4 Innovation Centres
Precision Engineering Centre of Innovation
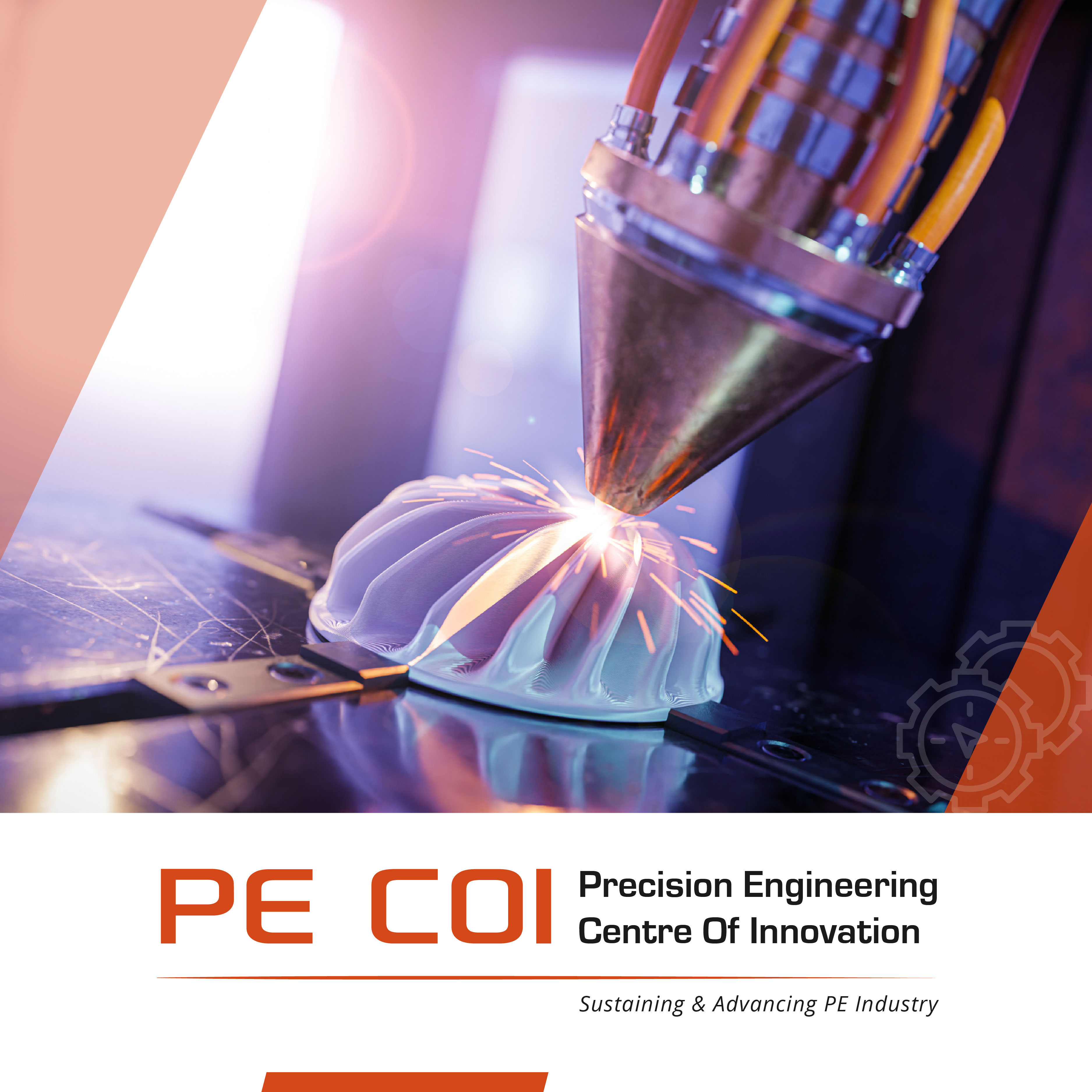
ABOUT PRECISION ENGINEERING CENTRE OF INNOVATION
Precision Engineering (PE) is the fundamental building block of manufacturing. From nanoscale dimensional semiconductor chips to the tough drill bits used in oil exploration, the PE sector is critical to the electronics, aerospace, automotive, marine & offshore and MedTech industries. Its role in the Singapore industrial landscape is evident as the PE industry employs a quarter of the local manufacturing workforce.
MISSION & ROLES
Mission
PE COI aims to support Precision Engineering companies in leveraging SIMTech’s manufacturing technologies to sustain, transform and advance their businesses locally and internationally.
