RESEARCH IN SIMTECH
Polymer & Composite Processing (PCP)
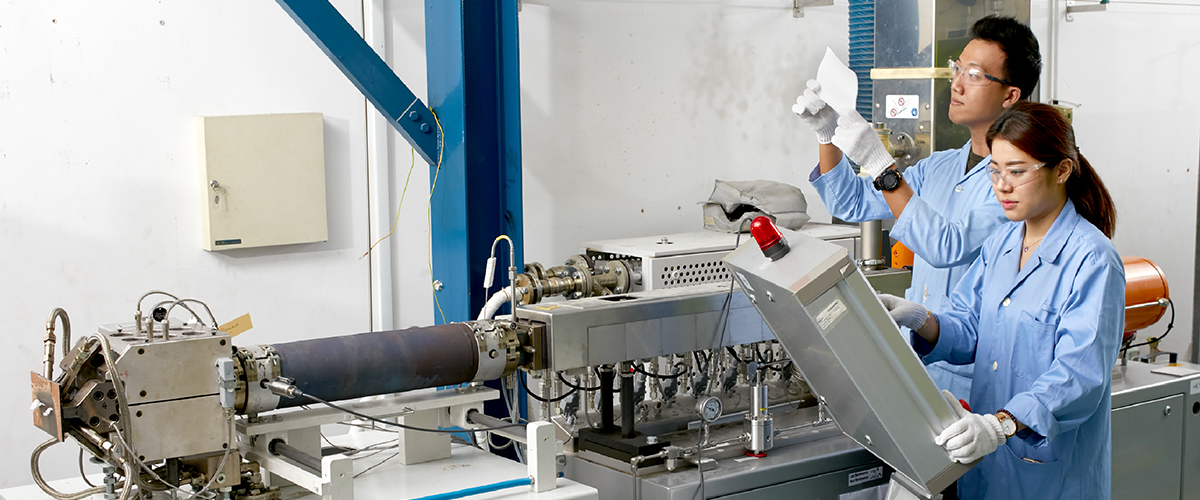
INTRODUCTION
The Polymer & Composite Processing Group (PCP) develops near net shape polymer and composite processing technologies, including functional property enhancement, design optimisation and process customisation. The aim is to create dimensionally accurate parts with optimised mechanical properties, while minimising material wastage and manufacturing costs within the process chain.
The group carries out collaborative cutting-edge research with academic institutions, co-develops processes and products with companies, transfers technology and conducts training for the manufacturing industry. PCP welcomes industry partners and industry-minded academic collaborators to work together on innovative research, and process and product development through projects and joint laboratories.
Focus Research Areas:
- Near-Net Shape Polymer & Composite Processing Technologies
- Functional Property Enhancement
- Design Optimisation & Process Customisation
RESEARCH HIGHLIGHTS
New design and test capabilities towards multi-material hybrid composite part development:
A universal joint utilising carbon fibre reinforced thermoplastic composites with embedded metal inserts was achieved through FE design optimisation of the insert base profile, experimental evaluation of surface treatments and laminate strength, and the development of tool designs and process concepts that supports the fabrication of high-quality parts. Given the right design and process prescriptions, lap shear strengths of greater than 80% was retained at the metal composite interface after 100 thermal cycles.
KEY TECHNOLOGIES
- Processing Technologies
- Precision injection moulding
- Micromoulding and overmoulding of plastic components
- Extrusion compounding of thermoplastic polymers and fibre reinforced composites
- Compression moulding of CFRTP with embedded metal insert
- Hybrid Laminate and sandwich compression moulding
- Thermoforming of unreinforced plastic and fibre-reinforced composite sheets
- Topology optimisation for customised lightweight design
- Characterisation and Validation of structural part performance (static/dynamic)
- Moldflow Simulation for injection moulding process
- Thermal process design for composite thermoforming
- Design for hybrid processing - Extrusion deposition with compression moulding consolidation
KEY FACILITIES
- Injection Moulding Machines
- Injection Compression Moulding
- Microinjection Moulding
- Twin Screw Compounding extruders
- Single Screw Film Extruders
- Vaccuum Thermoforming Machine with Plug Assist
- High Pressure IR Thermoforming Press
- Hot Press
- Hot Bonders
- Drying Ovens (Convection/Vaccuum)
- Tensiometer for Interfacial Surface Energy (<5g Sample)
- Polymer Melt Flow Index (MFI) Testing Equipment
A*STAR celebrates International Women's Day
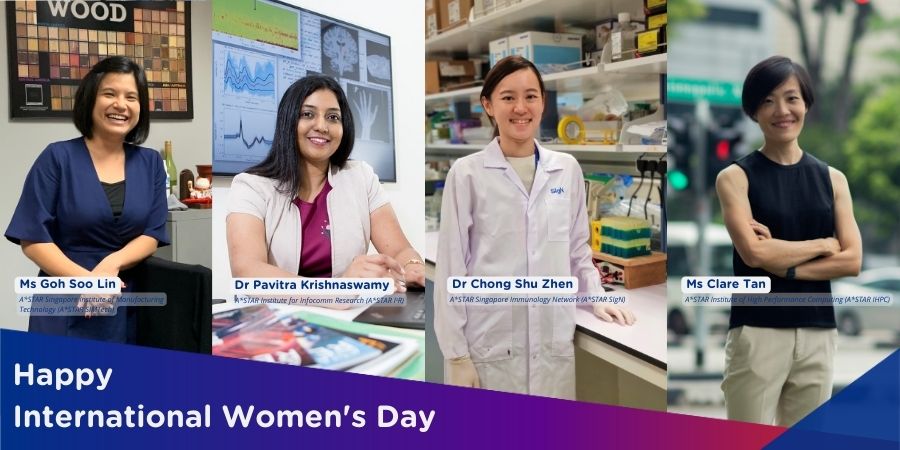
From groundbreaking discoveries to cutting-edge research, our researchers are empowering the next generation of female science, technology, engineering and mathematics (STEM) leaders.
Get inspired by our #WomeninSTEM