RESEARCH IN SIMTECH
Polymer Technology Group (PTG)
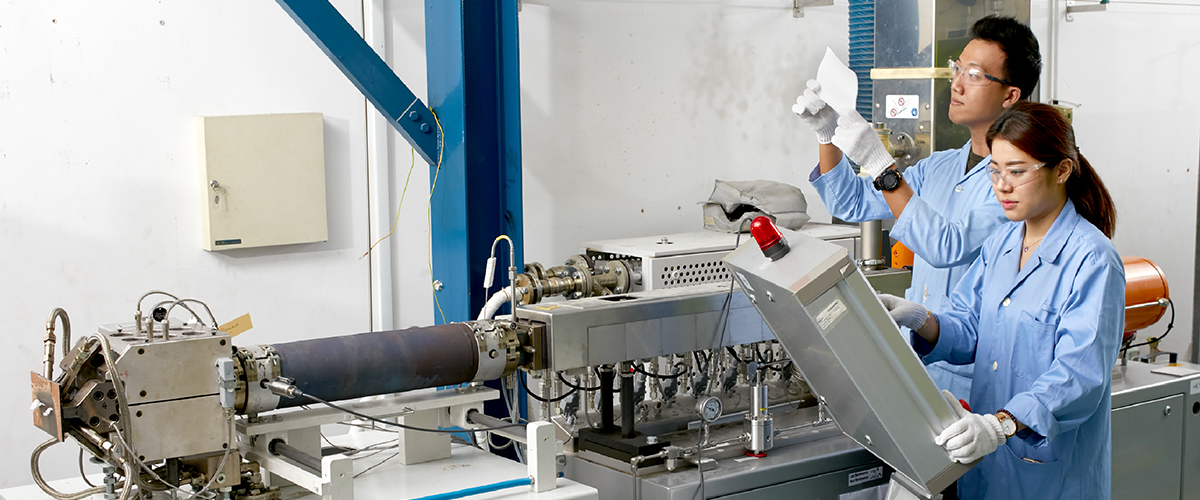
INTRODUCTION
The Polymer Technology Group (PTG) develops near net shape polymer and composite processing technologies, including functional property enhancement, design optimisation and process customisation. The aim is to create dimensionally accurate parts with optimised mechanical properties, while minimising material wastage and manufacturing costs within the process chain.
The group carries out collaborative cutting-edge research with academic institutions, co-develops processes and products with companies, transfers technology and conducts training for the manufacturing industry. PTG welcomes industry partners and industry-minded academic collaborators to work together on innovative research, and process and product development through projects and joint labs.
RESEARCH THEMES
- Polymer Processing
Research encompasses the development and optimisation of manufacturing techniques to produce different formats of polymer products, while making use of waste-valorisation and nano-functionalisation for a wide range of polymer base materials. Processes include additive manufacturing, blend compounding, aerogel processing, foam and film extrusion, vacuum forming and injection compression moulding. We are developing a certified local supply-chain to produce injection-moulded aircraft cabin interior components. - Polymer Composite Processing
Research is focused on the development of material-processing-property understanding to produce fibre-reinforced composites via near-net shape compression moulding and thermoforming processes. The research team concentrates on process, material and design optimisation for thermoplastic composites, hybrid composites and sandwich structures, including consideration of localised high-strength reinforcements with enhanced durability.
