot peening3 machines, and provides such services, for the aerospace, marine, automotive and oil and gas industries in Singapore and globally.
Under a new joint lab with a combined investment of S$5.5 million over three years, ARTC will help AE build advanced manufacturing capabilities to make four new types of products and enter new industries such as additive manufacturing and fast-moving consumer goods (FMCG). The joint lab will create at least nine new jobs.
This investment comes after AE’s past R&D investments paid off from years of co-innovation with ARTC (details in Annex B).
The joint lab will pursue four key projects, after which AE will manufacture its new products locally:
- Develop higher precision valves4 for more industries: Using magnetic and microwave particle sensing technologies, the research team will develop magnetic and non-magnetic valves with higher flowrate and precision for the aerospace, automotive and marine and offshore industries. With the new valves, AE will be able to handle more types of components and serve more businesses and sectors.
- Develop a high precision valve for additive manufacturing: Based on AE’s valve technology, the team will develop a valve with high accuracy and smart feedback control for additive manufacturing. The new valve will give manufacturers much-needed precision in the dispensing of powder in 3D printing, a key determinant of quality.
- Develop a high precision valve for FMCG applications: The team will develop a valve with high accuracy for the FMCG sector, also based on AE’s current technology. The new valve will give manufacturers precision and control needed for hyper-personalisation in manufacturing products.
- Develop a fully-automated blast room: Using robotics, the team will automate the sandblasting process for marine and offshore applications. AE will sell the automated solution to businesses to help raise throughput and productivity (industrial robots can handle higher volumes and pressure than humans), and improve quality (robots can blast in a uniform manner and without human error).
The joint lab will also tap the expertise of scientists and engineers from two other A*STAR units: Institute of High Performance Computing (IHPC) and National Metrology Centre (NMC).
2. A*STAR’s pilot Innovation Factory @ SIMTech in partnership with ESG
14 local SMEs and two trade associations joined the pilot Innovation Factory @ SIMTech today as members and strategic partners respectively (details in Annex C). Under the initiative, SIMTech has kicked off more than 10 projects to co-create products with these companies.
At this new co-creation space, A*STAR’s scientists and engineers will facilitate the process for companies, particularly local SMEs, to become product owners by helping them to design and create new products. This will help them move up the value chain and become more competitive.
The journey will take place in four stages: ideation, design, engineering and application. A*STAR will use design thinking strategies and advanced manufacturing technologies to help companies, and pull expertise from across its research units and the rest of the R&D ecosystem for these collaborations. A*STAR worked with ESG to reach out to SMEs across sectors to understand market demands and identify key challenges and skills gaps faced when developing new products.
Once a company is ready to scale up production for a newly developed product, such as when a prototype is ready, it could move to the complementary Model Factory @ A*STAR to manufacture it using the most suitable smart manufacturing solutions drawn from Industry 4.0 technologies.
With a floor area of about 1,400 sq ft at SIMTech, the pilot set-up features a design workstation with software tools, a workshop with electrical and mechanical design tools, and manufacturing equipment such as 3D printers. A full-scale version of the Innovation Factory @ SIMTech is slated to open at CleanTech Park in the Jurong Innovation District in 2021.
To speed up adoption of new technologies and practices, and ensure that newly developed products adhere to international safety, quality and interoperability, and
reliability standards, participating companies can tap ESG’s5 library of biomedical and Industry 4.0 standards. ESG and the Singapore Standards Council will also work with the Innovation Factory @ SIMTech to engage training providers to organise workshops and training programmes to help companies use these standards effectively.
3. Quotes from A*STAR and partners
On the joint labs with Tru-Marine and AE
a) Dr David Low, Chief Executive Officer of ARTC and Executive Director of SIMTech at A*STAR:
“To stand out from the competition, businesses must innovate. Digitalisation is key. SMEs are the bedrock of Singapore’s economy, and A*STAR will continue to help them build new capabilities and business models to move up the value chain and become more competitive. We continue to deepen R&D partnerships with local companies such as Tru-Marine and AE, helping them discover new possibilities as they transform and reinvent themselves in the age of Industry 4.0 and amidst the COVID-19 pandemic. I am glad that Tru-Marine and AE have benefited from co-innovation with ARTC over the years, and I am excited to continue the innovation journey together.”
