RESEARCH IN SIMTECH
Joining and Machining Group
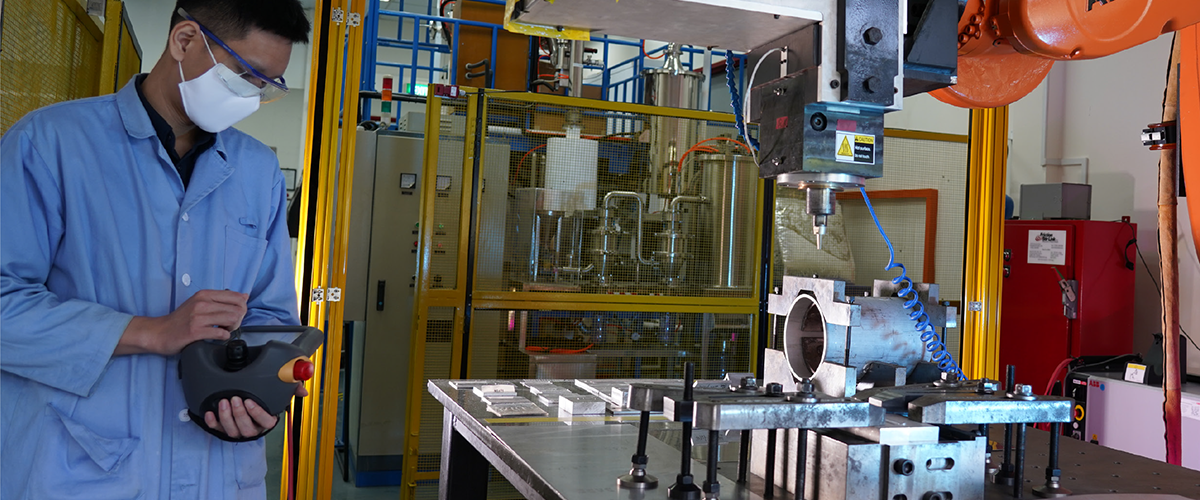
INTRODUCTION
Joining and Machining Group (JMG) focuses on developing new joining, machining and hybrid technologies for polymers, metals and dissimilar materials. The emphasis is on comprehensive study and understanding of physics, chemistry, metallurgy, surface and interface phenomenon, and cutting mechanisms to ensure sound metallurgical quality, precise dimensional accuracy, intricate and high structural integrity. This is achieved by process simulation, machine learning, digitisation, and experimental studies. Joining and machining processes contribute significantly to the performance and integrity of all products, which usually consist of similar or dissimilar materials. Advances in joining, machining and hybrid technologies have enabled a wide variety of materials, such as metals, polymers and ceramics, to be processed together with better efficiency, quality and flexibility.
The group carries out collaborative research with academic institutions, co-develops process technology, transfers technology, and conducts training for the manufacturing industry.
RESEARCH THEMES
Advanced Joining
The advanced Joining research team has good competency in conventional arc welding, friction stir welding, laser welding, hybrid laser-arc welding, lase aided additive manufacturing, micro-joining, transient liquid phase bonding, as well as reliability testing. The team aims to enhance the competitiveness of local manufacturing industry through innovative research, technology commercialisation and manpower training in various metal joining technologies.
Research Focus
- Development of advanced joining processes for polymers, metals and dissimilar materials
- Development of large format free-form laser aided additive manufacturing process, systems and toolpath generation software.
- Machine learning approach for process development and deposition toolpath optimisation.
- Integrated computational materials engineering
- Development of state-of-the-art metal joining systems
- Modification of additive materials
- Process simulation and material testing
Approach
The research team conducts in-house research funded by the core budget as well as national competitive funding to develop the advanced joining technologies. The research team works closely with academia for collaborative research and industry partners for development projects. The team actively promotes technology transfer and manpower training to the manufacturing industry through seminars, training courses and staff T-up.
Precision Machining
The Precision Machining research focuses on the development of advanced mechanical machining and laser machining turn-key solutions to enhance machining efficiency, quality and cost-effectiveness. The team aims to enhance the competitiveness of local manufacturing industry through innovative research, technology commercialisation and manpower training in various machining technologies.
Research Focus
- Ultra-precision machining of freeform surfaces
- Machining dynamics for vibration reduction and chatter avoidance
- Deep-hole drilling technology
- Robot machining for AM components
- Laser surface texturing and surface processing
- Laser precision dicing and drilling
- Laser surface and sub-surface marking
Approach
The research team conducts in-house research funded by the core budget as well as national competitive funding to develop the advanced joining technologies. The research team works closely with academia for collaborative research and industry partners for development projects. The team actively promotes technology transfer and manpower training to the manufacturing industry through seminars, training courses and staff T-up.