CORE COMPETENCIES
- Polymer Processing
- Compounding of thermoplastic blends
- Injection compression moulding
- Foam processing
- Film & sheet extrusion
- Vacuum forming
- Polymer Composite Processing
- Thermoplastic prepreg manufacturing
- Compression moulding
- Composite thermoforming
- Sandwich and hybrid composite processing
- Process Customisation
- Functional properties enhancement
- Hybrid material processing
- Recycled polymer and composite processing
- Process hybridisation
- Directed reinforcement
- Design & Process Optimisation
- Process optimisation
- Moldflow simulation for injection moulding processes
- Design optimisation for lightweight multi-material structures
- Characterisation and validation of structural performance
TECHNOLOGIES FOR LICENSING AND TRANSFER
- Processing Technologies
- Precision injection moulding
- Micromoulding and overmoulding of plastic components
- Extrusion compounding of nanocomposites, sustainable polymers and recycled thermoplastic composites
- Extrusion foaming of polymers using CO2 as physical blowing agent
- Continuous extrusion calendering prepreg manufacturing
- Hybrid/sandwich composite compression moulding
- Thermoforming of plastic and composite sheets
- Material Development & Characterisation
- Flame retardancy for PP supercritical CO2 foams
- Development of nano-cellular foams
- Extrusion-based processing with sustainable materials
- Sustainable thermoplastic composite development
- Design Optimisation and Process Customisation
- Topology optimisation for customised lightweight design
- Characterisation and validation of structural part performance (static / dynamic / fatigue)
- Moldflow simulation for injection moulding process
- Thermal process design for composite thermoforming
KEY ACHIEVEMENTS AND MAJOR PUBLIC-PRIVATE FUNDED ACTIVITIES
- International Patent Application for lightweight structure design. WO2018117971. "Method and system of manufacturing a load-bearing structure and a load-bearing structure manufactured thereof", Filing date: 28th June 2018
- Production Organisation Approval (POA) accreditation (AWI/POA/031) to manufacture parts and articles to be fitted onto Singapore registered aircraft
- SERC Industry Alignment Fund projects:
- Additive Manufacturing Centre (AMC) Initiative;
- Polymer Matrix Composite Programme (PMCP); and
- Technology Development for Suppliers Development Initiative - Natural Fibre Composites
- SERC Strategic Funding:
- Lightweight Structures and Functional Coatings for Aviation Products and Applications;
- Singapore Industry Composite Programme (SICP)
- Joint Labs:
- SIA/SIAEC Joint Lab;
- IMRE - Siam Cement Group (SCG) Joint Lab
- SIMTech-NUS Natural Fibre Composites Joint Lab
LISTING OF SOME MAJOR EQUIPMENT
- Polymer Processing
- Polymer injection and polymer injection compression moulding machines
- Twin screw compounding extruder
- Gas foaming extruder
- Single screw sheet extruder
- Single screw blow film
- Polymer Composite Processing
- Continuous sheet and composite prepreg manufacturing system by extrusion-calendering
- Hydraulic and pneumatic hot presses for composite thermoforming and compression moulding
- IR composite sheet heating system
- Additive Manufacturing
- Powder bed fusion systems: Selective Laser Sintering
- Jetting systems: Binder Jetting, Polymer Jetting
- Material extrusion system: Fused Deposition Modelling
- Vat polymerisation system: Stereolithography
A*STAR celebrates International Women's Day
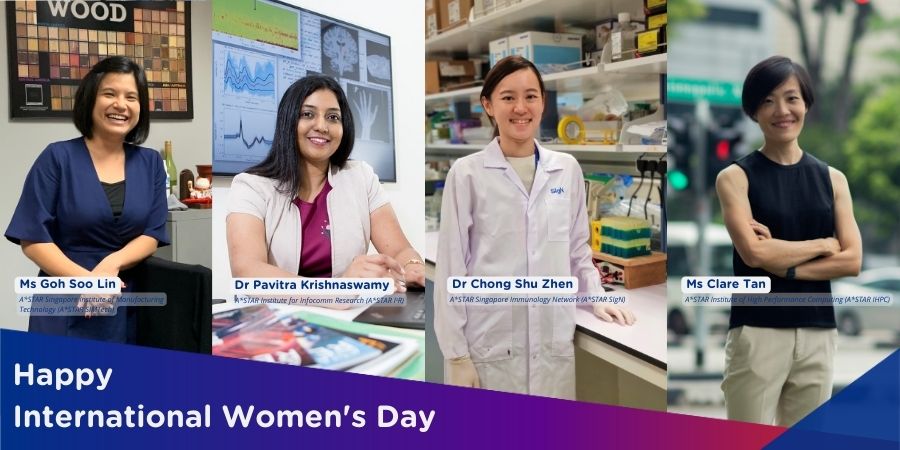
From groundbreaking discoveries to cutting-edge research, our researchers are empowering the next generation of female science, technology, engineering and mathematics (STEM) leaders.
Get inspired by our #WomeninSTEM