b) Mr David Loke, Executive Chairman, Tru-Marine:
“Innovation is the lifeline of our company. COVID-19 has compelled us to speed up digital transformation. To stay relevant, we must reinvent ourselves and do things differently. As it is difficult for SMEs like us to innovate on our own, we need strategic partners like ARTC with deep capabilities in advanced manufacturing. ARTC has been rendering tremendous support to Tru-Marine in digitalising our operations, and now we are on track to build a new business model together that will transform the industry.”
c) Mr Tan Ser Hean, Managing Director, AE:
“If we are to survive – let alone thrive – we have to innovate. Innovation must become second nature. I attribute much of our success since we joined the ARTC consortium to ARTC scientists and engineers who helped me prepare my business for Industry 4.0. Could we have done it on our own? Perhaps, but it would have taken us a lot more time and cost a lot more money. We have reaped the benefits of digitalisation – our R&D investments with ARTC have paid off – and we want to do more. Digitalisation is more urgent and important now than ever. If we are to survive the COVID-19 crisis, we must continue to invest in R&D even if it means having to tighten our belts in other areas. I am glad that we have in ARTC a trusted partner whom we know will deliver the results we want.
On the Innovation Factory @ SIMTech
d) Dr David Low, Chief Executive Officer of ARTC and Executive Director of SIMTech at A*STAR:
“There is no better time for companies to pursue innovation, in order to come out stronger from the pandemic. This is where public-private partnerships can open up new possibilities for businesses to ideate new innovative products and become product owners, enabled by advanced manufacturing and digital solutions. The Innovation Factory @ SIMTech is the starting point for companies who are trying to figure out how they can develop new products to differentiate themselves from the competition. It helps companies design the right products for the business, while the Model Factory helps them make those products right. Together with ESG, we look forward to catalysing a culture of innovation in businesses, to see exciting products emerge and help our partners thrive.”
e) Mr Simon Lim, Executive Director for Manufacturing and Engineering, ESG:
“The current economic climate has accelerated the need for SMEs to venture into product ownership, so as to create a stronger value proposition for their customers locally and overseas. To quicken the process, one key strategy is to work with knowledge partners and existing R&D ecosystem players to bridge science with business. The Innovation Factory @ SIMTech allows companies to take the first step in building new design capabilities, and to gain access to equipment, relevant standards, and industry-based expertise. It will aid them in developing new solutions that address problem statements in the industry.”
f) Mr Eugene Goh, Managing Director, JM Vistec System:
“Having worked with A*STAR for more than 10 years now, we have seen our joint R&D investments pay off, such as the projects we did with SIMTech and ARTC. Innovation is critical for businesses, and for SMEs like us, collaborating with scientists and engineers at A*STAR enables us to build the R&D capabilities we need for success. Trying to design and create a new product without domain knowledge from experts at A*STAR would be like trying to build something in the middle of the desert alone and with no resources. The Innovation Factory @ SIMTech is a brilliant initiative by A*STAR that I foresee will help many SMEs – we are thrilled to join as a member and continue our innovation journey with A*STAR. I encourage SMEs from across industries to come onboard to discover new possibilities for product development together.”
About the Agency for Science, Technology and Research (A*STAR)
The Agency for Science, Technology and Research (A*STAR) is Singapore's lead public sector R&D agency. Through open innovation, we collaborate with our partners in both the public and private sectors to benefit the economy and society. As a Science and Technology Organisation, A*STAR bridges the gap between academia and industry. Our research creates economic growth and jobs for Singapore, and enhances lives by improving societal outcomes in healthcare, urban living, and sustainability. A*STAR plays a key role in nurturing scientific talent and leaders for the wider research community and industry. A*STAR’s R&D activities span biomedical sciences to physical sciences and engineering, with research entities primarily located in Biopolis and Fusionopolis. For ongoing news, visit www.a-star.edu.sg.
Media Contacts
Elizabeth Han
Assistant Head, Corporate Communications
A*STAR
DID: +65 6517 7940
Mobile: +65 9759 2284
Email: elizabeth_han@hq.a-star.edu.sg
Robin Chan
Head, Corporate Communications
A*STAR
DID: +65 6826 6281
Mobile: +65 9830 2610
Email: robin_chan@hq.a-star.edu.sg
ANNEX A
ARTC & TRU-MARINE: CO-INNOVATION LEADING UP TO JOINT LAB
ARTC helps Tru-Marine to pilot digitalisation
Under A*STAR’s Technology for Enterprise Capability Upgrading (T-Up) scheme6, ARTC seconded an engineer specialising in process redesign to Tru-Marine from 2017 to 2018 to kickstart the company’s digital transformation.