CORE COMPETENCIES
- Advanced Joining
- Friction Stir Welding
- Arc Welding
- Laser and Hybrid Laser-Arc Welding
- Micro Laser Welding
- Laser Aided Additive Manufacturing (LAAM)
- Laser soldering
- Transient Liquid Phase Bonding
- Laser Welding of Polymer to Polymer/Metal
- Precision Machining
- Ultra-precision machining of freeform surfaces
- Machining dynamics for vibration reduction and chatter avoidance
- Deep-hole drilling technology
- Internal and external surface finishing
- Laser surface texturing and surface processing
- Laser precision dicing and drilling
- Laser surface and sub-surface marking
TECHNOLOGIES FOR LICENSING AND TRANSFER
- Advanced Joining and Additive Manufacturing
- Laser Aided Additive Manufacturing (LAAM) and hybrid LAAM
- Laser welding and hybrid laser-arc welding
- Laser soldering/brazing
- Micro-laser joining
- Arc welding and wire arc additive manufacturing
- Friction stir welding
- Resistance spot welding, ultrasonic welding
- Precision Machining
- Laser precision dicing and drilling
- Laser surface and sub-surface marking
- Laser singulation of electronics chips
- Ultra-precision machining of freeform surfaces
- Machining dynamics for vibration reduction and chatter avoidance
- Deep-hole drilling technology
- Robotic machining
- Laser Hybrid Processing
- Computer-aided hybrid manufacturing software
- Hybrid process modelling and simulation
- Hybrid process monitoring, inspection, and control
- Laser precision dicing and drilling
- Laser surface and sub-surface marking
KEY ACHIEVEMENTS
- A software “Flex-AM” for 3D printing tool-path planning and machine code generation has been licensed to Osteopore International Pte Ltd. This software helps the company print complex parts with improved quality and increase its manufacturing productivity by five times. With the capability upgrade, the company has extended their business to overseas.
- The patented technology “Powder Feeding Nozzle, Assembly and Method for Laser Aided Additive Manufacturing” has been licensed to DPL Technologies & Services Pte Ltd, a local system integrator. This technology helps the company dominate the market in developing the customised LAAM systems in Singapore.
- Laser soldering system and process has been licensed to IDI Services Pte Ltd for electrical appliances applications.
- SERC IAF-PP funding: Integrated Large Format Hybrid Manufacturing Using Wire-fed and Powder-blown Technology for LAAM Process.
- SG patent application No. 10201805673P: Circular array of conical nozzles with radial exhaust outlets for laser scarfing of composite materials, filed on 29 July 2018
- Best Research Achievement Award: Machining of high-precision roller molds for roll-to-roll embossing and gravure printing, SIMTech, March 2018
- WSH (Workplace Safety and Health) Innovation Award “Gold Medal”: Mobile laser marking system (developed for PEC Pte Ltd), Ministry of Manpower Singapore, 26 May 2017
- Media coverage on the successful CIPs of the quick milling vibration solver with customised software boost for Cragar's productivity, Strait Times, 1 March 2017
- SPIE Rudolf Kingslake Medal Award: SiC optical polishing method, Society of Photographic Instrumentation Engineers (SPIE), 30 August 2016
LISTING OF SOME MAJOR EQUIPMENT/SOFTWARE
- Advanced Joining
- 50W Thulium Laser (wavelength 1900-2050nm) System
- Robot Based Laser Aided Additive Manufacturing (LAAM) System
- CNC Hybrid Additive and Subtractive Manufacturing System
- Robot Based Hybrid LAAM System
- Robot Based Friction Stir Welding System
- Precision Machining
- Moore 5-axis Ultra-precision Machining Centre
- DMU 80P duoBlock 5-axis CNC Machining Centre
- UNSIG 2.0 meter Deep Hole Drilling Machine
- 1.06µm 10W Picosecond Laser
- 335nm 10W DPSS UV Laser
A*STAR celebrates International Women's Day
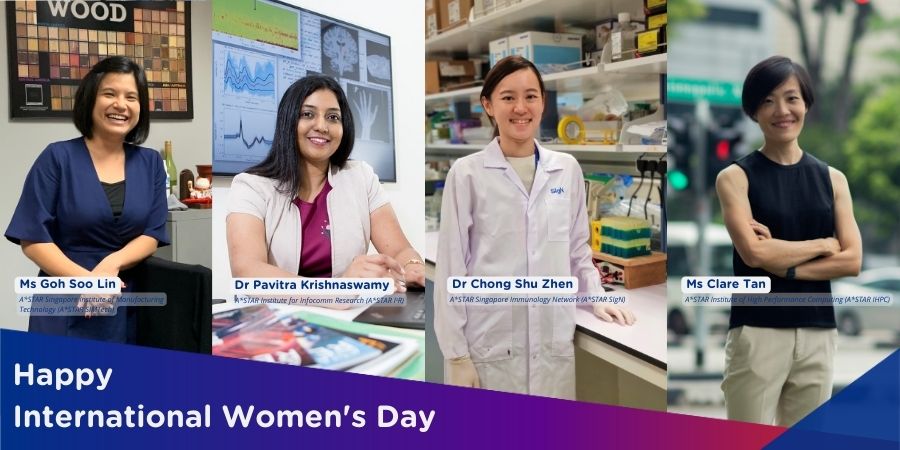
From groundbreaking discoveries to cutting-edge research, our researchers are empowering the next generation of female science, technology, engineering and mathematics (STEM) leaders.
Get inspired by our #WomeninSTEM