Roles
PE COI upgrades the precision engineering industry through:
- Industry Development
- Assist companies’ transition towards sustainable operations
- Create industry initiatives to help local PE companies to venture into high growth industries
- Provide advisory support and consultancy
- Technology Transfer
- Develop capabilities and Intellectual Property on process and automation technologies
- Transfer technologies to the local PE industry
- Knowledge Transfer
- Offer specialist skills training: modular programmes
- Organise seminars and workshops
- Showcase & Promotion
- Showcase material, process and product innovation
- Promote business model and operations innovation
- Organise seminars, conferences, roundtables and networking sessions
CAPABILITIES & SERVICES
PE COI offers a wide range of technologies and know-how that cater to diverse markets and industries:
- Forming:
Cold forging, Micro-forming, Precision rotary forming, Liquid forging, Polymer injection moulding, Micro-moulding, Injection/expansion/compression technology, Compounding of polymer, Processing polymer composite, Powder injection moulding of metals and ceramics - Joining and Machining:
Arc welding (including TIG, MIG, and plasma welding) and cladding, Laser welding, Laser Aided Additive Manufacturing (LAAM), Resistance welding, 3D Additive Manufacturing, Diffusion bonding, Brazing, Soldering, Ultrasonic Welding, Adhesive bonding, Sealing and Lamination, Micro/ Nano-joining, Thermal Management, Carbon nanotube and Graphene (dispersion, interconnection, electrode and nano-composites)
Micro-machining, 5-axis machining, Ultra-precision machining, Ultrasonic assisted machining, Cutter development, Gun Drilling, CAD/CAM, Surface finishing, Edge deburring, Laser technologies, Cleaning, Cutting, Drilling, Micro-structuring and Surface modification - Surface Engineering:
Super-hard coatings for wear resistance, dry lubrication, anti-stick and anti-corrosion for use in cutting tools, bearing, wear parts, moulds and dies, Hybrid composite coatings for anti-slip, easy-or self-cleaning and decoration - Mechatronics:
Precision machine design, Motion calibration, Multi-axis motion control, 3D error compensation, Machine vibration control, Automation and robotics - Precision Measurements:
Optic design and simulation, Optical system integration and characterisation, Machine vision system, Image processing, 3D surface measurement, 2D and 3D defect inspection, Metrology and thermal analysis
TECHNOLOGY FOR ADOPTION
The Centre will be a front for industry engagement with SIMTech's technologies; and several initiatives will be rolled out for different segments of the industries tackling different precision engineering issues.
SHOWCASES
- Material Innovation
PE COI assists companies to explore innovating new materials to enhance the performance of processes and products.- Sol-Gel Coating
- High Thermal Conductivity Burn Relief Applications
- Process Innovation
PE COI works with companies to develop innovative processes to manufacture products with cost effectiveness and in shorter time with SIMTech’s manufacturing expertise.- 3D Additive Manufacturing Technologies
- Laser Aided Additive Manufacturing (LAAM) for Repair of Turbocharger Components
- Quick Machining Vibration Solver and Optimiser
- Liquid Forging of High Aspect Ratio Radio Feature Parts
- Spin Forming of High Strength Metal Components Process Innovation of Turbocharger Components
- Customised Tool Grinding, Edge Polishing and In-Situ Measurement System
- Product Innovation
PE COI’s expert consultants and SIMTech’s technologies assist companies to develop new innovative products.- Portable Blood Bag Warmer
- Operations Innovation
PE COI helps companies improve overall operation efficiency and effectiveness by offering solutions to enhance manufacturing operation visibility for decision support.- High Productivity TIG (Tungsten Inert Gas) Welding Technique
- Business Model Innovation
PE COI works with companies to harness technology for business model innovation to keep pace with changing technology and business environment.- From an Equipment Supplier to Service Provider to Information Supplier
For enquiries, please contact
Mr Alex Thoe
Acting Director, Precision Engineering Centre of Innovation (PE COI)
Email: tbthoe@simtech.a-star.edu.sg
A*STAR celebrates International Women's Day
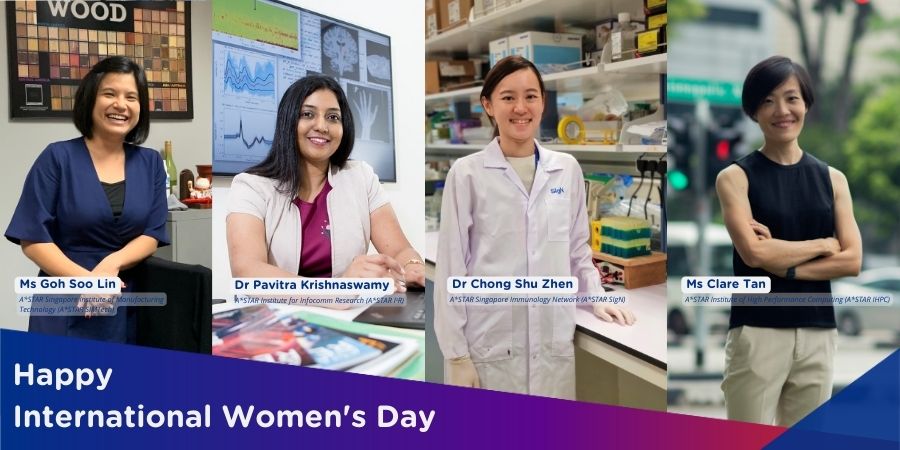
From groundbreaking discoveries to cutting-edge research, our researchers are empowering the next generation of female science, technology, engineering and mathematics (STEM) leaders.
Get inspired by our #WomeninSTEM