The ARTC engineer automated one of Tru-Marine’s shopfloor workflows as a pilot, which included process reengineering using digital tools to replace manual and paper-based information flow with electronic formats.
In the transformed part of its factory, Tru-Marine’s processes are now more efficient, enabling quicker response to customer needs. Tru-Marine decided to embark on a second T-Up to replicate this success for the rest of its shopfloor.
ARTC helps Tru-Marine further digitalise factory operations
COVID-19 has compelled Tru-Marine to speed up its digital transformation, according to the company. Building on work done in the first T-Up, ARTC seconded another engineer to Tru-Marine this year to digitalise the company’s entire factory operations for a smart and connected factory.
Over a year, the ARTC engineer, who specialises in programming, will digitalise Tru-Marine’s shopfloor processes using the Internet of Things (IoT) connectivity, data analytics and machine learning. Tru-Marine also plans to build a control room modelled on the Manufacturing Intelligence Control Room (MICR) at the Model Factory @ ARTC, with real-time monitoring of operations.
ANNEX B
ARTC & AE: CO-INNOVATION LEADING UP TO JOINT LAB
Since AE joined the ARTC consortium in 2013, it has:
- Made two new products through co-innovation with ARTC
- Digitalised its factory operations with the help of a ‘borrowed’ ARTC scientist under A*STAR’s T-Up scheme
- Started developing long-term growth strategies driven by technology with the help of experts under A*STAR’s Operation & Technology Roadmap (OTR) programme
On its innovation journey, AE has grown its business, having:
- Increased its annual revenue by nearly 50 per cent, from S$6.4m (2013) to S$9.5m (2019)
- Created more jobs, growing staff strength by over 30 per cent, from 35 in 2013 to 48 today
- Expanded its factory operations, doubling the floor area of its facility from 15,000 sq ft to 30,000 sq ft in 2013
Product innovation: a digitalised shot peening machine
With the help of ARTC scientists and engineers, AE has made its shot peening machines digital, making them more competitive in the age of Industry 4.0. These digitalised shot peening machines come with an IIoT box with data analytics, and a digital dashboard. AE started selling these high-value, fully automated machines in 2018 after a year of joint R&D, and has sold 15 units since.
Using these newly digital machines, manufacturers can improve the process and result of shot peening, and digitally record every step of the process for traceability. The machines can also be digitally connected to the MICR at the Model Factory @ ARTC for an overview of manufacturing operations in real time. If a manufacturer has a similar control room, it can do the same.
Product innovation: a valve with high accuracy to meet industry demands
With the help of scientists and engineers from ARTC and NMC, AE used microwave sensors to develop a new type of valve that:
- Has high accuracy (95%), meeting industry demands
- Works with both magnetic and non-magnetic materials, defying convention7
- Is compatible with an IIoT environment
- Is less prone to wear and tear, given the contactless nature of sensors
The team developed the product in under two years – less than half the time AE took to make another product, a magnetic valve, on its own. AE uses these new valves to improve the machines it sells, and sells the valve as a component to its competitors too.
ARTC helps AE digitalise factory operations
Under A*STAR’s T-Up scheme, ARTC seconded a scientist specialising in Industry 4.0 IoT architecture to AE in 2019 to help digitalise the company’s factory operations.
Over a year, the ARTC scientist helped AE build an industrial IoT architecture with wireless infrastructure to connect machines on its shop floor, and develop a smart dashboard for real-time monitoring. AE’s managers are now able to see data of its manufacturing operations in real time.
