Digitalisation of Business Process Workflow* (16 HOURS)
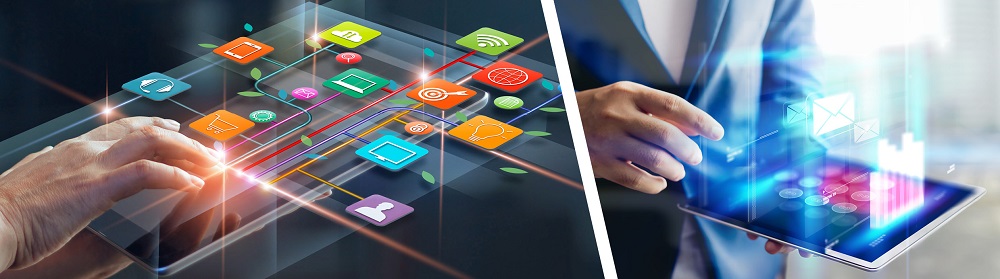
Use Your SkillsFuture Credit Before It Expires! Tap on your $500 SkillsFuture Credit (which expires in December 2025) to offset our course fees! Whether you're upskilling for a career switch or looking to enhance your current expertise, make full use of this credit before it expires and invest in your professional growth today. |
Introduction
With the increasing emphasis of Digital Transformation and productivity improvement for local enterprises, this course is designed to meet the national objectives of providing skills training for process and productivity improvement aiming at Professionals, Managers, Executives and Technicians (PMETs). These PMETs will have to constantly update their skills, knowledge, soft and technical expertise to stay competitive.
Effective workflow design and conversion to a digitalise application workflow using the SIMTech Digital Workflow Automation products for testing of the candidates’ processes will be a very good learning experience for the students taking up this course. Participants would learn various modeling technique and what is possible in a digital workflow environment.
about the programme
In this programme, participants would gain a holistic understanding of the digitalisation of manual processes and its potential productivity improvement in the daily operational activities, including the reduction of manual tracking of processes and time saving from automating the reporting of process performance.
Expected learnings by participants:
- Document the manual work processes into a digital model so that this could be translated into a digital workflow
- Perform hands-on modelling of the participant’s current manual work processes, with the guidance from our Digital Workflow automaton experts
- Adopt best practices for workflow process documentation through modelling and refinement after testing and review with end-users
Who Should Attend
The programme is highly relevant for professionals working in organisations including local SMEs from the manufacturing, logistics, marine, process, food, retail etc. It is also recommended to personnel from IT, non-IT, and Operations who are seeking capability enhancement in the workflow digitalisation of the manual processes.
What our trainees say
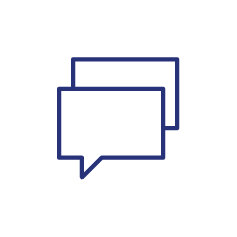
The course prepares me to convert the existing hectic paperwork into digitalisation. It also reduces the need to move around getting approval needs as it is all digitalised. The training and practise moved my thoughts of advancing the existing work mythology to a new digital level.
Mr James Liew,
Participant from Aug 2024 intake
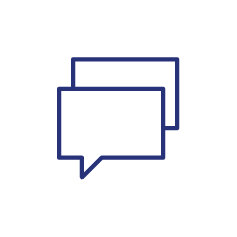
The course instructors and materials were all well-prepared and were instrumental in providing a good learning experience to me. Similarly, the applications shown in the training are useful yet simple to use and will surely aid companies embarking on their digitalisation journey.
Mr James Tan,
Participant from Aug 2024 intake
Our Success Story
Find out how this organisation has benefitted from our partnership in implementing a Digital Workflow Automation System.
About the trainers
Mr Teng Wei Yuen
Ms Nang Hsu Hlaing Mon
Contact Us
- For technical enquiries, please contact:
Mr TENG Wei Yuen,
Email: wei_yuen@ARTC.a-star.edu.sg
- For general enquiries, please contact:
Mr Alex TAY,
Email: alex_tay@SIMTech.a-star.edu.sg
Registration
- Please register for this course through our online form: Course Registration Form for Public Classes.
- For the first question, please select "Modular Programmes (Standalone Modules)".
- Applicants will be placed on our waiting list if the course does not have an upcoming scheduled intake.
- When the next intake is confirmed, a confirmation email with payment information will be sent to applicants to finalise their participation.
Schedule
Note: SIMTech and ARTC reserve the right to change the class/schedule/course fee or any details about the course without prior notice to the participants.
Announcement:
- From 1 Oct 2023, attendance-taking for SkillsFuture Singapore (SSG)'s funded courses must be done digitally via the Singpass App. More information may be viewed here.
- Participants will be provided with digital course materials when attending our courses. Please note that printed copies will not be available.




Quick Link
- View the full list of modular programmes offered by A*STAR SIMTech and A*STAR ARTC.
A*STAR celebrates International Women's Day
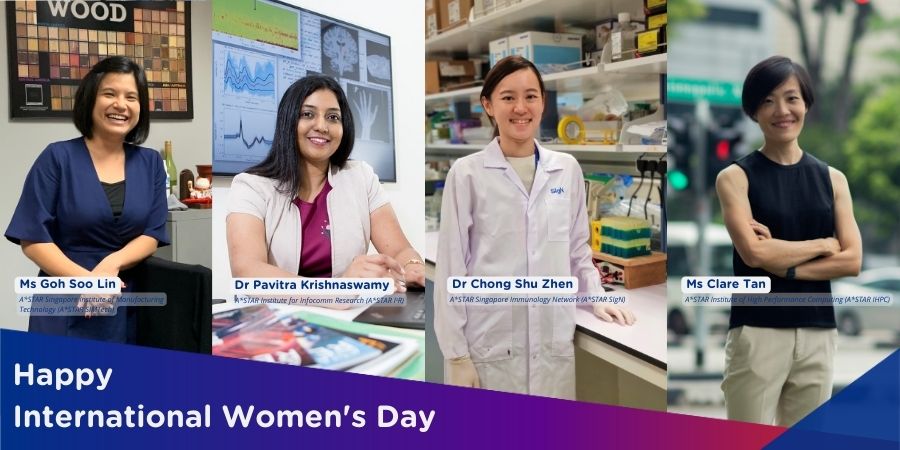
From groundbreaking discoveries to cutting-edge research, our researchers are empowering the next generation of female science, technology, engineering and mathematics (STEM) leaders.
Get inspired by our #WomeninSTEM