ANNEX C
INNOVATION FACTORY @ SIMTECH: MEMBERS & STRATEGIC PARTNERS
Members
14 local SMEs from across sectors joined the Innovation Factory @ SIMTech today as members:
- ATC (Applied Total Control Treatment Pte Ltd) – specialises in surface finishing for the aerospace, oil and gas, semiconductor, biomedical and optical industries
- Blue InCube Pte Ltd – a venture builder that focuses on innovative robotics, automation and data analytics startups that transform businesses and disrupt industries
- Data Terminator Pte Ltd – a data leakage protection specialist that provides certified equipment and services for secure electronic data erasure, destruction and IT asset disposal
- Delphic Manufacturing Solution Pte Ltd – specialises in high-mix, low-volume precision tooling solutions for the electronics industry
- Ecospec NovelTech Pte Ltd – invents and develops green solutions for health and environmental benefits by using patented technology
- Edible Creations LLP – reduces plastic waste and promotes urban nutrition through edible cutlery
- Flexmech Engineering Pte Ltd – a machine solutions provider that specialises in grinding, computer numerical control and 3D printing equipment as well as SME-focused Industry 4.0 solutions
- GINLEE Studio Pte Ltd – a contemporary fashion design studio
- JM Vistec System Pte Ltd – specialises in 2D, 3D and artificial intelligence imaging solutions for industrial optical metrology applications
- Line8 Pte Ltd – a developer and manufacturer of power track systems
- Makers Ideas Pte Ltd – specialises in industrial design, engineering design and consultancy services
- Mdesign Solutions Pte Ltd – a consulting company that develops innovative products for industries such as consumer electronics, medical devices and telecommunications
- pFIBRE Pte Ltd – a resin manufacturing company that makes biodegradable flexible packaging film
- Sanwa Plastic Industry Pte Ltd – manufactures high precision, functional plastic tools and molded components for the energy, automotive and medical sectors
Strategic partners
The Singapore Precision Engineering and Technology Association (SPETA) and Singapore Manufacturing Federation (SMF) also joined the initiative today as strategic partners to help encourage product innovation amongst industry players together with A*STAR and ESG.
1 A turbocharger is a critical component of a ship’s engine; it makes the engine more efficient by helping to power it using heat energy emitted by the engine itself.
2 Sandblasting is a surface finishing process in manufacturing.
3 Shot peening is a process to strengthen metal parts and make them more durable.
4 Shot peening entails blasting shot (round metallic, glass or ceramic particles) on the surface of a component. A valve in a shot peening machine measures the impact of each blast, a key determinant of the outcome, so accuracy is important. There are two types of valves: magnetic and non-magnetic.
5As the national standards body, Enterprise Singapore, together with the Singapore Standards Council (SSC), facilitates the development and promotion of Singapore and international standards. 6Under its T-Up scheme, A*STAR lends scientific talent to local SMEs to help them build capabilities to be more competitive.
7The valve and shot must both be either magnetic or non-magnetic, depending on the type of component. This new valve can handle both, breaking with convention.
Join the Innovation Factory @ SIMTech now:
https://www.a-star.edu.sg/SIMTech/innovation-factory
Click to watch the Official Launch of Pilot Innovation Factory video
Read more:
The Straits Times: A*Star launches two new joint labs with local engineering SMEs, with total investment of $11.5 million
A*STAR celebrates International Women's Day
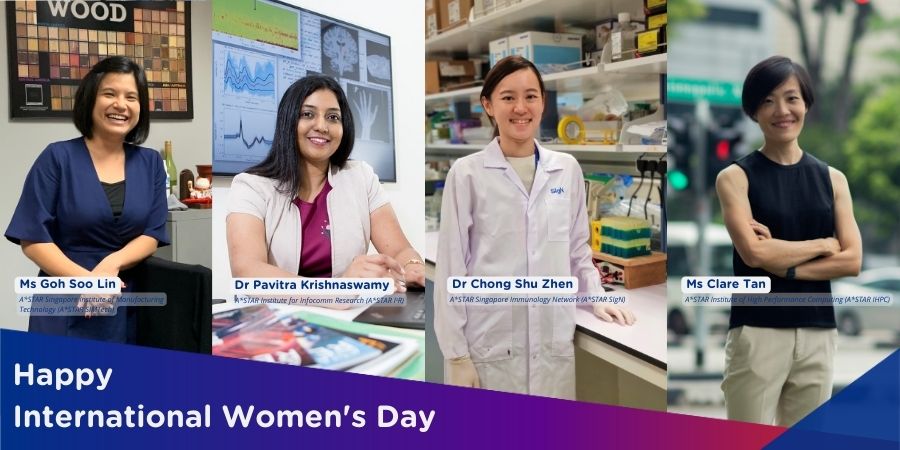
From groundbreaking discoveries to cutting-edge research, our researchers are empowering the next generation of female science, technology, engineering and mathematics (STEM) leaders.
Get inspired by our #WomeninSTEM